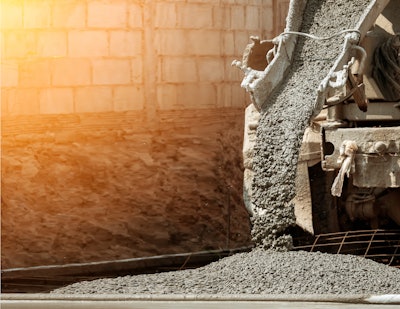
As a worldwide industrial concern with more than 50,000 employees, Heidelberg Materials is in a position to make a real difference in the global construction materials sector, both in terms of sheer cubic displacement and through its central role as the concrete industry evolves towards greater sustainability.
Heidelberg Materials produces aggregates, cement and concrete in Europe, North America, Asia, Australia and Africa. Across this operational portfolio, the company has well-defined organizational goals for sustainability. It has committed to generating 50% of revenue from sustainable products by 2030 and reducing CO2 emissions to 400 kilograms per metric ton of cement produced, down from about the half a ton industry goal for 2030.
The greening of concrete in particular has become an industry-wide effort, including environmental product declaration (EPD) requirements, led by NRMCA’s program and sustainability certifications for concrete plants and concrete professionals both. NRMCA is part of the Concrete Sustainability Council (CSC), of which Heidelberg Materials is a founding member. CSC has certified Heidelberg plants for sustainable operation, including several in the United States.
In parts of the world where the circular economy is progressing more rapidly, Heidelberg Materials has acquired companies that recycle concrete post-use, and in the United States is building internal capacity for recycling concrete rubble from demolition rather than sending that rubble to a landfill.
Another substantial area of accelerating progress being made in the United States however may be the adoption of internet of things (IoT) technology to reuse ready mix concrete leftover after a pour—concrete that otherwise would also wind up in the landfill.
Plants in Heidelberg Materials’ Southeast Region in the United States are rolling out the Command Alkon COMMANDassurance product, which harnesses the power of IoT to ensure ready mix meets quality and specification requirements when it is gets to the jobsite. COMMANDassurance leverages in-drum sensors and other sensors on the truck, along with a cloud-based application to provide visibility to the driver and the back office of what is going on with the mix. This extends beyond drum rotation speed and direction and other mechanical metrics to determine if the mix needs to be adjusted for an initial pour after its qualities change in transit, but also to ensure that leftover concrete from a pour still meets slump, temperature and volume requirements so it can be used on another project instead of being wasted.
CommandASSURANCE technology monitors and helps to manage properties ranging from slump, temperature, volume, water added and location/status of the truck.Command Alkon
If a truck has a water meter installed, COMMANDassurance can also measure and track how much water as added in transit. Other products in this smart concrete mixer category include the Verifi Solution from GCP Applied Technologies, which in turn leverages the AT&T Internet of Things platform-as-a-service (PaaS) solution, Colombia-based Stratos Group’s eTrace.
While the industry is focused on environmental improvement, materials companies should also consider putting less waste in the landfill and atmosphere can mean cost savings and process improvements that are measurable in dollars and cents. While focused on reducing waste in current operations rather than the more systemic and structural changes the industry is going through, the COMMANDassurance technology has helped Heidelberg Materials southeast region save a quarter of a million dollars in 10 months of having the solution in place in a portion of the region.
This elimination of waste by enabling re-use is a simple and hard metric for Heidelberg Materials to point to. But a variety of other metrics can improve thanks to clear, real-time information on when the load is fully mixed, when it is ready for discharge, and when water was added to the mix and how much.
A slump indicator on the truck-mounted system displays slump and temperature, enabling operators or even the customer to verify the concrete meets its specification. The unit also displays concrete volume, which will help operators and customers, as the volume drops during a pour, confirm they are getting the volume of materials ordered. Data is also packaged into reports so quality management teams can analyze performance to drive operational improvement or document concrete quality for regulators and project stakeholders.
COMMANDassurance Implementation
Heidelberg Materials has had a beachhead in the United States since 1977 when it purchased the Lehigh Cement Co., which, with its single mill in Pennsylvania, and been producing Portland cement since 1897. Heidelberg Materials in 2007 absorbed Hanson PLC to create Lehigh-Hanson, a multi-national provider of cement, aggregates, ready mixed concrete and other construction materials. The US company’s name changed to Heidelberg Materials in January of 2023.
“We are running COMMANDassurance in Alabama and Georgia, across a ready-mix operation that includes 23 concrete batch plants and running around 120 trucks,” Heidelberg Materials Quality Control/Technical Services Manager for SE Region Ready Mix Scott Kelley said. “These plants are producing about 750,000 yards of concrete annually.”
The southeast region provides material to a broad mix of commercial and residential customers, with an almost even split in Georgia and a majority of material going to nonresidential in Alabama.
“We see everything from a 40-yard residential pour to a 30,000-yard commercial job. We’ve done pour sizes over 4,200 yards, but that is not the norm of course. We do a lot of bridges and some infrastructure, but southern states are not typically heavy concrete usage states for interstates and highways so most of our infrastructure is bridges.”
Between this mix of projects, Kelley and his team see high-specification jobs ranging from 2,500 to 8,000 PSI. Having technology that helps them tightly control not just traditional quality measures, but specific qualities of concrete as it arrives on the construction site helps them nail these specifications reliably and confirm on-spec delivery to customers and project owners.
For Kelley’s team, COMMANDassurance also closes the communication gap with project stakeholders by sending notifications when a load is leaving the yard, when it is ready for discharge, how much water was added, and other data points.
This data eases real-time communication and underpins the work of a concrete producer’s quality team as they evaluate and optimize mix designs, mitigating against the need to overdesign the mix that previously may have been prudent lacking good data. This saves material costs because with more data it is possible to opt for a leaner mix design since the changes in transit can be planned around or even mitigated in transit. This enhanced visibility into the qualities and condition of concrete in the drum also prevents costly waste and rework from rip-and-replace.
A solar-powered in-drum probe collects data on mix condition in real-time.Command Alkon
Concrete IOT Evolution
Kelley remembers the first time he heard about the idea of rigging a drum with sensors to monitor its properties in transit.
“I had a friend working at Command Alkon at the time and he said he wanted to have lunch with me,” Kelley said. “He had a big steel rod and said he wanted to put this in a drum and measure slump. I told him that if you can do this and do it accurately, it will change the face of the industry. You are starting to see these kinds of technologies coming out. We have totally changed the way we deliver concrete right now. We can test at the plant and at the job, but a lot happens in transit. Now, we can see from the time it enters that drum.”
Capturing IoT data from inside the drum and even managing those conditions actively in transit yields a huge data set, and Kelley relies on this data set to support multiple other functions. One of these functions is to avoid disputes through thorough documentation.
“Knowledge is power,” Kelley said. “When you are in the quality control role, you are put into some situations where you have to defend yourself by digging into the forensic side of concrete. He who has the most data usually wins. The temperatures in particular are key to the ability to reuse concrete. We have for a long time been able to track load times and batch times. But now being able to monitor slump, moisture, temperature, materials and volumes, these are the key components you were not able to track together and now you can.”
A precise set of data on what is happening in the drum is crucial to supporting decisions about whether or not to re-use a partial batch.
“We can then add that to or send it to a different order, or load on top of an order depending on parameters the quality control team and I set up,” Kelley said. “That has saved us a pretty good bit of money in terms of being able to reuse that concrete instead of haul to landfill and get rid of it. Our broader focus is on sustainability, but this is one of the bigger areas of hard ROI for this technology. In our Alabama business, our ability to use returned concrete was zero—we did not do it. You have to have a way to measure it to meet ASTM guidelines for reuse.”
Under ASTM C1798 guideline, a materials provider can re-use concrete up to eight hours after its original mixing time. The temperature of the concrete to be re-used must not exceed 100° F and meet other project specifications.
Technology for Concrete Quality Management
Apart from supporting the ability to re-use leftover concrete in a batch, the added confidence in the properties of the concrete at the time of pour enable designing mixes around these new, tighter, tolerances.
“We have been able to optimize the mix design because of this technology,” Kelley said. “We can tighten standard deviations. Some of our mix designs change over time, but this technology has shown me that, for instance, we were a little water thirsty on some of our mix designs. We are now able to optimize designs that we already thought were okay.”
Technology for in-transit concrete management has won Kelley’s trust, but as its reliability becomes more widely understood, it may have far-reaching implications for regulatory enforcement and other processes outside of the materials provider organization.
In-drum monitoring could soon replace traditional concrete slump testing.©ME Image – stock.adobe.com
“I have enough confidence in this slump and temperature and other data to take that over what a third party does,” Kelley said. “The standard for slump, in my opinion, is less reliable because you can follow the standard and have two inches difference in reading. I have found is this technology is very consistent. Even if I was running a slump test, I would take the consistency reading based on pressure. You can calibrate that number to a slump number and measurement, and I would take it over 100 tests. In that test, the concrete may pull faster or slower, but digital gives you a true reading.”
Even an integrated, engineered solution like COMMANDassurance is not the end-all, according to Kelley.
“The sophistication of this technology will continue to advance,” Kelley said. “Air content is a constant battle in the ready-mix world, and our next thing may be trying to chase air content.”