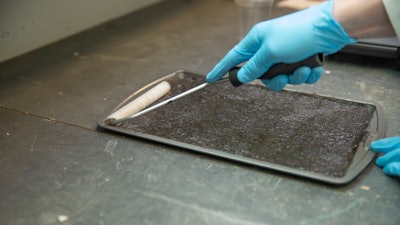
According to the American Road & Transportation Builders Association (ARTBA), 1 in 3 bridges in the U.S. need repair or replacement. Of the 2022 state data, Kentucky ranks 19th in structurally deficient bridges of inventory. As it’s the second-most used material on the planet, the work will require a substantial amount of concrete. ARTBA's data ranks West Virginia, Iowa, and South Dakota as the top three in percentage of structurally deficient bridges, respectively.
Sometimes, it takes a fresh set of eyes and the creative mind of a young generation to take look at past ideas and rework them in exciting new ways for modern construction and repair. The team of undergraduate, graduate, and even a couple of high school students at the University of Kentucky have been cleverly researching ideas in the civil engineering and structures for years with the guidance of Professor Issam E. Harik and Abheetha Peiris, a researcher at the Kentucky Transportation Center
Harik is a Raymond-Blythe Professor of Civil Engineering and Structures Program Manager within the Kentucky Transportation Center at the University of Kentucky. The department covers all major components of civil engineering from transportation, environmental, hydraulics, hydrology, structures, materials, geotechnical, and construction. Much of his research has been in concrete structures repair. He and Peiris have been at the helm of a group of students since 1994 researching the use of fiber reinforced polymer (FRP) composites.
University of Kentucky
“Sustainability has recently become a ‘buzzword’ seen on many products and websites,” he says in an April 2023 press release. “But, for engineers, it has been and remains integral to optimizing material, energy and time, while minimizing cost and environmental impact.”
“Not only concrete is changing quite a bit but also some of the materials for repair or new constructions,” says Harik.
For example, student teams since late 1990s have already developed carbon fiber rod panels and fabrics that have been deployed to help repair more than 40 bridges in Kentucky. He says that there had been at least two occasions where a bridge was saved using the product. Products developed by the student group all fall under the moniker CatStrong—a reference to the Wildcat legacy of the university.
The carbon fiber fabric product utilizes a high-grade, high strength “aerospace grade” material. In fact, the same fibers that produce their products are used for high-end aircrafts like the Boeing 787 and jet fighters able to product a 700,000 lb./in2 capacity. Back in 2019, the student team then conducted an experimental case in that they enlarged a bridge pier utilizing a concrete form made of hemp. “In these cases,” explains Harik, “we don’t need the 700,000 lb./in2 strength that the carbon fiber can provide— much less strength would be more than adequate for these applications.
According to the university’s news, the team repaired one of the piles on the KY 32 bridge using their hemp fabric. It cites the natural material’s biodegradable quality and a small carbon footprint—but had a low strength.
While he advises the undergraduate student group with guidelines and assists with purchasing material, the students conduct all the research. They take lessons learned from each project towards the next, always aiming at upgrading and extending the life of bridges and buildings.
They’ve now turned their sights onto utilizing human hair as their next material to create a natural, easily sourced, environmentally concrete form. Yet, it’s early in their research. The project is divided into three stages; as of spring 2023, they’ve finished stage one.
It sounds strange, but there are undeniable benefits.
University of Kentucky
“The project involves analyzing, designing and deploying concrete construction forms fabricated with human hair (fiber reinforcement),” explains Peiris.
The students wanted the entire product to be either recyclable or so easily disposed of that it would not pollute the environment. Harik explains that they spent the year developing a bonding agent or resin made of commercially available “off the shelf” products. He says, “One bonding agent that students started the project on was flour, water, and lemon juice. It was successful for producing samples, but it was not geared towards producing large forms to pour concrete.” They then tried alternative products and eventually were able to produce a form from hair mixed with that natural product. A local salon was more than happy to supply discarded cuttings.
The objective was to create something reproduceable, anywhere—but something not of animal hair or plant fibers, something available even in remotest areas to produce a concrete form. They started with a two-part epoxy as a resin binder, but it was synthetic and didn’t fully meet their sustainability requirements. University of Kentucky
To create their sheet, Harik explains that the students had to find the ideal temperature to heat the mixture of binder and human hair to have the components come together while keeping a level of flexibility.
As a sheet of fabric, students found that the CatStrong product could easily produce any shape, wrap as many times as needed to increase strength, and resized on site. “You don’t have to precut beforehand,” explains Harik. “If the design plans call for an additional six inches of concrete, but you get to the site and decide ‘no, I need 12 inches’ [contractors] would be able to add extra layers.” He explains that the thinnest it can go would be same as the thickness of the human hair.
They’re at “proof of concept” stage to prove the idea and confirm a natural binder via creating pour cylinder molds for tests. Depending on the binder, the used cylinder mold could then be tossed for compost – saving that waste from a landfill. Students are conducting hundreds of tests, but their latest included borax with lemon juice. Remember, that one of their objectives is to have every material involved to be readily available.
Phase two will be further developing the fabric and laboratory testing. They’re hoping to have a field application in three years.