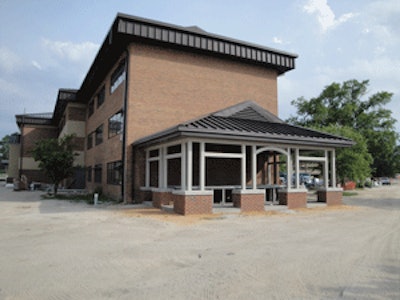
Army training exercises are not typically clean activities. Soldiers often return from the field dirty and their gear caked with mud. When the Fort Jackson Army base in Columbia, S.C., was in need of 60 new outdoor washout tables for its barracks, it wanted structures that could handle a lot of mud and abrasion and be durable enough to support soldiers climbing into the sinks for a pre-shower washdown. General contractor on the job, McCarty Corp., Austin, Texas, found the base a solution with precast concrete.
The general contractor contacted PreiTech Corp., manufacturer of EPS concrete countertop forms that include a proprietary plastic coating for a smooth, bubble-free finish. "Urethane molds would have been expensive with the size of the tables they wanted, and wood mold construction would have been very time consuming," says Mike Eastergard, president of PreiTech.
PreiTech produced the 4-foot by 8-foot molds, each 4 inches thick with a shallow reverse indentation slope toward the middle of the table to accommodate a drain. The thinnest part of each table was 2.5 inches thick at the site of the drain. PreiTech also produced a mold for a 4-inch custom rail around each table.
The mix
The three-man McCarty crew used Quikrete's Countertop Mix, a self-consolidating concrete mix designed specifically for countertop construction. Normally available in 80-pound bags, McCarty special ordered the Countertop Mix in bulk 3,000-pound "super sack" bags. Bulk orders of the Countertop Mix are available on request from any Quikrete plant capable of handling bulk mortar or equipment.
The crew mixed 9,000 pounds of concrete twice a day in the back of a rear discharge ready mix truck. Eastergard explains one of the main benefits of working with Quikrete to secure the mix for a project of this size was it was able to maintain tight quality control measures, which is very important when working with an SCC mix. A mix from a ready mix plant delivered by truck wouldn't have been reliable from batch to batch. "Measuring has to be precise. Mixing on site we didn't have to worry about too much water. They only way you can control that is to be there for 100 percent of the mixing," he says.
The construction process
Eastergard supervised the McCarty crew during the project. They set up at a local industrial warehouse and worked the tables in groups of 20 over the course of two and a half days. On day one they formed out 20 tables, poured them, then formed out the next group of 20. On the second day the crew poured the second group of 20 tables and formed out the third group of 20 tables, which were poured on the third day.
McCarty workers had all the rebar prebent and tack welded for each table. The crew poured each table three-quarters of the way full, placed the rebar mat, then finished the pour.
The tables were then covered with burlap and left to cure for 30 days in the temperature-controlled warehouse. The McCarty crew returned to wet down the slabs after day 1, day 2, day 4, day 7, day 14 and day 21. "They wet the slabs for a slow cure in order to minimize any cracking," Eastergard explains.
Installation
After the 30-day curing period, the McCarty crew used forklifts to load the tables onto a flatbed truck and cushioned them with Styrofoam. As insurance, the crew made five extra tables to replace any that broke during transportation; only three tables broke during the drive from the warehouse to the installation site.
Once the tables made it to the Army base, the crew stripped the forms and lowered the tables with a crane onto U-shaped concrete legs. Minimal finishing was required. "The crew spent only about 20 minutes detailing the tables after the forms came off. They used a grinder to knock off any sharp edges around the side and bottom of the tables," Eastergard explains. "Using the SCC mix eliminated 99 percent of the detailing work on the back end of the project."