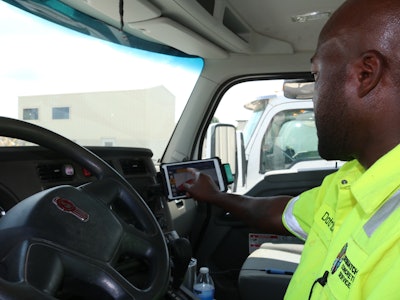
Overview
Customer Profile: Established in 1954, Sequatchie Concrete Service Inc. is a family-owned company and leading producer of concrete construction materials in the southeast, serving customers in Tennessee, Alabama and Georgia.
Business Challenge: Sequatchie Concrete was looking for a better way to track the individual performance and operational efficiency of the company’s geographically distributed plant locations. The organization also wanted to give dispatchers, managers and operators better visibility into fleet operations with instant communication and real-time vehicle location tracking. Looking for these capabilities and to modernize operations overall, Sequatchie Concrete turned to Trimble Construction Logistics for the solution.
Solution: Trimble TrimFleet suite, TMT Fleet Maintenance solution, TrimView and a number of additional modules:TrimView Direct, Communicator, DVIR, V-Sight Diagnostics and Navigation.
Benefits:
- Automated delivery of daily Department of Transportation (DOT) ready mix vehicle inspection reports – eliminating the need to collect paper vehicle logs and manually input data.
- Dispatchers and plant managers can track trucks directly to a plant for better asset tracking and cost analysis; including, live truck mapping, order tracking, real-time alerts and fuel and diagnostics updates.
- Streamlined company-wide communication using TrimView Communicator and Zello for push-to-talk (PTT) communication between drivers, dispatch and managers.
- Trimble products can identify operational efficiencies that can make the solution cost neutral after the first year of deploying the equipment.
- Continuous cost savings from better insight, machine management, shorter cycle times and improved equipment maintenance and replacement – which can potentially save thousands if costly vehicles are identified early.
Sequatchie Concrete was founded in 1954 in the Sequatchie Valley of Tennessee. What started as a ready mix batch plant consisting of two aggregate bins and a bucket elevator has grown into a full-scale concrete and construction material operation.
Celebrating more than 60 years in business, Sequatchie Concrete is known as a premier concrete producer delivering ready mix concrete, commercial and residential block, architectural block, retaining wall block and structural precast products across the South. The organization has over 300 employees, more than 150 vehicles in its fleet and approximately 20 locations across the region. Brian Van Fleet, Operations Manager at Sequatchie Concrete, explains that the company was looking for sharper insight into overall plant operations and selected Trimble Construction Logistics equipment because of its solid reputation and pre-built integrations into its dispatching software.
“We saw that Trimble Construction Logistics could help us standardize our operations, providing us the ability to see individual truck productivity; looking at things like equipment revenue, versus costs broken down to a granular level,” said Van Fleet. “We wanted the ability to track vehicles back to specific primary plants, which would help us manage the entire fleet more effectively; including billing, product deliveries, order tracking, inspections, and looking deeper into things like managing engine hours per yard of material delivered.”
Stephen Byrd, IT Director for Sequatchie Concrete, explains that the company adopted the Trimble TMT Fleet Maintenance system and TrimView components of the Trimble Construction Logistics suite, as well as several modules, including: TrimView Direct, Communicator, V-Sight Diagnostics and Navigation. To begin, Byrd and his team worked with Trimble to deploy TrimView and build integrations into the organization’s dispatching software, Jonel. They also synced the software with the company’s ERP system. With these integrations, the TrimView system can automatically collect information about truck location, products, truck maintenance and customer ticket tracking. Managers can also log into the TrimView system to gain insight and access reports showing day-to-day truck activities and operational performance as a whole. It also includes billing truck activity and maintenance directly to the appropriate plant, even if a truck starts the day with a load from one plant, and finishes at another.
Van Fleet said the team selected the TMT Fleet Maintenance system for the ability to monitor and streamline truck maintenance schedules across all plant operations. This includes monitoring and scheduling preventive maintenance, parts inventory, fuel and tire levels and technician hours worked.
The Trimble V-Sight module helps track machine maintenance by providing real-time, remote diagnostics and a detailed description of vehicle fault codes. The mobile app, TrimView Direct, then collects and integrates data from Trimble’s TrimFleet Suite to give drivers, dispatchers and managers access to instant information. The app displays a dashboard of operational data that can be filtered by each manager’s preference using graphs, charts and timelines. From the application, plant managers can see driver hours and performance as well as dive into data from the drum rotation sensors inside the ready mix trucks.
“Because we’re integrated with the dispatching software, TrimView and TrimFleet show us every single event that happens to a truck – from ticketing and loading, to discharging, delivering and washing down the truck,” says Van Fleet. It’s all broken out and we can see where that truck is at any given moment. We couldn’t see that before, and that lack of visibility was holding us back. Now, plant managers can view all truck event details to provide real-time updates to sales and customers. Our drivers are also provided with important information about their order; including mix designs, address, and turn-by-turn navigation to the jobsite.”
With the TMT fleet maintenance system, Van Fleet explains that Sequatchie Concrete is also working to streamline its daily vehicle inspection report process. Historically, each day drivers were required to inspect their vehicle and truck mixing components. Those vehicle logs were then collected daily, manually logged into the system and shared with the Department of Transportation. Today, the company can create custom reports that can be leveraged and submitted at the start of each shift. Because Sequatchie services several states, Trimble also provides necessary accurate mileage by state reports, using GPS, eliminating paper and potential for human error.
“The old process required our safety and environmental manager to collect and manually enter data from each driver vehicle log every single day,” said Van Fleet. “We were doing this 20 days a month for 150-plus trucks each day, so there’s a lot of information to be collected. Now using the tablet inside each vehicle, drivers can evaluate the condition of belts, hoses and mixing components and quickly submit the required information from the truck, directly to TMT to alert the shop of service requests. It’s a lot more efficient and removes paper from the equation.”
As a feature of TrimView office software, the team also uses TrimFleet Communicator and TrimFleet mobile for real-time communication between each driver and dispatch. The VoIP system uses cellular coverage combined with Internet voice-calling to replace traditional radio truck communications. TrimFleet Communicator is also integrated with push-to-talk (PTT) application Zello for Work. Byrd explains that from a dash-mounted tablet inside each truck, the company-wide communication system lets drivers quickly and simply communicate with any other driver, manager, customer, or dispatcher with the push of a button. They can also access frequent contacts or specific channels, and they can make point-to-point calls at any time. Managers can also access voice activity logs and manage channels from their desk or on-the-go from a smartphone or mobile device.
Van Fleet believes TrimView and the other modules will continue to drive productivity gains across the company’s plants and ready mix concrete delivery cycles. He predicts the investment in technology can be cost neutral after the first year of deploying the equipment by managing through the data provided. He also expects continuous improvements from having better insight, shorter cycle times and improved machine maintenance and replacement, which he estimates could save thousands of dollars if costly vehicles are identified early.
“The beauty of what we get from this technology is that it tells the story of every single driver, every day,” says Van Fleet. “We have all the information we need to make solid decisions based on real-time data about our drivers, costs, materials and machines. This lets us give real-time updates to our customers about orders, delivery times, water meter values – and pretty much anything else they might want. In the business of concrete, differentiating yourself is all about good communication and delivering a “Done Deal” for our customers. This technology helps us do that.”
Ed Note: Rebecca Muhlenkort is a freelance writer who covers technology for the construction industry.