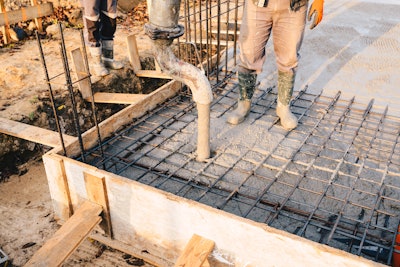
Concrete contractors in 2025 are facing a perfect storm of challenges that are reshaping how work gets done on-site, impacting project timelines, budgets, and workforce stability.
From labor gaps and QC headaches to price spikes and unpredictable pipelines, contractors are under pressure from all sides in 2025. Success this year means staying flexible, adopting tech that boosts efficiency, and forging tighter collaboration across the supply chain.
Rising Material Variability and QC Disputes - Inconsistent material sources and growing reliance on performance-based specs have led to a spike in quality control issues. Discrepancies between ready-mix producers and third-party testers are leaving contractors caught in the middle, often bearing the cost of disagreements. In several cases, misaligned test results have led to full concrete removals and re-pours, pushing back schedules and inflating costs.
Skilled Labor Shortage - The labor crunch remains severe. With an aging workforce and fewer younger workers entering the trade, contractors are stretched thin across projects. Crews are often split across multiple sites, impacting both productivity and concrete finish quality, especially in harsh weather regions like the Northeast or hot climates where night pours are common. One Texas contractor reported major delays on an infrastructure project due to a lack of skilled finishers, leading to missed milestones and rework due to uneven finishes.
Sustainability Pressures - Sustainability mandates are now landing squarely on contractors’ shoulders. From sourcing low-carbon concrete to tracking environmental performance, meeting green targets adds complexity to an already tight workflow. For many, aligning with environmental goals while keeping projects on time and within budget is proving to be a difficult balance.
Rising Costs and Supply Chain Disruptions - Global tariffs on steel, aluminum, and other key materials have sharply raised prices, with 87 percent of contractors reporting cost hikes in 2025. Nearly a quarter have faced delays or cancellations due to material shortages. These price pressures, combined with longer lead times and occasional shipping delays, are making it harder to manage budgets and project schedules.
Economic Uncertainty - Fluctuating interest rates and policy shifts under the new U.S. administration have created uncertainty in the private construction sector. While infrastructure and data center work are booming, sectors like office and residential construction have cooled, creating uneven pipelines. Many firms entered 2025 with strong backlogs but concerns about a slowdown or recession are forcing cautious spending and conservative planning.
Addressing the Challenges
Concrete contractors in 2025 are stepping up with a mix of people-focused strategies, tech adoption, and smarter project planning to confront the industry’s most pressing issues, especially the skilled labor shortage, supply chain pressures, and rising costs.
While the solutions aren’t universal or instant, the industry is making real strides. From smarter sourcing and targeted upskilling to digital tools that lighten the workload, concrete contractors are adapting with resilience. The road ahead remains complex, but 2025 is showing that innovation and long-term thinking are moving the needle.
Workforce Development & Retention - To combat the ongoing labor shortage, contractors are expanding apprenticeships, offering referral bonuses, and partnering with trade schools. On-site mentorship is helping transfer knowledge from seasoned workers before they retire. While progress has been slow given the structural nature of the shortage, efforts are starting to pay off. Construction employment grew 1.7 percent this year, and higher wages have helped with retention. Still, training is a long game, and small firms in particular face challenges scaling these efforts.
Smarter Cost and Supply Chain Strategies - Faced with volatile material prices, many contractors are building relationships with multiple suppliers, sourcing more locally, and purchasing in bulk to avoid delays. Index-linked contracts are becoming more common, helping firms manage cost fluctuations with clients. These actions have helped reduce some of the shock of 2025’s tariff-driven inflation. While price pressures remain, improved procurement practices and inventory planning have helped avoid the worst delays.
A Pivot Toward Public Projects - With interest rates cooling private investment, many firms are shifting focus to infrastructure and public-sector work like schools, highways, and municipal builds that benefit from government funding. Bids in this sector are up over 3 percent this year and have helped stabilize backlogs. This move has proven critical to maintaining workflow during economic uncertainty.
Tech Adoption to Stretch Labor - Contractors are leaning heavily on tools that boost efficiency. Project management platforms, real-time monitoring (like concrete sensors), BIM, and drone surveys are streamlining workflows and improving quality control. Prefabrication is also gaining traction to reduce on-site labor needs. Though not a silver bullet, these solutions help teams do more with less and firms using them report fewer delays and tighter coordination.
In-House Quality Control & Dispute Prevention - To reduce dependency on external labs and minimize QC disputes, some contractors are training their teams to perform basic material testing. This on-site validation keeps projects moving and prevents costly rework when third-party results conflict with mix producers. It’s a proactive step that’s reducing friction on site.
Upskilling and Fast-Track Training - Trade associations and contractors are offering intensive bootcamps and accelerated training programs to get new workers job-ready faster. These programs are showing impact, particularly for formwork and finishing roles, though affordability and access still vary widely.
Working the Skilled Labor Problem
Despite record-high construction employment in 2025, surpassing even mid-2000s levels, concrete contractors are still struggling to fill skilled roles. The U.S. industry employs over 8.3 million people, yet many contractors can’t find enough qualified workers for critical positions like finishers, formwork carpenters, and site supervisors. Unemployment in construction is extremely low, and firms are holding onto every team member they have. Layoffs are rare, not due to slowdowns, but because replacing skilled talent is nearly impossible.
The Core Problem: A Chronic Skilled Labor Gap - The industry faces a structural labor shortage, not just a temporary one. More than 20 percent of U.S. construction workers are over 55 and retiring fast. Meanwhile, younger generations are entering the trades at a slower pace, deterred by outdated perceptions, academic pressures, and competing industries. Even when new candidates show interest, they often lack the specific skills or certifications modern jobs demand, like operating laser screeds or using BIM tools. This growing mismatch has become a key cause of project delays, overtime costs, and even safety concerns.
Wages Are Up, But So Are Pressures - To attract and retain talent, contractors are raising wages; construction workers now earn nearly 19 percent more than the average U.S. worker. But while this boosts retention, it also squeezes margins. In some regions, bidding wars have broken out over experienced concrete supervisors and foremen, driving up labor costs even further.
Contractors Are Adapting, But It’s Not Easy - Companies are responding with a mix of short- and long-term strategies. Many are investing in apprenticeship programs, on-site training, and trade school partnerships. Referral bonuses and mentorship programs are helping bring in new workers and keep existing teams engaged. Some contractors are even using technologies like lifting robots, rebar-tying machines, and exoskeletons to make jobs less physically demanding and reduce burnout.
Others are being strategic by bidding selectively, extending project timelines, or adopting lean planning models to maximize efficiency with smaller crews. The emphasis is on getting more done with less, without overworking limited staff.
Tech Can Help, But It’s Not a Silver Bullet - Automation and digital tools are being adopted to reduce manpower needs. Robotic layout systems, drones, and prefabrication are seeing traction, especially on large commercial jobs. But adoption is uneven, costs, training time, and ROI concerns still pose barriers for smaller firms.
The bottom line is that construction employment is strong, and contractors are doing what they can to adapt, but the skilled labor shortage remains one of the industry's most stubborn hurdles. Until there’s a broader shift in how the next generation views construction careers, and greater investment in vocational training, contractors will continue building in a tight labor market.
Pouring in 2026
The concrete industry is bracing for a demanding 2026, with several major challenges converging, many of which are similar to what we’re managing through this year.
Skilled Labor Shortages - The workforce gap will intensify as veteran tradespeople retire faster than new talent enters. Contractors will continue struggling to find experienced finishers, carpenters, and supervisors, forcing higher wages, limited capacity, and slower productivity.
Pressure to Decarbonize - Sustainability mandates are tightening. More clients and jurisdictions will require low-carbon concrete, EPDs, and mix transparency. Contractors must adapt by working with greener materials and mix designs, often without extra budget, making compliance a technical and financial challenge.
Economic Uncertainty - While infrastructure and industrial sectors remain strong, private investment may stay cautious. Contractors will need to navigate thinner margins, uneven market demand, and elevated material and transportation costs that are stabilizing, but not dropping.
Technology Adoption Gaps - AI, BIM, and automation are rapidly evolving, but not all contractors are ready. Training staff, investing in tools, and managing digital change will be make-or-break for many firms. Falling behind could mean lost bids and reduced competitiveness.
This is part 1 of a 3-part series looking at the state of the concrete industry in 2025.