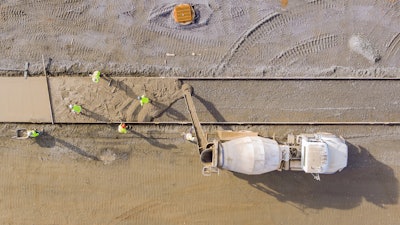
Concrete can be unpredictable and change from good to bad at the drop of a hat. Concrete is perishable, therefore, the way that you treat the product before use is crucial to its future quality.
Testing the quality of a load of concrete has traditionally been done manually. This method of manual testing takes time and can be tedious. If the concrete doesn’t meet expectations or has a different finish from the previously poured batch, then crews are tasked with rip-and-replace—a very pricey process. If a load received onsite isn’t in spec, the truck could be sent away and the concrete will have been wasted.
Mistakes are costly in the concrete industry. What can you do to avoid undue expenses? The future of concrete is moving towards mobile quality control technology.
What is Mobile Quality Control?
As the world advances toward digitization, the construction industry is starting to incorporate more opportunities in technology. Mobile quality control (QC) technology can make the concrete testing process quicker and improve accuracy.
How it Works
Mobile quality control for concrete functions in a relatively simple way. Sensors are placed either at the plant, on the drum, or both. These sensors monitor everything from temperature to slump to air. There are technologies that can work together such as BCMI’s Material Now and CiDRA’s SMARThatch. With this technology in the palm of their hands, contractors and workers at concrete plants can get real-time data on the state of a load of cement. Having information at your disposal at any moment can ensure that loads aren’t wasted and removal is not necessary.
CiDRA SMARThatch shown on a ready mix truck onsite at a project.Irving Materials, Inc.
The Benefits of Mobile QC
There are a variety of benefits when it comes to mobile quality control in concrete.
1. Time Savings
Manual concrete testing can be time-consuming, and the wasted time can lead to differing results between test time and pour. Giving you real-time access to data, mobile QC makes it much quicker to retrieve information.
It can take around 10-15 minutes to test the concrete’s slump and air. While testing with mobile QC can cause drivers to slow down a little due to letting the drum sit for a couple of minutes, that’s all it takes to test the batch.
Slowing the drivers down a bit could result in “better driver behavior, which will then create a more consistent concrete from their end too,” says Heather Brown, vice president of quality control at Irving Materials, Inc (IMI).
2. Cost Savings
Companies using mobile QC technology can have fewer errors in their concrete mixes which leads to far less load rejection. When trucks are sent out and then sent right back due to not being up to standard, both the company and the contractor suffer. Using quality control technology makes the process of sending and receiving trucks much smoother.
Brown explains that “if you know your concrete properties, in transit and on the job by a sensor, then you're not waiting, you're not slowing the job down, and time is money.”
Mike Baldoni, director of quality control at IMI, details that if a company delivers “in spec concrete, we can see it immediately right after we batched it. That just helps the overall quality process of a project in general.” Baldoni applied this to the claim that this technology provides education to crew members by exposing them to the data. When they understand that data, they can better discern what happens with their concrete, and this instigates finding solutions to the problems.
If a crew builds a structure out of concrete and suddenly realizes that the concrete they used was bad, the cost repercussions can be extreme. Craig Yeack, president and co-founder of BCMI, says that this kind of mistake is “hugely expensive. It can often bankrupt the concrete finishers and the concrete producers and, of course, it's a legal mess.”
3. Environmental Protection
The construction industry can be very dangerous, and safety tends to be the industry’s number one concern, but according to Yeack, reducing their footprint stands right there with it. Yeack states that the industry is “experimenting with all sorts of new types of concrete—concrete replacement, geopolymer concrete…to try to reduce that carbon footprint.”
Brown and Baldoni agreed that more environmental benefits have potential if contractors and owners get on board. Brown says that architects “want to slow things down so that [they] can put in more environmental products. But that would mean that you might not be able to load that floor, for two weeks versus six days. So, it's gonna push construction schedules out, and nobody is getting on board with that.”
In the future, hopefully, contractors and owners will come together with architects and concrete companies to slow down and allow for a more positive environmental impact.
Being able to digitally check on a load creates a lot less waste compared to the manual testing necessary for each load.
A worker is watching the BCMI Material Now app at the concrete plant.Irving Materials, Inc.
4. Safety Benefits
Safety in testing concrete isn’t necessarily something that people consider. But there are a few things that have the potential to be dangerous in the process of testing and transporting concrete.
Andrew Davis, product manager at CiDRA, mentions the added “safety benefit that drivers don't have to climb up and check the load of the truck on a ladder. The QC guy doesn't have to move around tens or hundreds of pounds of concrete by hand. They don't have to go dump the samples and dispose of them.”
Another bonus benefit of having technology monitor the specifications of concrete is the potential to see drum revolution speed. This feature, intended to help understand the quality of the load, can also aid in the safety of many. If a driver goes speeding along and their drum is spinning really fast, they’re at risk of crashing. The faster the drum turns, the higher the chance that the truck rolls over. Drivers will likely be more cautious driving knowing everyone on the job site can see how quickly the drum revolves. Therefore, leading to a safer environment.
5. Less Over-design and Rip-and-replace
In the concrete world, over-design and rip-and-replace are nightmare-worthy. These processes result in lots of time and money lost. Sometimes engineers want “a built-in amount of over-design so that we know it will not fall below the minimum strength,” says Brown.
This desire to ensure strength through overdesign can be resolved by trusting the quality and strength of the concrete mix. By being able to test each load of concrete and have access to all the sensor data, engineers can have more confidence in the concrete provided and therefore reduce over-design.
Rip-and-replace can be avoided by simply having information on a batch of concrete before pouring. When referring to rip-and-replace, Davis says that people commonly use the factor of three which means that “If you have to remove material that you've placed, it costs three times as much as it did to put it down the first time.”
Using QC data gives the contractor and the engineer the information they need to decide if the load fits the standard before they use it.
6. Claims Disputes
Using bad concrete can result in catastrophe depending on the structure being built. When something goes wrong, everyone looks for who to blame. With the data provided by mobile QC technology, suppliers, contractors, and concrete finishers can defend themselves and protect themselves from liability. Easy-to-access data helps even further should there be accusations. The CiDRA SMARThatch close up on the side of a concrete mixing truck.CiDRA Concrete
Mobile QC Can Help
Having mobile quality control technology at your fingertips enables a more informed and simplistic way of dealing with concrete— helping make placing concrete more productive, cost-efficient, and reducing guesswork.
Yeack says, “I think the big thing is harnessing the available digital tools to improve their business, to not just save money here and there, but to actively look for leaks of profit. Actively look and plug these problems like holes in a boat.”
If you own a concrete plant, contract for concrete builds, or have anything to do with concrete at all, you should know that useful technology is available. The big thing that Baldoni and Brown wanted to push was getting the word out to owners about this technology.
Baldoni says, “the owner is usually responsible for hiring the third party for a project.” However, owners are subject to a disconnect between what happens on-site and what technological advancements are occurring. Owners must understand the changes in the industry to make educated decisions on who to hire. This will hopefully encourage more environmentally friendly decisions from contractors and data-driven actions.