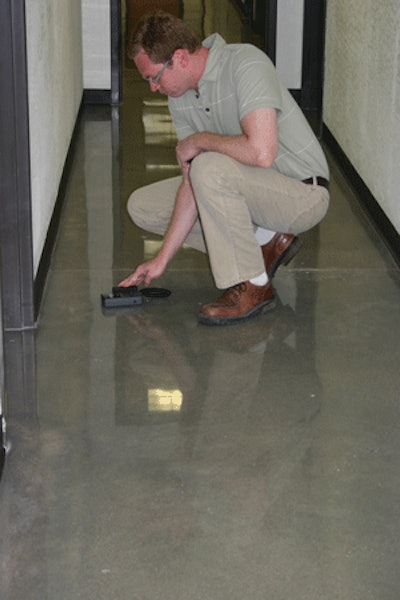
Pat Kelly, manager for a Toyota forklift dealership in Kansas City, Mo., knew he wanted shiny gray concrete floors on 1,200 square feet of his new location. The question he brought to Jameon Schwarz of Pro Concrete Designs, Raytown, Mo., was: Is it better to have acid-stained concrete with a sealer on top? Or is polished concrete the way to go?
"I explained the biggest issue with the acid-stained concrete is the sealer," Schwarz said. "It wears off and scratches. Then you have maintenance issues.
"On polished concrete, due to its hardness and abrasion-resistance, you can have conference room chairs sliding around, or chairs on rollers, and still eliminate scratches and wear-through."
With a green light to install polished concrete floors in the building's entryway, main hall, training room and parts room, Schwarz started work at Shoppa's Mid-America Toyota forklift dealership in mid-June.
When he arrived, Schwarz and crew found the 20-year-old red carpet covering most of the concrete floor had been taken up. Unfortunately, much of the petrified adhesive remained.
"It took us a day-and-a-half just to grind the glue off," Schwarz said. "That was the toughest part of job. Once we got the glue off and the base grind was done, we just flew through it."
With the floor ground to 200 grit from an HTC800 "Powergrinder," the Pro Concrete Design crew applied PROSOCO's Consolideck® LS™ (lithium silicate) hardener-densifier with pump-up sprayers. Tests have shown LS™ increases abrasion-resistance up to 27 percent over untreated concrete.
After a 90-minute dwell-time for the LS™, Mr. Schwarz was back on the floor with the Powergrinder, taking the hardened floor in stages to an 800-grit finish. He then colored the concrete with two coats of Consolideck® GemTone Stain Welsh Slate. The water-based stain soaked into the polished floor bringing the concrete a much richer, deeper almost pearly shade of gray.
"I chose that color because it looked good with the carpet and furniture in the offices," Kelly said.
Following a short dwell, Schwarz took the finish to a dazzling 3,000 grit finish, then locked in the shine by burnishing on a micro-thin layer of Consolideck® LSGuard™ at 3,000 rpm with an 800-grit twister pad.
LSGuard™ further improved the floor's light-reflectance, stain- and spill-resistance, and hardness.
Start to stop, the job took five days, Schwarz said. What does Kelly think of the finished floors?
"They look awesome," he said.
Schwarz is pleased with his handiwork as well. He plans to use the Shoppa Mid-America floor as a showcase for Pro Concrete Design's work.
"Pat told me I was welcome to send potential clients over to see the floors," Schwarz said — "as long as they're interested in buying forklifts."
Visit Prosoco at www.Prosoco.com.