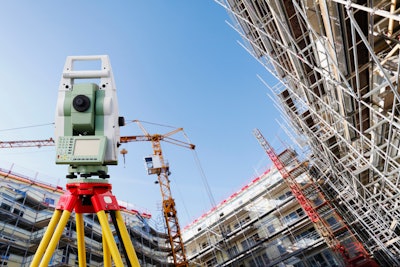
One barrier to increasing productivity in construction is the remote and dynamic nature of where, how and when production takes place. A manufacturer may implement a manufacturing execution system (MES) that brings formal processes to work-in-progress (WIP), including task and resource scheduling, capture of production as it is completed and even integration with automated machinery.
Construction is catching up fast with the growth of the Field Productivity Software product category. Like an MES, field productivity software takes the project plan and breaks it into work packages assigned to workers, crews, subcontractors, even to equipment. Some of these software products are aimed more directly at the heavy/highway civil construction space, and some can integrate telematics data from heavy equipment or even hand tools to monitor utilization and even production delivered.
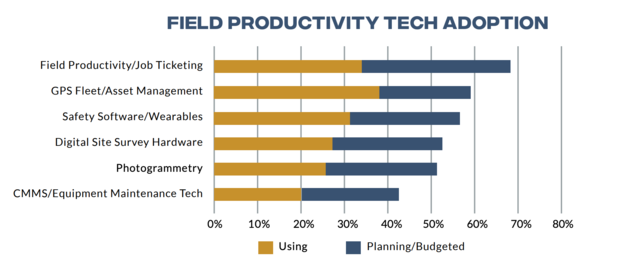
READ THE IRONPROS STUDY ON FIELD PRODUCTIVITY SOFTWARE AND OTHER CONSTRUCTION TECH ADOPTION
Raken, Booth #N12276
While pretty much any contractor could benefit from some type of field productivity solution, Raken’s software is also designed to capture value put in place, and most of the work completed on projects is completed by subcontractors.
“Right now, we are effectively serving subs with production management, work-in-place management, photo management—but we also work with some generals,” Raken Senior Solution Sales Manager Brian Poage said in a 2022 debriefing call with IRONPROS. “We currently integrate with project management softwares like Procore, and we are building out a more extensive integration with Procore to serve a some of our existing customers. We also integrate with accounting packages including those from Sage, Foundation, Computeze, and are looking at integrations with drawing solutions and other software.”
While Raken did not at the time of the call consume telematics data, it does capture equipment utilization that field workers enter into the app, including cost codes. Raken helps contractors capture these details in the field and then surfaces that data to processes in the back office portions of Raken and to construction enterprise resource planning (ERP) software through integrations.
“We track equipment in our software—and this feature is not as robust as the OEMs—but you can record whether you have the equipment on the job site and how long has it been there,” Poage said. “Asset management software is about maintaining equipment accurately based on utilization and then keeping it maintained. What our customers track in Raken is how they are using equipment. The software has the ability to capture the amount of hours used and right now is pushed to ERP, with more project management software specifically—on the roadmap for further integrations.”
Raken extends into and construction site activities and processes in ways that not only streamline, but document them. This can eliminate a lot of non-value-added work around things like safety training through embedded toolbox talk materials and then, the ability to document that employees were exposed to the information.
“If you are out in the field and conducting your daily business, you are using Raken for capturing time for your crews when you start work, what material got work in place completed,” Poage said. “You can identify quantities, attach photos to back up quantities, quality or safety issues. You can record equipment used to complete that work in place. We include standard pre-inspection checklists, safety or quality walks, with that information transferred into a daily report that submits it to external stakeholders and to other departments.”
Raken is definitely a field execution system, but it also offers some useful standard packaged analytics including:
- Production insights so a project team can upload a budget for insights on whether a project could be successfully executed against it.
- Tagging hours to a specific scope of work enables comparison to plan
- Analytics around delays and workplace incidents
HCSS, Booths #N12125 and #W41566
HCSS is much broader than field productivity, with modules extending into construction ERP, estimating, equipment management and more. But HCSS HeavyJob straddles
Once you win the work, HCSS HeavyJob takes over the project lifecycle, tracking cost against projects, digitizing time cards and uniting the field to the front office.
What is impressive about the mobile interface is the design, simplicity and intuitive nature of the interface. Here we see a mobile interface used for timecard analysis, which to me looks almost as intuitive as other solutions for entering time.
HeavyJob makes the important numbers, for instance, very prominent, sticking a variance column all the way to the right. The software also provides insight on how to get the project back on track. And this data is super current because unlike many settings where labor cost is only added to the project financials after payroll is run, this ports n here in real time from the timecard and functionality that applies wage rates and business rules accordingly.
There are out of the box tools for common project financial metric like estimate at completion and estimate to completion but then HCSS Intelligence lets you bake your own views if you have something more exotic in mind.
Another significant part of the offering is the Equipment 360 product for fleet management, maintenance and telematics that supports more than 10,000 telematics units operating on heavy equipment.
In all, HCSS offers a broad suite of applications designed for interoperability, but also integrate with multiple products that compete with slices of the offering, including SIS Construct365.We can expect more functionality from HCSS designed to ingest, surface and drive value from data from connected external software and devices.
Assignar, Booth #N12732
Assignar, meanwhile, goes deeper into equipment to the point it can support capital spending decisions, as IRONPROS learned during a 2022 debriefing with Assignar CEO Sean McCreanor.
Assignar includes equipment maintenance functionality including reminders for scheduled maintenance tasks and capturing information on failures as they happen. McCreanor said the company was also pursuing integrations with Caterpillar VisionLink, Tenna and Komatsu’s Komtrax.
Because it has one foot in field productivity and the other in equipment and maintenance, it gets easier to schedule maintenance around project demand or avoid scheduling a machine for production when it is in fact in the shop. Assignar can also expose equipment data on how utilization of equipment classes should impact a capital construction equipment budget.
Sage, #N12476
While the Sage Field Operations solution extension to the Sage Intacct construction ERP product is not equipment focused, it brings a degree of flexibility many other field productivity solutions do not. That is because it straddles the worlds of field productivity for construction projects as well as field service management for functions like installation, service, repair and maintenance. In a project environment, an employee or crew is typically on site for a day or more, whereas in field service management a single employee or crew is typically at multiple sites a day. Scheduling, tracking, task management and other functions vary slightly between the two, but in many contracting companies, the same pool of employees split their time between initial construction and service provision. Sage Field Operations solves this problem.
On the construction project side, Sage Field Operations pulls from construction functionality already built out in Sage Intacct.
“We pull the job information directly from Intacct directly into Sage Field Operations,” Operix Partner Enablement Manager Kathleen Sherman said in a 2022 debriefing call with IRONPROS. “This gives us the ability, in our scheduler, to schedule jobs by cost code to team members. That makes us unique because if we want to schedule a task for a job or a work order for field service to the same individual, we can do that. Both of those pieces of information will be on our schedule board. A contractor is able to see their assignments from the assignment page on any device, and can clock in out or enter whole hours.”
Sage Field Operations is more of an enterprise application than some other applications in the space, and allows for a multi-step approval workflow for time sheets and project labor hours. According to Sherman, Operix plans to integrate this workflow with the Sage Payroll solution for Intacct, which in fact is created by Penta of Brookfield, Wis. Contractors running other payroll solutions could port data in by integrating with Sage Intacct’s time and attendance module.
Other construction field productivity solutions may go deeper than Sage Field Operations in the area of safety, where some vendors may have baked-in functionality and toolbox talk content and Sage offers their custom forms which can be configured to facilitate a safety program. When forms must be filled out, they can be delivered as hard-to-ignore pop-ups in the application.
An integration point with Sage Intacct to capture equipment hours is still on the horizon, and according to Sage Intacct Principal Product Manager Kyle Watt, Sage Field Operations fills a very different purpose for a contractor than a more equipment-facing field productivity solution like Assignar, which has its own integration partnership with Sage Intacct.
EquipmentShare T3, Booth #N11462
While EquipmentShare has a foot solidly in the rental equipment management market, its T3 operating system for construction aims to unite the people, materials and equipment used on a construction site using artificial intelligence (AI), the internet of things (IoT), mobility and cloud.
Apps in the T3 suite include:
- Fleet: OEM-agnostic telematics
- Time Tracking: Schedule management, labor time card capturing, work order management and more
- E-Logs: Electronic Logging Device compliance with digital reporting
- Analytics: Customizable reports on utilization, job cost and more
- Work Orders: For equipment maintenance
- CRM: Track vendors and customers
The product is growing in scope rapidly, and newer functionality encompasses:
- Cost Capture: Record expenses from a mobile device along with invoices for full expense management
- Inventory: Plan inventory consumption across jobs with a streamlined intake and parts order workflow
- Rent Ops: Manage assets on projects with external and internal rental functionality
Other Field Productivity Vendors To See at The Show
- AboutTime Technologies/Workmax, Booth #N10318
- AGTEK, Booth #N12325
- Busybusy, Booth #N10855
- Cenpoint Software, Booth #N12934
- Connixt, Booth #N13043
- CrewTracks, booth #N10863
- FieldFlo, Booth #N10148
- SiteSense, Booth #N11068
- Vizzn Inc., Booth #N11335