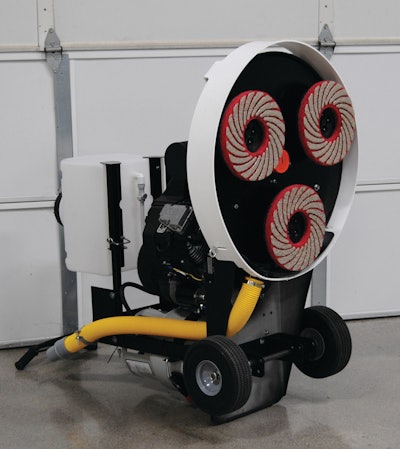
I recently returned from a trip and noticed one thing that has not changed in hundreds of years, re-enhancement of every type of building, surface and everything in between. When applying this to our industry it reminds us that each and every floor out there needs some sort of “facelift” or beatification in order for it to last the test of time.
Let’s first start with the “why” would this be needed in today’s industry? Since the emergence of finished concrete floors, the industry has taken a turn for the better by offering proper education on the actual process of polishing concrete to the maintenance procedures that are now being recommended. All surfaces, not just concrete surfaces, take abuse every single day. In some cases they take extreme abuse due to their simple location. We've all seen the salt attack on a concrete floor in the entry areas of buildings or the abuse of a store next to the beach.
To bring this into simple perspective: Without proper walk off mats:
- 1,000’s of people and their carts, strollers and shoes will track into an entry area 1.2 pounds of dirt and abrasives per day.
- On wet days this increases to 3.6 pounds of dirt and abrasives.
- 1,000’s of people will remove up to 42 percent of the floor finish per year.
- Abrasives are the major cause of floor wear in our industry.
The industry has taken the proper steps to help educate owners, architects and themselves on how to actually extend the life of a concrete surface. In order for the “enhancement” process to work, the finished concrete floor needs to be properly processed in the beginning.
According to SASE Company’s Vice President of Sales, Greg Ferchaud, “These lighter weight machines are here to work the surface of a properly diamond ground and polished surface using heavy planetary machines with the proper diamond tooling on them. They will not replace these machines or the work they do.”
There have been a lot of advancements in diamond tooling and the way that floors are processed, some with just marketing behind them and others that have been proven through time. Today, with the growing number of manufacturers, applicators and support, guidelines have been worked on to actually define the grinding, honing and polishing process. Manufacturers that lead the industry, SASE Company, Ameripolish, Metzger Mcguire, PROSOCO, Inc. and others have worked with the CPAA (Concrete Polishing Association of America) and with multiple committees on ACI (American Concrete Institute) — which is the go to entity on concrete in our industry (302, 310 and their respective sub committees). As with most guidelines, manufacturers still work to train and educate each applicator/artisian to actually learn to read each floor since each floor is different and processed differently. SASE Company Inc., National Sales Manager, Marcus Turek states that as the industry evolves, the diamond tooling changes, “We currently have multiple hardness bonds of diamond tooling on our shelves to help serve the contractor. This is due to the way concrete floors are processed today, some extremely hard and others extremely soft and we need to be able to respond.”
Many machine manufacturers that serve our industry have responded and have come out with machines that are light weight, durable and contain the right diamond tooling to help address the need for bringing a polished concrete floor back to life.
Each machine is not actually the same. New machines, tooling and processes have been adapted to handle the harsher environments and respond to what the contractors have requested. Typically these machines weigh around 300 to 400 pounds and are not planetary but work with “free” planetary heads underneath them. Think of a burnisher on steroids. In the picture above you can see that these machines use a water tank to actually add additional weight and the use of water on the steps needed.
During the actual process a floor undergoes a test section to actually determine what steps/diamond tooling will be needed to bring the floor back. Typically most larger retailers want gloss values between 35 to 45 and the newer qualification on DOI (Distinction of Image). All of this is taken PRIOR to any protective treatment that is used to create a false look/reading.
As stated, these machines will not replace the use of a 1,000 pound machine or the tooling that they use. Typically the best tooling used is on a flexible pad that allows the lighter weight machines to actually follow the surface and hit all “peaks and valleys” and provide constant contact with the floor. As with any surface that you are processing, each chemical manufacturer recommends to re-densify the surface properly and according to manufacturer’s instructions. Read the floor and apply to rejection on any densifier you use.
Once the surface has been “re-enhanced” to meet the owner’s expectations, the use of a protective treatment will ensure your floor will once again gain the durability look your owners, architects, and consultants will accept.
In closing, not all machines are the same and you will need to work with your machine manufacturer to determine what equipment will work for you and your company. The right choice on tooling will ensure your efforts are rewarded. Don’t go at it alone, there are many resources in the field, pick yours and work with them as they are there to help.
Happy enhancing!