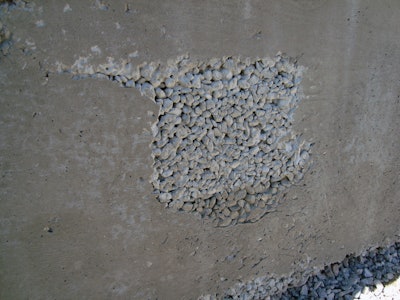
Honeycomb, subsidence cracks, cold joints and excessive surface air voids are common surface blemishes associated with ineffective concrete consolidation. In addition to being unsightly, formed surfaces with blemishes may not conform to the requirements of the contract documents. When this occurs, surface blemishes become defects and subsequently must be repaired. Along with the expense of repairing surface defects, it is difficult and sometimes impossible to make repairs match the color and texture of the surrounding concrete. By understanding the causes and using effective consolidation techniques, contractors can avoid repair costs and aesthetic disputes due to consolidation-related surface blemishes.
Stages of consolidation
Two stages of consolidation: leveling and de-aeration. Due to the oscillatory energy waves, entrapped air bubbles are driven to the form face and move upward to escape.
In the second, or de-aeration stage, the remaining entrapped air bubbles rise to the surface and escape, especially the large bubbles. It is not possible to remove all the entrapped air bubbles; however, vibration should continue until the cessation of large air bubbles occurs.
Use the largest and most powerful internal vibrator, systematically vibrate the concrete area through the full depth of the lift being sure to penetrate the previously lift, and limit the distance between insertions so the area visibly affected by the vibrator overlaps the adjacent just-vibrated area. Continue vibrating until the coarse aggregate particles become embedded, a thin film of mortar forms on the top surface and along the form faces, and large air bubbles stop escaping from the surface.
Also, listen to the pitch or tone of the vibrator. When the vibrator is first inserted into the concrete, vibrator frequency drops but then increases and finally becomes constant when the concrete is free of entrapped air bubbles.
Many times, untrained operators only level the concrete and fail to complete the de-aeration phase of consolidation resulting in unwanted surface blemishes. It is important for operators to understand the stages of vibration and indicators of well-consolidated concrete.
Avoid honeycombing by using appropriate concrete mixtures with sufficient workability, proper placement and consolidation techniques.
Honeycomb
Honeycomb occurs when mortar fails to completely fill the spaces between the coarse–aggregate particles leaving irregular voids or stony zones in the concrete. Typically, honeycombing occurs along the form face and in many cases is limited to the region between the form face and reinforcement. Causes include: congested reinforcement and narrow forms, insufficient paste due to segregation of the concrete, improper fine to coarse aggregate ratio, improper placement procedures (excessive concrete free fall and lift thicknesses), trying to place stiff and dry concrete, difficult construction conditions, and insufficient consolidation efforts.
Subsidence cracks
Sometimes called plastic settlement cracks, subsidence cracks occur when additional settlement or consolidation occurs after the freshly placed concrete has been vibrated and finished. Causes of delayed settlement include excessive bleeding and incomplete concrete consolidation. Cracks form in the plastic concrete because of some type of restraint that restricts concrete settlement. Subsidence cracking in columns and walls commonly occurs over fixed items such as tie bolts and reinforcement and in columns and walls where settlement is restrained by wedging or arching of the concrete. Deep concrete sections are more prone to subsidence cracking.
This form of plastic cracking can be minimized by using proper placing and consolidation procedures and essentially eliminated by revibration. Revibration is not harmful, can mend subsidence cracks and reconsolidate concrete after delayed settlement has occurred. If the vibrator can be inserted into the concrete and removed without leaving a hole, it is not too late to revibrate the concrete.
Lift lines are typically caused by color variations between two success lifts of concrete. Lift lines can be minimized by completely knitting successive lifts of concrete together.
Cold joints
Cold joints are different than lift or layer lines. Lift lines occur when successive lifts of concrete are not completely knitted together. In many cases, lift lines occur because of color variations between loads of concrete and do not indicate there is a joint or discontinuity in the concrete.
When a concrete placement delay occurs, try to avoid a cold joint by keeping the top of the placed lift plastic by periodically revibrating. When concreting resumes, place a short lift and thoroughly vibrate the two lifts together.
In contrast, a cold joint is a discontinuity between two lifts of concrete. They occur when, due to a concrete placement delay, the earlier lift of concrete hardens sufficiently to preclude knitting and bonding of the two lifts. Except for the unsightly appearance, cold joints are typically not a concern unless the concrete is unreinforced or an environmental tank.
Surface air voids or bugholes are acceptable for vertical cast-in-place concrete walls and columns unless voids exceeds the maximum allowed size.
Surface air voids
Commonly called bugholes, surface air voids are small, regular or irregular cavities, usually less than 5/8 inch in diameter, caused by entrapment of air bubbles in the surface of formed concrete. Bugholes are normal for vertical cast-in-place concrete and not considered a defect unless voids exceed the maximum size specified by the contract documents.
Minimize bugholes by using: smooth, impermeable formwork; the thinnest coat possible of an appropriate release agent; limited lift thicknesses; high-frequency vibrators; and proper vibrating procedures with sufficient periods of vibration to de-aerate the concrete.
References:
ACI 309R-05 Guide for Consolidation of Concrete, American Concrete Institute, www.concrete.org
ACI 309.2R-98 Identification and Control of Visible Effects of Consolidation on Formed Concrete Surfaces, American Concrete Institute, www.concrete.org