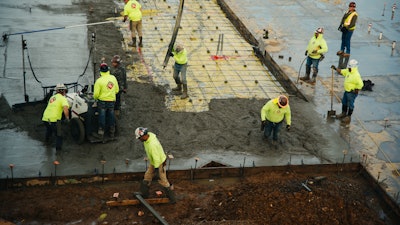
The drive to reduce the carbon footprint of the cement production and concrete construction industries continues. According to the statistics and facts from Statista.com published on March 2025 these industries would be the world's fourth-biggest emitter of greenhouse gases.
Yet, works and efforts continue and every foot and every slab provides an opportunity for some sustainable decisions. For example, projects are opting to spec for more green cement options, such as opting to bring in 18 metric tons of a green and ordinary cement mix for the construction of a new building in Northern California. The use of which should result in a reduction of nearly 13 tons of embodied CO2 for the project.
Simpson University (Redding, California) have begun the construction process of a new business, technology, and engineering building to be the home to the Maurice & Marianna Johannessen Veteran Success Center, STEM program facilities, as well as new engineering and technology labs. Green cement manufacturer, Fortera, provided 17 metric tons of their low-carbon "green" cement product known as ReAct to the project. Made from industrial CO2 emissions, concrete producers will mix the cement with ordinary cement at a 10% blend for the construction of the slab and footings.
Placing the footings.Fortera
According to Fortera, the use of ReAct should result in the reduction of nearly 13 tons of embodied CO2. The product was produced at the Redding ReCarb Plant - the company's commercial facility that directly captures carbon emissions from cement production to make ready-to-use green cement. With concrete contractor SK Construction on the front lines, Shasta Redi-Mix supplied the concrete for the project, and rebar placement was subcontracted out to Sacramento Rebar. Concrete pumping was provided through American Concrete Pumping via boom pump.
The job required 18 metric tons of ReAct mixed with ordinary cement for 650 cubic yards of concrete, enough to fill 65 concrete mixers. Shasta Redi Mix is not directly connected to Fortera.
Construction broke ground on the project in May 2024 and has raised $8M for its construction, with $1 million needed to complete the final phase. Construction is expected to be completed in time for the 2026 fall semester.
Building on Relationships
Concrete contractor SK Construction specializes in structural work providing services in commercial and residential foundations, flatwork, as well as decorative. Their brother company, Ward Concrete, specializes in the curb and gutter, sidewalk side of the business.
"My father [Steve] started the company," says Brian Kamisky, president of SK Construction. "I worked for him all through college - even when I was away at school." Brian started taking over the company in 2011 after graduating from Chico State with a degree in marketing with an emphasis in finance.
"My dad didn't have an opportunity to go to college...so his dream for my brother and I was that he wanted us to go to college and graduate," says Kamisky. He and his brother worked as much as they could in the business while in school - covering their debt. He graduated with a degree and got back into concrete the next day.
It's often said that relationships is key in the concrete industry. SK Construction are a prime example. Kamisky says that about 70 percent of their work is from the same 5 or 6 people that they've been doing business with for the last 35 plus years. In fact, half of their jobs they don't even bid. "We have clients that we just do all their work, no questions asked. 'Here's a set of plans, here's when we're going to have the dirt work ready...let us know when you're done,'" he says.
You can't find a more solid foundation than that.
Fortera has had a plant in Redding for five years. Focused on sustainability and green efforts, they are honored to have the opportunity to be a part of the construction so close to home. As quoted in the official announcement, "We're committed to making a positive impact in our own community and proud to contribute to the foundation—both figuratively and literally—of education, veteran success, and sustainable infrastructure," says Ryan Gilliam, CEO of Fortera.
Working In The Mix
Despite the low-carbon qualities, the concrete specs were fairly typical:
- Maximum w/c ratio of .50
- Minimum compressive strength of 3,000 psi
- The concrete mix was a 5.75 sack mix with 10% replacement of the Fortera ReAct material
Fortera
Contractors used a Somero S-485 to screed the concrete. With the amount of plumbing, deepened footings, anchor bolts, and other limiting factors, its maneuverability made it key to productivity. The S-485 also does not include auger - just the plow - which allowed contractors pull excess straight back and to work around obstacles without the auger ejecting concrete into already screeded areas.Fortera
While the mix was green, nothing out of the ordinary was required for rebar. All reinforcement steel was American-made, grade 60, standard bent bars. No epoxy coating was needed even though they knew they were using a new mix design.
Shawn Shasta, manager of Shasta Redi-Mix, explains that the compressive strengths of the concrete with the Fortera ReAct addition averaged 5% higher than standard portland cement mix which would allow them to further reduce the cement content in the concrete, therefore reducing the embodied CO2 per cubic yard of concrete ever further. "Anything we can do to reduce the embodied CO2 in our concrete is a move in the right direction," says Steele.
On using the "green" concrete mix, Kamisky was excited, using it an opportunity to build a competitive advantage in the area. Where it would be more understandable for a project funded by the deep pockets of an Apple or a Google, it's a rarity to have something of this size in the area. "It's nice to see that there are some jobs here where people are willing to try some things while benefiting the environment," he says.
"The construction industry is definitely moving in the direction of a low carbon concrete mix and is much more prevalent in the upcoming project specifications," says Steele. He anticipates the use of a low-carbon concrete in all upcoming projects.
Due to limited accessibility and size of the project, ready-mix trucks were not allowed close enough to tailgate the placement.Fortera
The placement and the finish were very similar to a standard mix of straight portland cement. Both Kamisky and Steele say there were not any noticeable differences.
It was comparative enough, in fact, that Kamisky didn't tell the concrete finishers about the "green" quality in placing the footing pour. At the end of the day, he asked the guys that placed the footers what they thought about the mix - they had no idea it was any different in the footing placement; it acted identical to your normal footing concrete without the admixture.
Everything met strength in break results. In fact, all breaks were above what they needed to be.
In the placement and finish of the slab, on the other hand, is where things get a little more critical. No one will ever see the footings, but the slab is where contractors are selling the finished product. SK Construction had a few extra guys out to make sure it didn't flash off or harden faster than anticipated. They compared it to working with pouring with a fly ash mix design.
"It's pretty standard to replace 15-20 percent of cementitious material with fly ash or blast furnace slag...this just replicated those," says Kamisky. "It didn't finish like a pure cement mix design would, but it finished very, very similar to a fly ash mix."
They even noticed similarities in cutting the control joints. Normally, they prefer to not to use fly ash or additives for slab-on-grade concrete - the edge has a tendency to fracture off when cutting the joints and not hold a tight saw cut line. Kamisky explains: "Because the fly ash has a tendency to have a greater 56 day overall strength, it has a lower 7 and 28 day strength. That initial set period to get the concrete tight enough to saw cut it without fracturing the edges usually takes a little bit longer with fly ash. When we're pouring an 80,000-sq.-ft. finished floor warehouse, we will pull all the fly ash out of the mix designs to get it to tighten up faster so our saw cuts look better. "
Luckily, they didn't have this issue - Kamisky says that it saw cut just like normal concrete.
SK Construction had existing buildings on three sides of the project. Contractors were given one fact to access work.Fortera
ReAct green cement is a unique form of calcium carbonate created from mineralized industrial CO2 to match the strength and durability of ordinary cement. It meets ASTM C150 and ASTM C595 specifications. ReAct can be used alone or mixed with ordinary cement, reducing the carbon footprint of construction projects while maintaining strength and enhancing workability.
Simpson University is the only private university between Sacramento and Eugene, Oregon. The new building will provide crucial resources to veterans as they transition from military service to student and civilian life. The VSC will offer admissions and enrollment assistance to prospective students, veteran-specific benefit navigation, supportive veteran community spaces, study resources, and mentoring. According the release, approximately 10% of Simpson students are veterans or their dependents. The new space and expanded programming will allow the university to increase the number of veterans served - it expects to double its annual reach in the next 5-10 years.
For the university, the building and the center represents more than additional square footage, but the alignment of environmental stewardship and impact into the community. "By providing low-carbon cement for our project, Fortera is supporting both STEM workforce development and expanded services for our veteran community...This project’s environmental and educational benefits will create a lasting positive impact in our region," says Ken White, Dean of Advancement at Simpson University.
A rendering of what will be the new Business Technology and Engineering Building at Simpson University.Fortera