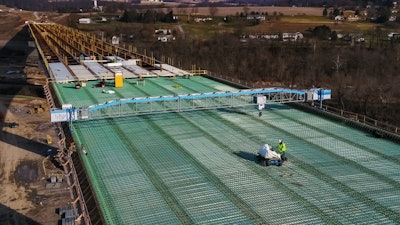
Located in Beaver County, PA, the Koppel Bridge was a historic, 1,200-ft. structure dating back to 1914, where it was initially a privately owned toll bridge. The state of Pennsylvania acquired the bridge in 1944 and it subsequently went through various repairs throughout the decades before the Pennsylvania Department of Transportation (PennDOT) finally determined its age and condition warranted replacement.
The $27.58 million Koppel Bridge replacement project called for two 12-ft. travel lanes and 8-ft. shoulders. The deck would consist of 1 million lbs. of rebar and 6,000 cu. yds. of concrete. The structural steel supporting the deck would weigh approximately 4.3 million lbs.
The project required closure of the bridge to all traffic over a 72-day period from mid-August 2019 through late October. Brayman Construction Corporation (BCC), a heavy civil and geotechnical contractor headquartered in Saxonburg, PA, was brought on as the prime contractor. Known for being an early technology adopter, the contractor took a unique approach to rebar tying on this project.
A Robotic Solution
Situated in the Pittsburgh area, a global hub for artificial intelligence and robotics, BCC is no stranger to advanced technology. In fact, company chairman and CEO, Stephen Muck, is an innovator himself, partnering with Jeremy Searock, a former technical program manager at Carnegie Mellon University's National Robotics Engineering Center, to form Advanced Construction Robotics (ACR). The company combines robotics and artificial intelligence (AI) to develop autonomous products for the construction industry, including the TyBot autonomous rebar tying robot.
The TyBot rebar tying robot can tie up to 1,000 intersections an hour using autonomous navigation of its working area.Advanced Construction Robotics
With the extensive rebar tying required, the Koppel Bridge project was an ideal opportunity to put TyBot to the test. BCC meticulously recorded production data for the deck reinforcing steel installation of the project so that the case study could provide meaningful results.
Autonomous Tying Generates Substantial Savings
BCC self-performed the rebar installation on two of the four spans before bringing TyBot, LLC in as a subcontractor to complete the bulk tie on the remaining two spans. BCC was projecting a 20% savings in personnel hours for bulk tying, but the data showed the company saved an additional 14% on top of this, bringing its total savings to 34%.
TyBot, LLC performed the bulk tie portion of the Koppel Bridge deck reinforcing steel installation for two out of the four spans of the bridge.Advanced Construction Robotics
In addition, use of the TyBot prompted the operations team to perform more pre-planning of the deck rebar work in order to minimize the time the robot was waiting on placed rebar to tie. Such planning is typically done in the field, with the crew often reacting to the daily changes and challenges that are frequent on such projects. With TyBot, the manual labor crew was focused on making sure “the robot didn’t catch up to them.” This created a sense of competition between the robot and crew, pushing the work along faster.
The combined result was a 34% savings in both personnel hours and in the duration of the work on the project. In addition, the Koppel Bridge replacement showcased how using TyBot to augment rather than replace a rebar crew can help accelerate projects, meet tough schedule constraints and best utilize worker skills.