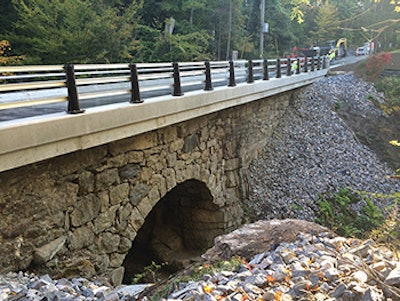
Oldcastle Precast’s Skilton Road Bridge Rehabilitation and Interstate-10 Tex Wash Bridge Emergency Replacement Projects were recipients of Precast/Prestressed Concrete Institute’s (PCI) 2016 Design Excellence Awards.
During the 54th annual PCI Design Award Program, twenty-six awards were presented to projects across North America, including best-in-class awards for both transportation structures and buildings, as well as special awards for industry advancement, sustainable design, and all-precast concrete construction.
Skilton Road Bridge Project - Recipient of PCI’s Best Rehabilitation Bridge Award & ACEC/CT Engineering Excellence Merit Award
Skilton Road Bridge, a one lane, dry stone masonry arch bridge originally built in 1865, required special consideration to preserve the historic nature of the bridge, increase the width to accommodate two traffic lanes, and add a sidewalk on one side of the bridge.
The designers considered several potential solutions to rehabilitate the structure, and ultimately decided to install a new superstructure consisting of precast, prestressed concrete slabs that would bear the load of the new road structure, thus preserving and protecting the entire historic structure below. “The use of prestressed, precast concrete beams enabled the bridge to be widened while minimizing the impact on the existing bridge,” says William Andres, associate with Tata and Howard, the engineer for the project.
A key advantage to utilizing precast, prestressed concrete on this project was that the precast concrete slabs were cast while demolition and construction of new beam seats were being completed, which shortened the project timeline and minimized disruption. It also reduced the time needed to detour traffic around the construction site, and eliminated the need for scaffolding and formwork. “That made it made it less expensive than a cast-in-place design,” Andres says.
The precast concrete slabs were prestressed to resist the required construction loads and to carry the required in place design loads. Instead of orienting them in the normal longitudinal direction, the slabs were installed transverse to the roadway, extending out roughly 5 ft beyond the existing stone masonry walls. Installation of the slabs took just 1 day.
“Typically, these types of precast, prestressed slabs are transversely connected using grouted shear keys with post tensioning tendons to ensure that the slabs deflect together under load,” Andres says. (retrieved from: Precast/Prestressed Concrete Institute. (2017)-[https://www.pci.org/Project_Resources/Project_Profiles/Profile_Pages/Repairs_to_Skilton_Road_Bridge/?terms=WATERTOWN].
The precast-prestressed concrete slabs forming the superstructure were designed, engineered and manufactured at Oldcastle Precast’s Rehoboth, Mass. facility.
PCI #24 Repair to Skilton Road Bridge
Engineer of Record: VB Technologies Corp., Rocky Hill, Conn.
Engineer for the Project: Tata and Howard, Mass.
Contractor: Black & Warner Construction Company, Unionville, Conn.
Owner: Town of Watertown, Watertown, Conn.
Precast Producer: Oldcastle Precast, Rehoboth, Mass.
Precast Concrete Specialty Engineer: Eriksson Technologies, Tampa, Fla.
Additionally, the Skilton Road Rehab Bridge Project, with Tata and Howard, Mass as the engineering firm, received a 2017 Engineering Excellence Merit Award from the American Council of Engineering Companies of Vermont (ACEC/CT).
Interstate-10 Tex Wash Bridge Emergency Replacement Project - recipient of Honorable Mention in PCI’s Bridge with a Main Span from 76-149 Feet category
The Interstate-10 Tex Wash Bridge Emergency Replacement Project, was constructed using cutting-edge precast concrete bridge elements manufactured by Oldcastle Precast in Perris, California. Recognized as an innovative precast solution, the use of precast concrete allowed the project to meet the stringent requirements of the California Department of Transportation and delivered the speed required to replace the bridge in only two months.
Timing was critical for this emergency project, and designers took advantage of the many benefits of precast concrete to meet the rapid delivery goals. Using precast concrete girders eliminated the need for temporary falsework, which accelerated girder placement and limited the environmental impact on the channel area. Precast concrete segmental abutment and wingwall elements were used to accommodate a staggered construction schedule. In addition, an adjacent precast concrete girder arrangement meant the project did not require deck forms, which further shortened the timeline.
Owner, Engineer of Record, and Architect: Caltrans, Diamond Bar, Calif.
Contractor: Granite Construction Company, Indio, Calif.
Precast Producer: Oldcastle Precast, Perris, Calif.
A widely-regarded industry program, the PCI Design Awards recognize and honor design excellence and construction quality in buildings and transportation structures using precast/prestressed concrete elements. The program demonstrates how designers are continuing to use precast/prestressed concrete construction to achieve sustainable, cost-effective, resilient and aesthetically versatile projects.