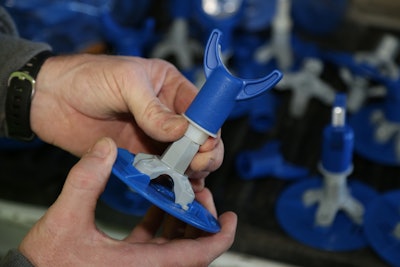
Maurin Construction began business in 2007 as a concrete subcontractor and found success working on public works projects. As the company’s work load grew, project specifications regarding Fl and Ff numbers were tightening up making it difficult for the contractor to meet the expectations of their clients.
When the company accepted a project at a local school district featuring a 12,000 square foot footprint, slab-on-grade and one elevated deck, approximately 7,000 square feet, meeting the required specifications was crucial. The slab-on-grade was to be six inches thick with two inches of sand, a vapor barrier and four inches of aggregate to be placed underneath the vapor barrier. The architect of the project demanded the floor meet the Ff 35 specification.
“We were looking for a better, more accurate way to meet the Ff numbers on flatwork projects,” General Superintendent, Craig Whitaker says. “Specifically, we were looking for a solution to be able to offer the most level, flattest floor we could build, without puncturing the vapor barrier that was placed between the slab and the ground.”
With a variety of products on the market, Whitaker says none of those products met their needs. “The reason we got involved with MAKO Products is specifically because the vapor barrier options the company offers,” he says. “The MAKO product allows us to use a non-penetrating system that is accurate, sturdy and adjustable—which is really nice.”
Whitaker is referring to MAKO's Base Plate and FinCap 4.5 Screed Support System. The system provides exact elevation control for concrete slabs. The stay-in-place screed supports are fully adjustable to accommodate sub-grade variances or deflection in elevated decks.
“The vapor barrier we were using is 15 mil thick, so it’s tough and hard to accidentally puncture, but it’s one of those things where you have to maintain the integrity of the vapor barrier,” Whitaker says. “That’s why the MAKO Base Plate and FinStands came in handy.”
He says the crew was able to set the Base Plate and FinStands on top of the vapor barrier. For added protection, the contractor brushed the bottom of each stand with a mastic from W.R. Meadows – PERMINATOR Underslab Vapor Barrier Retarder and glued down the base plates.
“This was not the recommended installation from the manufacturer,” Whitaker says, “but to me it was something that helped make the installation quicker and easier.”
MAKO’s Base Plate 4.5 used with the FinStand system was designed for uses with vapor barriers, sandy soil or any other type of substructure. The FinStand snaps and securely locks into the Base Plate. Setup continues by inserting a ½” rod between the bottom of the FinStand and the Base Plate. Adding a hex nut and washer for additional height gain and fine tuning the adjustments will achieve the exact elevation required on the job.
Set-up is complete by installing the non-metal FinCap which will work with a variety of mounting structures from 3/8” to 5/8”. The FinCaps support a nominal 1-1/2”– schedule 40 or higher screed pipe; or a 1-1/4″ ID or 2″ ID screed pipe may also be used.
Whitaker says the installation was quick and easy. “It was the first time we used this system completely. We would set each base plate down, install the threaded rods and set the height nut to the designated height. We then periodically checked to ensure we were maintaining the correct elevation using a string line and adjust the height as needed.”
Placing the concrete
With the screed support system in place, the pour was scheduled to occur the following day. “In preparation of the pour, we tend to map out our pouring and screeding strategy depending upon the type of obstacles that might be within the slab,” he says. “We like to get the bulk of the mud down in order not to stall the pour and in this case, the pour was a fairly wide open area.”
“One of the things I discovered was using the MAKO product caused our pour to go more efficiently. We spent the day prior trying to get things right and install the screed support system. It took us a few more hours than what I thought, but to me, it’s one of those things where all we have to worry about during the pour is picking up the pipe and moving it over to the next bay and making sure it is sitting in the cradle flush. During the pour, we had set up our TopCon laser system to make sure the finished floor stayed within the specifications.”
As the concrete was placed, the four man crew followed behind with Multi-Vibe GX35 vibra screeds and continued to strike off the concrete, all while maintaining the proper height and levelness of the floor.
“In our operation, we run the vibra screeds and then use a check rod to correct the highs and lows on the floor,” Whitaker says. "After approximately three to four hours, crews make one pass with our Whiteman ride-on trowel installed with float pans. We then use a bump cutter behind the float pans for cut and fill."
To finish the floor, crews install the ride-on trowel with float pans and make another pass in three different directions before switching out the float pans with combo blades to lay down the concrete. Finish blades were then installed to the ride-on trowel to finish the floor.
“Considering our main challenge was making sure not to puncture the vapor barrier and achieve the desired Ff numbers, I was really impressed with the MAKO product, even if everything about it was plastic. It’s a very sturdy product.”
Whitaker says he will be starting an elevated deck project soon and plans on using the product in the future. “It’s a lot easier and more efficient to use the Base Plates and the FinCaps on an elevated deck. We’ll still have the grade issues and this product will work just as well on these scenarios as it does on any slab-on-grade project.”