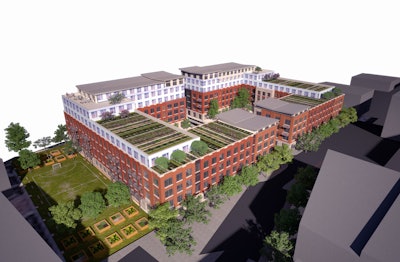
In the U.S. many community building codes for apartments and condominiums require parking garages to be constructed with concrete while the residential units above them can be built with wood. This is also the case in Kansas City, Missouri where Arnold Development, Kansas City, is building “The 122 Delaware Apartments,“ a 276 unit apartment complex. When the six story development is complete in 2017 it will have a tiered floor appearance with four floors of apartments in one area, five floors in another, and six floors in a third location—all over two floors of parking garage. The $50 million dollar center-of-city development is designed to attract both young and old to live in the heart of the city. The flat concrete roofs of the apartment structures will pitch to drains by using tapered insulation covered with a membrane roofing material. Featured on top of that will be unit paver walkways and gardens.
What is different about this project is that the entire construction is structurally reinforced cast-in-place concrete. The owner’s goal is to build a long life structure—a minimum 100 year service life with only regular maintenance—with high energy efficiency.
Concrete benefits for residential construction
Although structural concrete isn’t used too much for low-rise residential living units, there are many good reasons why it should be. Here are some of its advantages.
Long life. Given good engineering, concrete mix designs, and proper placement techniques, concrete structures can last a very long time. Owners are beginning to include specified service lives exceeding 100 years and longer in their construction documents.
Energy efficiency. Concrete is a very slow conductor of heat energy (or the lack of it) and for that reason it can store energy and release it slowly, providing very even temperatures while saving on heating and cooling costs. It eliminates air movement too, provided that openings are properly sealed. Insulation can easily be added on the inside, outside, or in the middle of walls.
Storm and fire resistance. Concrete is about the only building material that can resist maximum wind forces from tornadoes, straight-line winds, and hurricanes. It’s also the building material that should be used to build structures in high fire risk areas.
Sound transmission. For apartments and condominiums built with concrete walls and decks very little sound from surrounding units is transmitted. They are very quiet.
Resistant to mold, termites, and rodent intrusion. There isn’t anything organic in concrete to support mold, fungus, or bacteria growth. Termites can’t tunnel in it and rodents can’t chew holes in order to gain entrance.
- The wood industry promotes that it is green because not much energy is needed to harvest trees from a renewable crop. But it’s the long life of a structure and how much energy is needed to maintain it that really counts and this is where concrete performs well. Also, almost all concrete today replaces 20 percent or more of its portland cement with pozzolans such as fly ash and slag—products requiring no energy to make.
- The cost of a structure is usually compared to wood construction. For concrete cost is mostly related to forming systems and crew efficiency. Arnold Development thinks their project can match the cost of wood due to their choice of forming system, training for workers, and repetitive forming operations that increases efficiently.
Building the garage complex
James Rogers, the Project Superintendent for HarenLaughlin, Lenexa, Kansas, the general contractor for the project, says they used MEVA Imperial Formwork for the wall construction in the two floors of the parking structure at the recommendation of the concrete contractor. The walls on the first level are 12 inches thick while those for the second level are 16 inches thick in order to accommodate the walls for the residential units. Plywood panels were used to form the decks, with an Ellis 4x4 wood post system used for shoring. Western Forms supplied forms for the columns needed in the garage.
Building the residential units
The decision to use the Western Forms system for the living units was made by the developer. The aluminum wall forms include “ledger forms” which connect the inside wall forms to the aluminum deck forms, allowing contractors to form walls and decks (ceilings) in one operation and place concrete for both in one placement. It’s usual to place concrete for one entire floor level of a residence at one time. Ron Ward, president of Western Forms, Kansas City, Missouri, says each floor is divided into “L” shapes. An L is a cluster of approximately fifteen apartments facing a center courtyard. Workers can form all the units in one L at a time and cast them with concrete. The exterior walls and ceilings of each apartment are concrete; the interior walls for each unit are steel studs and drywall. Given the anticipated long life of the building the developer thought it best to provide for easy remodeling inside the units. Concrete beams can easily be included into the deck panel system and they occur when needed for longer spans, as are columns.
The decision was made to place insulation for the exterior walls in the center of the wall forms using the Thermomass system of ridged polystyrene foam panels positioned in the center of the wall form, held in position by special fiberglass ties. A finished wall includes a six inch reinforced concrete wythe on the inside, a six inch thick insulation panel in the center, and an exterior four inch thick reinforced concrete wythe, making up a total wall thickness of 16 inches—matching the second floor parking level walls that are also 16 inches thick. The decks are six inches thick.
The financial success of a project like this depends a lot on how efficient the construction of the apartment walls and floors are. Rogers says they sent a forming crew to a warehouse off-site to train how to achieve optimum cycle times with the Western Forms. They set up a 70 foot long mock-up wall that included columns, decks and beams. This was done twice, the second time being much faster. He thinks the repetitive nature of the formwork, performed dozens of times on this project, is what will enable their concrete work to meet or beat the cost of installing wood conventional wood frame construction.
The exterior walls for the apartment complex will be finished with thin-set brick and stone that will add little weight to the structure.
Concrete
122 Delaware will use approximately 25,000 cubic yards of concrete. Self-consolidating concrete (SCC) with a spread of about 24 inches is being used for all the walls in the structure to ensure good consolidation around rebar, produce fewer bug-holes, and to flow under window ledges as long as 10 feet. Rogers says they considered using SCC early on because they were concerned about tight wall profiles and the need for consolidation.
Specified concrete compressive strength for parking deck walls and apartment walls is 5000 psi, for columns is 8000 psi, and for all decks and floors is 5000 psi.
The developers wish
Arnold Development decided to use the “integrated project delivery” (IPD) process for managing construction. The developer and contractors included in the IPD also are integrating and using Lean Construction Practices to assist in planning and scheduling throughout the project. With this method of construction the owner makes decisions about the sub-contractors for the project—contractors they know and trust—and then hires the general contractor, giving them their list of preferred subs. The owner also decides on the type of structure they want so the decision to build concrete apartment units was their choice, one that stands in contrast to the more usual structural wood choice that local codes allow. Early budget planning put overall costs to be competitive with wood frame construction and hopefully that will turn out to be the case by the time the project is finished in late summer of 2017.
The developer plans to own the development so the reduced maintenance costs of the structure and energy savings are important to them.