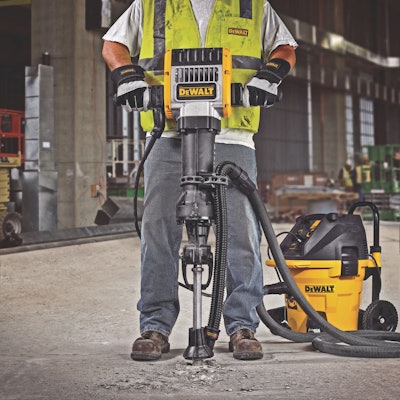
Crystalline silica is a basic component of sand, quartz, slate and other minerals. Exposure to airborne crystalline silica can put workers at risk of developing silicosis, a non-curable lung disease caused by accumulation of silica dust in the lungs. The dust embeds itself in the lungs and causes scar tissue to form. The scar tissue reduces the lungs’ ability to take in oxygen. Each year, 300 people die from silicosis.
Concrete and masonry products contain silica sand and rock containing silica, leaving many construction workers susceptible to respirable crystalline silica exposure during these workday activities:
- Chipping, hammering and drilling rock
- Crushing, loading, hauling and dumping rock
- Abrasive blasting using silica sand as the abrasive
- Abrasive blasting of concrete (regardless of abrasive used)
- Sawing, hammering, drilling, grinding and chipping concrete or masonry
- Demolition of concrete and masonry structures
- Dry sweeping or pressurized air blowing of concrete, rock or sand dust
The Department of Occupational Safety & Health Administration (OSHA) has specific regulations for concrete cutting and dust containment: regulation 29 CFR 1926.55 Gases, vapors, fumes, dusts and mists. Within that regulation it states employers are required to “avoid” employee exposures to silica beyond permissible exposure limits (PELs) and also required to implement controls to minimize or eliminate exposure. If an employer suspects silica dust may be present on a jobsite, OSHA requires that employer to communicate the risks to employees whether or not it is known for sure. It is important to be aware that airborne crystalline silica may be present even if no dust can be seen.
Engineering controls
OSHA specifies that an employer must “implement the best possible permanent solution” for reducing and/or eliminating crystalline silica dust. When silica exposure cannot be eliminated, OSHA suggests three methods of controlling silica exposure when cutting concrete: engineering controls, improved work practices and use of PPE. Engineering controls, the preferred of the three methods, keep silica dust out of the air through mechanical means such as:
- Installing a water hose to wet down the dust at the point of generation
- Installing local exhaust ventilation
- During rock drilling, flowing water through the drill stem
- Installing dust collection systems on to machines or equipment that generates dust
- Using concrete/masonry saws that provide water to the blade
Increased emphasis
In recent years, the concrete industry has seen an increased emphasis on concrete dust suppression and containment. This buzz was created by a few things, namely OSHA’s current National Emphasis Program on Crystalline Silica (which has been in effect since Jan. 24, 2008), talk of stricter regulations and contractors wanting greater dust suppression capabilities, both for safety and jobsite cleanliness.
Chris McCutchen, chief operating officer for CDCLarue Industries, Inc., says the EPA’s Lead Renovation, Repair and Painting (RRP) Rule from two years ago signals where those regulations might go. “Right now, new PEL ratings are sitting at the Office of Management and Budget waiting to be signed into law. [The construction industry] doesn’t know what the new PEL ratings will be,” he says. “There is a lot of speculation that suggests the EPA will bring concrete PEL ratings down to the same PELs as asbestos and lead. If they do that, contractors will need to use vacuums to control concrete dust.” An OSHA spokesperson confirmed it expects to issue a proposed rule for crystalline silica, which includes revised PELs, in May 2013.
Jeff Beck, product manager with DeWalt, has heard similar talk in the industry, but also sees safety as a driving factor in increased dust suppression on jobsites.
“We keep hearing that OSHA is going to lower the PELs and enforce them more, but we haven’t seen that yet,” Beck says. “What we have seen is more awareness by some of the larger contractors on the dangers of silica dust and a concern on their part to try to mitigate some of that exposure to their employees.”
Other reasons for greater interest in dust suppression equipment is the increased number of retro and refit projects throughout the country, where a business or industrial facility might keep a portion of its building open and functioning during reconstruction. In those situations, dust containment is necessary to prevent dust exposure to customers and retail goods, or workers and manufacturing equipment. Additionally, contractors understand less dust to clean up on a jobsite results in labor savings.
Choose the right tools
In recent years, equipment manufacturers have added or improved features and mechanisms that help contractors control dust on the jobsite. Saws and drills used in the concrete sawing and drilling industry include water feeds that both keep dust down and cool and lubricate the cutting tool. Tool manufacturers and manufacturers of after-market dust-collection systems have added and/or improved dust shrouds, sleeves, industrial vacuums and other dust control options in recent years.
DeWalt took a unique approach to helping contractors choose safer concrete cutting, drilling, chipping and grinding equipment when it launched its Perform and Protect line in late 2012. These products aren’t necessarily new to the industry, but their inclusion in the Perform and Protect line makes it easier for contractors and safety managers to identify products with heightened safety features.
“Our Perform and Protect brochures are targeted toward safety managers so they can identify our tools that have a better level of protection for torque management, vibration control and dust suppression,” Beck says. Introduction of the line, which will be launched globally at Bauma in Germany in April, includes a comprehensive website describing the tools and their technologies and special Perform and Protect branding that makes the products easy to identify.
Despite unknown limits on the forthcoming regulation on permissible jobsite silica exposure, a tightening of these rules seems eminent. Manufacturers of dust containment and dust suppression products are meeting the industry’s call for cleaner jobsites with new equipment and product technologies.
Additional information provided by OSHA