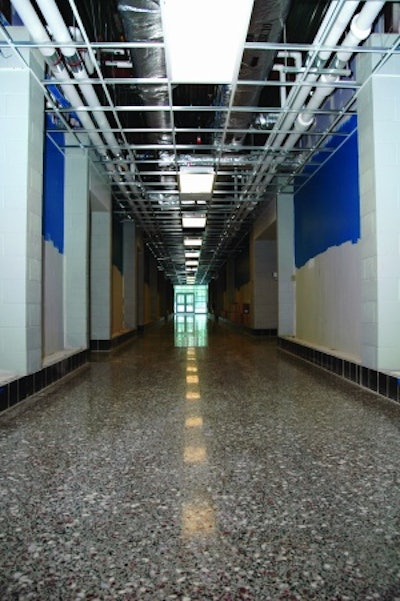
Although the James M. Bennett High School in Salisbury, Md., will not be submitted for certification through LEED, the Wicomico County Board of Education knew that all future schools built in the district would have to earn LEED certification. With maintenance budgets shrinking and LEED in the back of the owner's mind, the architect set out to find a flooring solution that fit into LEED requirements, would be aesthetically pleasing and would require less maintenance than traditional VCT (vinyl composition tile). The solution was to use the existing concrete sub floor and mechanically process and highly refine the surface to a polish with diamond abrasives for a polished concrete floor.
My company, Cuviello Concrete, was selected as the subcontractor to process the concrete to a polished finish. The job consisted of 41,000 square feet of corridors of uncolored concrete, a 7,000-square-foot black integrally colored cafeteria, 7,000 liner feet of edges, 463 corners and 3,159 linear feet of saw cut joints.
The polishing project was originally bid to receive a multi-colored dye application. Due to a concern as to how well the specified dyes would hold up to long-term ultra violet light, vapor transmission, pH variations in the concrete and the possibility of improper maintenance, the architect and school board decided to remove the dye application. For aesthetic appeal, they instead opted to use colored glass in school colors - red and white - and other decorative aggregate seeded into the surface at the time of placement. The surface would be ground to expose the seeded aggregates, honed and polished to a 1,500-grit finish.
A pre-planning project meeting was held with all parties whose work would affect the outcome of the finished floor. The meeting included the owner, architect, general contractor, concrete flooring subcontractor, the ready mix producer and me, the polishing subcontractor. In the meeting I explained how the aggregates would need to be seeded along with mix design and finish work requirements. I also emphasized the goal of the floor was not to achieve a finish that would resemble terrazzo but to achieve a consistently inconsistent exposure of aggregate; any expectation of a terrazzo consistency would set me up for failure and everyone else for disappointment.
Together with the concrete flooring subcontractor, my team produced a mock-up showing various densities of glass and aggregates that ranged from one half pound up to a pound and a half per square foot. Over the next several months the concrete flooring contractor poured the floors and seeded the aggregate by staging it in 5-gallon buckets every 10 feet along the pour, ensuring each area would receive the same amount of aggregate.
A floor protection plan protected the floor in the 18 months that spanned the time between the floor pour and the polishing. A janitorial-grade acrylic floor finish was applied to help protect the slab from stains. In addition, all trades were told they were working over a finished floor and that anyone caught cutting pipes, running equipment that was not diapered, or did damage to the surface from negligence would result in a back charge.
On the job
In the initial grinding phase we used a Prep/Master 4430 to grind the concrete anywhere from 1/8 inch to ¼ inch. To finish the grinding phase and throughout the honing and polishing phases we used two Lavina 32 Pro units. With the initial grinding steps being the most demanding we chose to use the Prep/Master 4430 because of its gear drive, weight for heavy grinding, 44-inch grinding path and ability to refine the floor through the use of 24 abrasives being driven in an intertwining rotary motion. The Lavina was chosen because it is lighter, easier to finesse into smaller areas and quickly refines the floor through the use of 18 abrasives being driven by six individual satellite heads in a planetary motion.
The abrasives used under each machine were produced by the individual equipment manufacturers and designed for optimal performance based on the characteristics of the machine. Each abrasive used refined the concrete to the maximum potential before moving to the next. Refinement of each grit went beyond simply replacing the scratch patterns from the previous grit. You know when you have refined the concrete with each grit to its maximum potential when the slurry becomes translucent and there is no visible scratch pattern to the naked eye. Maximum refinement is critical when reaching for a floor that will have a crisp, clean appearance with maximum clarity of overhead reflection; it is also as import to the floor's durability.
The densifier on this project was from RetroPlate. Application of a densifier is based on the absorbency of your project's concrete; on this job we typically applied the densifier after our 100-grit resin pass. To continue with the floor protection plan started before the polishing began, once my team completed each area of the floor the general contractor laid down a temporary floor protection system to protect the finished surface.
One of our primary challenges on this job was grinding to expose aggregate then honing and polishing the edges flush to the existing finished block. This was done with a combination of stand-up edge machines and four finishers on rolling carts using various shapes and sizes of abrasives and hand tools. The ground floor was built slab-on-grade and the joints were filled with VersaFlex SL 75 polyurea.
Another considerable challenge was handling the excessive amounts of slurry produced from the deep grinding operation. During the first half of the job slurry was pumped into a lined dumpster with sump pumps. This became costly, messy and ultimately counterproductive when the hoses started to freeze due to winter working temperatures. The solution came in the way of a water/slurry separator that allowed reuse of the filtered water and easy disposal of ground concrete patty cakes. The cakes were disposed of in the trash dumpster along with all other construction debris.
When completed, we left the school with a maintenance plan that addressed the use of entrance matting, vacuuming loose dry debris with backpack vacuums, mopping with micro fiber pads, the use of Diamond Bright Polished Concrete Cleaner (a slightly alkaline cleaner) and burnishing the floors with a polished concrete maintenance pad.
With the efforts of all parties involved the finished floor exceeded the owner's expectations.
Project at a Glance
Owner: Wicomico County Board of Education
Architect: Becker Morgan Group, Inc.
General Contractor: Whiting-Turner Contracting Company
Flooring Subcontractor: Harkins Concrete Construction
Polishing Subcontractor: Cuviello Concrete
Key products and equipment:
RetroPlate densifier; ProGuard Dura Cover; Substrate Technology's Prep/Master 4430; Superabrasive's Lavina 32 Pro; VersaFlex SL 75 polyurea; Adhesive Systems Technology Corp. application unit; finisher carts from RACATAC Products; GOLZ Slurry Fox water/slurry separator from Substrate Technology Inc.; L.M. Scofield integral color; Heritage Glass.