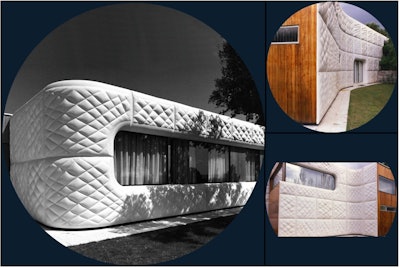
Throughout the 20th century, a number of innovators experimented with fabric as a flexible membrane for the support of fluid concrete, forming structural members. Significant among the early innovators were James H. de W. Waller (1884-1968) who in 1934 patented a fabric-formed system using hessian (burlap) fabric for numerous building components and in 1948, along with Kurt Billig, built corrugated concrete shell roof structures utilizing hessian fabric. In 1949, Felix Candela one of the most prolific of the shell builders and influenced by Waller began to experiment with fabric by utilizing burlap sacks stretched over wooden arches to form corrugated shell roofs. In the years following, Candela in turn influenced other visionaries including Pier Luigi Nervi (1891-1979) and Heinz Isler (1926-2009). Besides Nervi and Isler a few of the architects and engineers who used the forming materials at hand to create expressive forms out of concrete and masonry were Antoni Gaudi (1852-1926), Robert Maillart (1872-1940), Eladio Dieste (1917-2000) and Miguel Fisac (1913-2006).
Formwork applications
Alan Chandler in fabric formwork1 notes “…for Felix Candela and Christopher Alexander fabric acted as a permanent shutter (formwork)…”. Chandler speaks of the family of fabric construction that includes:
- Tensile structures
- Pneumatic structures
- Hydrostatic structures
- Shell structures derived from membrane form-finding
From this family of fabric construction what potentially practical applications exist? Fabric forming applications include:
- Walls
- Cast-in-place
- Precast
- Shotcrete thin-shell curtain wall systems
• Beam and floor system
- Trusses
• Columns
• Shells and Vaults
- Prefabrication of thin-shell funicular compression vaults
- Pneumatically fabric-formed thin-shell domes
- Molds for stay-in-place concrete formwork pans
- Pneumatically formed concrete impregnated fabric shells
• Foundations
- Continuous and spread footings
• Civil engineering works
- Revetments, underwater pile jackets
- Coastal and river structures
Figure 2. Quilt-like formwork pattern used for the Eiji Hoshino Residence.
It should also be recognized that wood and/or metal used for forming is not totally eliminated by using fabric but can be reduced to essential components thereby saving natural resources. So what is the current state-of-the-art? Following are several architectural examples.
State-of-the-art: Architectural formworks
One of the first architects to use a flexible formwork in an architectural application was the late Spanish architect Miguel Fisac with his 1970’s design of the Juan Zurita residence in Madrid, Spain, Figure 1. His use of rope and plastic sheeting to create these precast panels imparts a sense of “warmth and softness” to an otherwise cold and hard substance. Fisac used this method throughout the 1970’s to form the cladding of a number of structures.2
Another architect whose work has softened up concrete is Japanese architect Kenzo Unno. Working independently of Fisac he has developed several cast-in-place (CIP) fabric-formed wall systems since the mid-1990’s. The Kobe earthquake on January 17, 1995 provided the motivation for Unno to create residential designs that are intended to provide safe housing using simple methods of construction with as little construction waste as possible. Using standard wall ties and the wall’s reinforcement for support of the fabric membrane his quilt-point restraint method, for example, creates a pattern reminiscent of a quilt for the Eiji Hoshino Residence, Figure 2.
Figure 3: Susae Nakashima “Stone Renaissance” house.
Another practitioner that comes to mind is Sandy Lawton, a Vermont, USA design-builder. Lawton used geotextiles to form the columns, walls and floors for a nontraditional “treehouse” which was completed in 2007, Figure 4. See Sandy Lawton ARRODESIGN website: http://www.arrodesign.org/
Foundations
Industries are sometimes slow to embrace new technologies and industries utilizing fabric formworks are few. Since 1993 Richard Fearn, owner and founder of Fab-Form Industries, Ltd., has developed and marketed several fabric forming products including; Fastfoot for continuous and spread footings; Fastbag for spread footings and Fast-Tube for piers and columns. See Fab-Form Industries’ website: http://www.fab-form.com/.
Pneumatic formworks
Several methods of construction using inflated forms have been available since the early 1940’s but it was only recently that American Concrete Institute (ACI) Committee 334 introduced a standard guide for the construction of thin-shells using inflated forms.3
Figure 4: “Treehouse” for Chuck and Wendy Black.
Conclusions
By utilizing a flexible fabric formwork, such as a geotextile, several advantages have been noted:
- The possibility to form very complex shapes.
- Geotextile fabric is strong, lightweight, inexpensive and is reusable.
- Improved surface finish and durability―due to its filtering action.
- A more efficient and sustainable design is possible since material is placed only where it is needed―“form follows function”.
- Flexible fabric formwork increases freedom of design expression and can spark the imagination of architects and designers to think beyond the simple prismatic shape.
- The development of a fabric formwork system has the potential to significantly reduce man’s impact on the environment in terms of materials and energy usage.
Ed. Note: Part 2 was published in the April/May 2016 issue of Concrete Contractor.
Robert P. Schmitz, P.E. is a registered professional engineer in the State of Wisconsin, with more than thirty-five years experience in architecture and structural engineering. His research interest in fabric formwork comes as a result of work he completed for his Master’s degree and his desire to see this unique method of forming concrete brought into mainstream construction practice. He is a member of ASCE and ACI. He can be reached via e-mail at [email protected]
References:
Readers interested in additional information are encouraged to visit the following websites:
- Author’s research dedicated website: http://www.fabwiki.fabric-formedconcrete.com/
- The International Society of Fabric Forming (ISOFF): http://www.fabricforming.org/
1. Chandler, A. 2007. Concrete as equipment. In: Chandler, A. & Pedreschi, R. (eds.). fabric formwork London: RIBA. pp. 5-19.
2. Veenendaal, D. & West, M. & Block, P. 2011. History and overview of fabric formwork: using fabrics for concrete casting. Structural Concrete: Journal of the fib, 12 (3): pp. 164–177.
3. ACI Committee 334 2005. Construction of Concrete Shells Using Inflated Forms (ACI 334.3R-05). Farmington Hills, Michigan: American Concrete Institute.