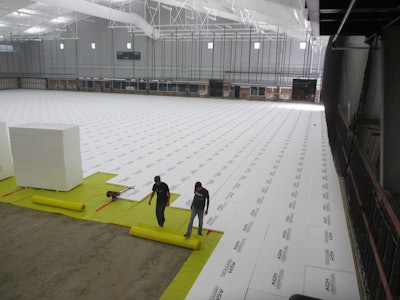
More than six years since the flood of 2008 destroyed the University of Iowa’s Voxman Music Building, the Hawkeye Marching Band is finally enjoying the benefits of a new indoor practice facility. Completed in the fall of 2014 as part of the Tennis and Recreation Complex, the band’s 82,000-square-foot indoor turf practice facility was constructed by General Contractor Russell under the State of Iowa’s first ever design-build contract. This new $15 million facility features a full-scale artificial turf practice field that additionally provides much-needed indoor athletic facilities for the University’s intramural and club sports, as well as some athletic department teams.
Iowa’s intense weather produces temperatures swings that range from below zero in the winter months to above 90 degrees during the summer. As a result, designers and builders need reliable, durable insulation strategies that perform well in both extremes. During the project development phase, the design-build team recognized that a key consideration for the University would be how to mitigate long-term heating and cooling costs for a building roughly the size of a football field for the life of the facility. For a space that size, in-floor radiant heating provided a lot of advantages over forced-air.
“Because this was a design-build project, there was a lot of opportunity to provide value analysis-based solutions during the pre-construction phase,” remarks Jim Seelman of MBA Incorporated (MBA), the subcontractor responsible for the indoor turf scope of work under Russell. MBA specializes in turf field construction and was familiar with a variety of architectural grade expanded polystyrene (EPS) insulation products that would support the radiant heating system. Since the design called for some 80,000 square feet of under-slab insulation, Seelman recommended ACH Foam Technologies’ Foam-Control Plus+ as an ideal solution.
In part, Seelman’s recommendation centered on the product’s favorable cost compared to XPS alternatives. Seelman estimates that selecting Foam-Control Plus+ saved the project more than $100,000 in material costs alone over the original specified product. In addition, the selected product had to meet the University’s performance criteria. Compressive strength was one key consideration since the design called for a six-inch layer of rock aggregate on top of the insulation, followed by the artificial turf. Placing the aggregate on top of the insulation required large trucks to drive onto the already-placed foam to dump the material, which was then finished in place. Other factors were the superior R-value of Foam Control Plus+; the ease with which the radiant heating piping could be laid into the insulation; and the product’s 50-year warranty. It is also the first EPS insulation on the market to come in uniform pre-scored pieces, increasing the ease and flexibility of installation.
“This product is extremely easy to install,” Seelman says. “We actually hired the local high school football team to help with the installation, and the kids were able to use the work as a team fundraising project.” Under MBA’s guidance, all 80,000 square feet of under-slab foam insulation were installed in a single 12-hour night’s work, tallying roughly 250 man hours of labor. “There were about 20 players from the team and those boys worked so hard, we actually were pressed to keep the materials coming to them fast enough. They laid out the foam, tapped the joints, and kept the overall grid really straight. They also ate about $300 of pizza, but it was a great experience for all of us.”
The evenness of the product was also crucial. Since the insulation was being installed below grade, any inconsistencies in level could contribute to an uneven foundation. MBA used a laser grading system to ensure a highly precise finish grade that remained flush within a quarter of an inch to support the aggregate and turf layers. Seelman also touted Foam Control Plus+’s uniformity, calling it “the most square” foam product on the market.
Though the design-build methodology is tried and true for builders and clients across the county, for the University of Iowa it was an unfamiliar process. That meant increased attention paid to every design and construction decision, including material selection and procurement. According to Seelman, the University wanted all long-lead items accounted for well before they were actually needed on site.
“When we made the switch from the original specified product to Foam Control Plus+, the University wanted actual photographic proof that we would have the required volume of materials on hand and ready for installation,” notes Seelman. “When you are talking about pre-purchasing 80,000 square feet of foam insulation, it’s not the kind of thing that can be brought to a congested construction site and simply stored until it’s ready to be installed.”
Working with Seelman and the local product distributor, Whitecap, ACH Foam Technologies processed the material order and then stored the foam until the foundation was ready. Knowing that many contractors find themselves in similar situations, ACH Foam Technologies often works with distributors to warehouse purchased materials and transport them to construction sites for a just-in-time delivery.
From quality and performance to cost and customer service, ACH Foam’s Foam-Control Plus+ insulation proved to be a win-win choice for the building owner, designers, and builders.