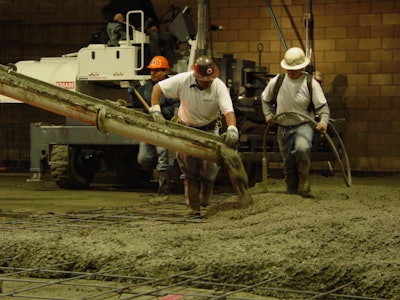
The amount of water in concrete controls many fresh and hardened properties in concrete including workability, compressive strengths, permeability and watertightness, durability and weathering, drying shrinkage and potential for cracking. For these reasons, limiting and controlling the amount of water in concrete is important for both constructability and service life.
Water-cementitious materials ratio
The ratio of the amount of water, minus the amount of water absorbed by the aggregates, to the amount of cementitious materials by weight in concrete is called the water-cementitious ratio and commonly referred to as the w/cm ratio. The w/cm ratio is a modification of the historical water-cement ratio (w/c ratio) that was used to describe the amount of water, excluding what was absorbed by the aggregates, to the amount of the portland cement by weight in concrete. Because most concretes today contain supplementary cementitious materials such as fly ash, slag cement, silica fume, or natural pozzolans, the w/cm ratio is more appropriate. To avoid confusion between the w/cm and w/c ratios, use the w/cm ratio for concretes with and without supplementary cementitious materials. The w/cm ratio equation is: w/cm ratio = (weight of water – weight of water absorbed in the aggregates) divided by the weight of cementitious materials.
Upon hardening, the paste or glue consisting of the cementitious materials and water binds the aggregates together. Hardening occurs because of the chemical reaction, called hydration, between the cementitious materials and water. Obviously, increasing the w/cm ratio or the amount of water in the paste dilutes or weakens the hardened paste and decreases the strength of the concrete. As shown Figure 1, concrete compressive strength increases as w/cm ratio decreases for both non-air-entrained and air-entrained concrete.
Decreasing the w/cm ratio also improves other hardened concrete properties by increasing the density of the paste which lowers the permeability and increases watertightness, improves durability and resistance to freeze-thaw cycles, winter scaling and chemical attack.
In general, less water produces better concrete. However, concrete needs enough water to lubricate and provide a workable mixture that can be mixed, placed, consolidated and finished without problems.
Code requirements
Because w/cm ratio controls both strength and durability, building codes have set upper limits or maximum w/cm ratios and corresponding minimum compressive strengths as shown in Table 1. For example, concrete exposed to freezing and thawing in a moist condition or to deicing chemicals shall have a maximum 0.45 w/cm ratio and a minimum 4,500 psi compressive strength to ensure durability. Designers select maximum w/cm ratios and minimum strengths primarily based on exposure conditions and durability concerns — not load-carrying capacity requirements. For different exposure conditions, use the code required maximum w/cm ratios and minimum strengths to reduce the permeability of the concrete. Doing so will increase the concrete’s resistance to weathering.
Water content and drying shrinkage
The most important factor affecting the amount of drying shrinkage and the subsequent potential for cracking is the water content or the amount of water per cubic yard of concrete. Fundamentally, concrete shrinkage increases with higher water contents. About half of the water in concrete is consumed in the chemical reaction of hydration and the other half provides the concrete’s workability. Except for the water lost to bleeding and absorbed by the base material or forms, the remaining water that is not consumed by the hydration process contributes to drying shrinkage. By keeping the water content as low as possible, drying shrinkage and the potential for cracking can be minimized.
Workability
The ease of mixing, placing, consolidating and finishing concrete is called workability. The water content of the mixture is the single most important factor that affects workability. Other important factors that affect workability include: mix proportions, characteristics of the coarse and fine aggregates, quantity and characteristics of the cementitious materials, entrained air, admixtures, slump (consistency), time, air and concrete temperatures. Adding more water to the concrete increases workability but more water also increases the potential for segregation (settling of coarse aggregate particles), increased bleeding, drying shrinkage and cracking in addition to decreasing the strength and durability.
Adding water onsite
If measured slumps are less than allowed by the specifications, slumps may be adjusted by a one-time addition of water. However, there are requirements associated with adding water onsite:
- Do not exceed the maximum water content for the batch as established by the accepted concrete mixture proportions.
- No concrete has been discharged from the mixer except for slump testing.
- All water additions shall be completed within 15 minutes from the start of the first water addition.
- Water shall be injected into the mixer with such pressure and direction of flow to allow for proper distribution within the mixer.
- The drum shall be turned an additional 30 revolutions or more at mixing speed to ensure a homogenous mixture.
Before adding water onsite, the allowable amount of water that can be added must be known. This amount should be printed on the delivery ticket or be determined during the pre-construction meeting and be agreed upon by all parties.
Water is a key component in concrete. However, too much water can be detrimental to both the fresh and hardened concrete properties, especially strength, long term durability and potential for cracking. On your next job, be sure to know the water requirements for the concrete mixtures being used, especially the allowable water that can be added for slump adjustments.
References
Kosmatka, S. H., and Wilson, M.L., Design and Control of Concrete Mixtures, 15th edition, Portland Cement Association (PCA), www.concrete.org