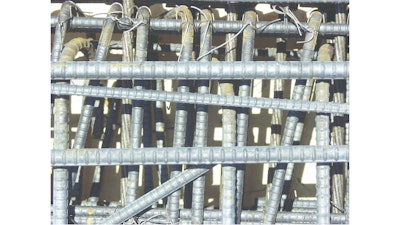
The American Concrete Institute’s 2013 edition of Concrete Terminology doesn’t include a definition for the word constructibility. So let’s look first at a broad definition, then consider a definition that will work for concrete construction.
The Construction Industry Institute (CII) defines constructibility as “the optimum use of construction knowledge and experience in planning, design, procurement and field operations to achieve the overall project objectives.” This definition clearly indicates that experienced construction personnel need to be involved with the project from the earliest stages to ensure their construction focus and experience can properly influence the owners, planners, and designer, as well as material suppliers. This differs from value engineering, which focuses primarily on cost. The design or project objectives shouldn’t be compromised simply to reduce cost. When considered during design, the goal is improved constructibility and the resultant lower cost while still meeting overall project objectives.
CII acknowledges that it is common practice in the industrial/commercial construction industry to develop a project team composed of planners, designers and a variety of construction personnel, whose sole purpose is to review design for constructibility issues. CII also acknowledges what it terms the “review fallacy” that most concrete contractors are familiar with. The “review fallacy” occurs when construction personnel are excluded from the planning process and are invited only to review completed or partially completed products from the designer. Comments usually have to be limited to minor details. CII points out that scope changes at this point are not feasible for a variety of reasons, including:
- Major changes cause delays and increased expenses after significant design costs have already been incurred.
- Designers may be defensive because they have committed themselves publicly on drawings and perceive that any changes would affect their credibility.
The benefits of early constructibility efforts result in a significant payback to the project. CII research has cited cost reductions of between six to 23 percent, benefit/cost ratios of up to 10:1, and large schedule reductions. The intangible benefits are as important as the quantitative benefits and must be recognized accordingly. These include:
- More accurate schedules
- Increased productivity
- Improved sequence of construction
- Enhanced quality
- Decreased maintenance
- A safer job
Concrete contractors don’t often get a chance to participate in early constructibility efforts as these efforts are primarily in the domain of the construction manager. But concrete contractors can assist the construction manager by providing specific recommendations for the constructibility of concrete construction. CII provides some specific recommendations as shown below:
- Standardize shapes to maximize form use
- Provide vibrator space around reinforcing steel to avoid honeycomb problems
- Avoid reinforcing congestion
It’s curious to note that two specific recommendations provided by CII relate to reinforcing congestion and the ability to get concrete and a vibrator through the steel to avoid honeycomb problems (See also “Consider Consolidation in Both Design and Detailing,” pg. 14-15, Concrete Contractor, January 2012 or http://bit.ly/1A0cnwd.) Concrete contractors must deal with limited vibrator access on many projects, but are often told that this is their problem and is not related to design decisions.
The Concrete Reinforcing Steel Institute (CRSI) provides many good recommendations for economical constructibility in its engineering technical note (ETN-C-1-10) “Economical Reinforced Concrete Construction.” There is no charge for downloading this technical note at www.crsi.org. The document provides recommendations in three separate categories:
- Formwork
- Reinforcement
- Concrete
One particular recommendation from CRSI that addresses a CII concern is vibrator access:
- On heavily-reinforced beams such as transfer girders, where the spacing between bars is relatively close, provide a gap. Sometimes bars may be bundled to provide this gap. Experience has shown that four-inch slump concrete with three-quarter inch aggregate will not flow easily through a two-inch space between bars. Similarly, vibrator heads are two to three inches in width and sometimes become entangled in the reinforcement.
Section 8.1 of ACI 309R-05 “Guide for Consolidation of Concrete” suggests that the method of consolidation should be carefully considered when detailing reinforcement and formwork. For example, the ACI Guide states openings in the reinforcement should be provided to allow insertion of vibrators. Typically, 4" x 6" openings at 24 in. centers are suggested. This helps to minimize honeycombing and other imperfections, both on the surface and within a concrete member.
Both the CRSI and ACI vibrator recommendations offer specific responses to the CII constructibility concerns related to consolidation. But if we have a constructibility warning from CII, CRSI and ACI, why do we continually have a vibrator access issue?
The issue is mainly due to building Code requirements in Section 25.2.1 of ACI 318-14, which set the minimum clear spacing between parallel bars in a layer at the greatest of one inch, the reinforcing bar diameter, or 4/3 times the maximum aggregate size. The ACI 318 Commentary states that these limits were established to permit concrete to flow readily into spaces between bars and between bars and forms without honeycomb. For much reinforced concrete construction, bar sizes don’t exceed #8 and the nominal maximum aggregate size is three-quarters of an inch. Thus, a minimum clear bar spacing of one inch meets ACI 318 requirements. But a one-inch bar spacing doesn’t permit use of the common two- or three-inch diameter vibrator heads needed for adequate consolidation. Thus, recommendations in the CII, CRSI and ACI 309 documents are at odds with the minimum clear rebar spacing permitted by code requirements for the designer in ACI 318-14.
Ultimately, this is not about the needs of the designer or contractor, but those of the owner. The owner does not care about ACI 318, ACI 309, CRSI or CII recommendations. What the owner does care about is lowering the cost of construction without sacrificing quality. Concrete contractors can help to achieve this goal by providing input regarding constructibility during the early design stages. This is already being done by design-build firms, but there isn’t yet a good mechanism for accomplishing it through the design-bid-build process.