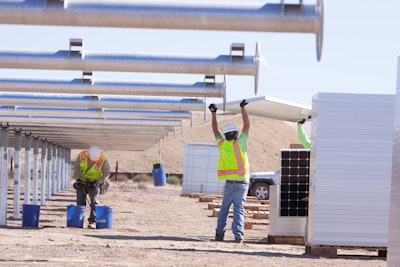
Robots for construction and automated construction equipment are prominent at CONEXPO in Las Vegas March 14-18, with robots for repetitive use cases dominating the field.
The sector has moved well beyond 3D paving and earthwork applications with GNSS-driven elevation control from the likes of Trimble, Topcon and Leica that have been launched in the early 2000s. In these earthmoving and roadbuilding use cases, equipment is progressing from automated control of the level of a blade or compactor to automated steering. Software that supports the automated equipment will often help interlace tasks of the different pieces of equipment on a site—a paver and a compactor, for instance, to create an automated process. The technology has progressed to the point where the equipment can, with minimal human intervention, execute against a road cross section or site plan.
These repetitive use cases in greenfield construction or linear asset construction are maturing, but various emerging and established robotics companies are addressing myriad other tasks that are ripe for automation. From masonry robots to robots that place and tie rebar for infrastructure projects to robots that print schematics on the floor of a project, new use cases for robotics are coming to market, and many are being shown at CONEXPO. What is very rare though about from 3D earthmoving and paving which are seeing multiple new entrants, many other construction robotics use cases are firsts in the market. Another exception is field printer robots used to mark the project floor with the plan and even instructions to trades, where a new entrant from HP will be released to market this year to compete with incumbent Dusty Robotics.
Solar Construction Technology
But the robots coming broadly to market, from those that enable remote operation to those that aim to operate autonomously, perform better in repetitive environments, as opposed to that would require a robot to deal with ad hocratic events as they unfold. These environments include solar construction, where Built Robotics has focused their efforts with their robotic exoskeletons for excavators.
According to the International Energy Agency (IEA) solar generation increased by 179 TWh (up 22%) in 2021 to more than 1,000 TWh.
“Solar PV is becoming the lowest-cost option for new electricity generation in most of the world, which is expected to propel investment in the coming years,” IEA reports. “However, average annual generation growth of 25% in the period 2022-2030 is needed to follow the Net Zero Emissions by 2050 Scenario. This corresponds to a more than threefold increase in annual capacity deployment until 2030.”
This macroeconomic trend makes solar field construction a desirable target for robotics, so it is not surprising that today at CONEXPO, Built Robotics announced another robot to address another task in solar field construction—the RPD35 robotic pile driver. The robotic system attaches to a mid-sized excavator—the version at the show was built on a Caterpillar 335.
“The piling process is very difficult, it is labor intensive, unsafe, and it could be a good component for automation,” Built Robotics Director of Communications Erol Ahmet told IRONPROS in a briefing the week before CONEXPO. “What happens without robotics is that a survey team comes out to mark the locations, and then a pile distribution team manually places a single pile at each spot. Driving the piles and getting them into the ground is its own step. And then there is an inspection process to ensure the pile is plumb and at the correct depth. We can take all those four steps and put them on one machine. You just upload the site plan—the poles are housed on the machine itself.”
The machine can carry 200 piles, driving them autonomously with a custom-designed hammer that impacts the pile 500 times per minute at 4,000 pounds of force per foot.
By using GPS, the RP35 can place the piles to the requisite degree of accuracy, which is essential because failing this the load weight of the solar panels could be affected. Some of the functionality of the RP35 is underpinned by a robotic operating system that came with the company’s January 2023 purchase of Roin Technologies.
“Our ultimate goal is to automate every step of the utility solar process,” Ahmet said. “We handle the trenching for the AC/DC cables, now pile driving, and we are also looking at a machine to automate solar module installation.”
Robots Face Off
This direction puts Built Technologies on a collision course with Sarcos Techology, which earlier in March of 2023 went through final validation on a robot for solar module placement. A broader, multi-industry robotics company, Sarcos bases their technology for solar panels on a suction-based lifting arm used in solar panel fabrication. Sarcos’s Outdoor Autonomous Manipulation of Photovoltaic Panels (O-AMPP) project is a collaboration with Mortenson, JLG Industries, Array Technologies at a Mortenson project site, which validated the Sarcos robotic solar field construction solution.
The publically-traded Sarcos may have broader resources to draw from than the, including a commercial team and team focused on defense. Sarcos relies on standard vehicles as base to provide mobility for their robots, but then offer a variety of end effectors, including passive ones like scrapers or active effectors that can manipulate tools. This enables a single robotic investment by a contractor to extend across multiple tasks. Sarcos takes a software-forward approach, and an interface enables end users to perform a task analysis and teach a robot to perform new tasks that can then be duplicated at scale.
Early use cases include:
- Hydroblasting
- Media blasting
- Grinding
- Spraying
- Application
- Torque tooling
- Coating
- Petrochemical surface prep
- Maintenance
- Solar panel installation
“We automate things that are dangerous, at height because that means paying a premium for labor, but also support staff and safety,” Sarcos Executive Vice President and Chief Product and Marketing Officer Kristi Martindale told IRONPROS in a briefing before CONEXPO. “Maybe a contractor can also eliminate scaffolding.
“In solar, we are solving the problem caused by conditions at these sites,” Martindale said. “A human can only work for 20 minutes before they need to rest or go back in air conditioning. With our robot, a person is not lifting the solar pane, which is heavy and awkwardly shaped. We can get people out of workflow and enable placement of panels without somebody being there. That is a huge cost savings.”
The suction-based end effector used by Sarcos for the solar panels according to Martindale help prevent micro-fissure cracks that are invisible until final testing.