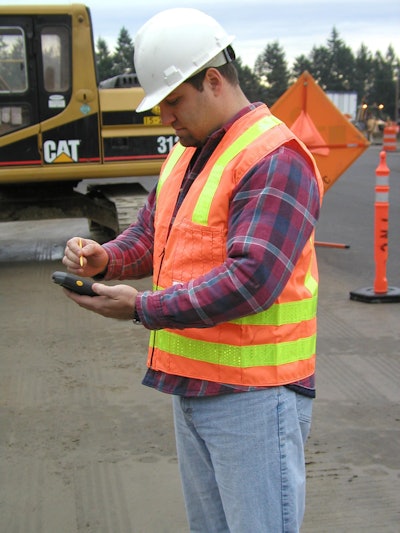
Mobile devices combined with software solutions are now offering contractors the opportunity to manage employee labor hours, equipment usage and production while on the jobsite. This type of mobile management can be done right on the job, usually by a supervisor in the field, using mobile devices including special handheld devices, smart phones, laptops and tablets. With a wireless signal, this information can be sent in real time directly to the office and even integrated right into the payroll system without the need to re-record.
"Now more than ever, construction companies are providing mobile devices to their field employees," points out Wood Flynn, senior consultant for construction software manufacturer Equential.
Mobile management software allows supervisors and field crews to track labor and equipment hours as well as production quantities on the jobsite without the need for Internet access. The info can be sent directly to the office or payroll software when Internet access becomes available. These mobile solutions and their instantaneous nature allow contractors to send and retrieve information from the office related to the project quickly, which means the employees on the job can be armed with better information while onsite, adds Jim McFarlane, president and CEO of Explorer Software.
Construction and company managers know what is happening on a jobsite in a more timely manner than if they had to wait until the end of the day or week. They can make corrections or changes as needed to help achieve cost savings on the job. Mobile management devices combined with construction software can help reduce the time it takes to manage multiple jobsites, ExakTime Chief Technology Office Scott Prewett says.
"These solutions allow you to report against progress on a daily basis and make adjustments and decisions based on results they can see on a daily basis," Flynn says. This can often allow tighter management of progress.
The accuracy of mobile management software is one of its biggest benefits, says Brad Mathews, vice president of marketing for Dexter+Chaney. "If somebody comes into work six minutes late but their timecard still reflects they came in at eight o'clock, in a paper process that's not going to get captured very often. With an electronic process that can be captured," Mathews says. "Those numbers add up over time and result in reducing the actual labor costs on the job."
Mathews also points out that with a paper system, timecards might not be filled out until the end of the day or even the end of a week. That opens up the potential for human error trying to remember exact time and production quantities. With mobile tracking, labor hours and production can be recorded right away to eliminate that human error.
Mobile management systems not only benefit current jobs, but they can also affect future bids. "It helps us bid jobs in the future more effectively because generally people review the effectiveness of their bidding based on their job costing," Mathews says. With more accurate job costing, bids can be more accurate.
Employee Adoption
"There is a right and wrong way to introduce mobile management," Prewett says. Some employees used to self-reporting may feel that management does not trust them to record their hours. However, if management explains the purpose and benefits of automating labor tracking, Prewett says employees can be more accepting of the change.
Maybe the biggest perceived challenge is that field employees will not want to use mobile devices to track employee and labor hours. "Contractors may be concerned about burdening employees or that the employees won't take to the new system," Flynn says. "However, we find that once those employees begin to use it they figure out it's pretty easy."
It is important to note that no mobile management system can make a bad employee a good employee, Prewett says. If employees are committing outright fraud, practicing unacceptable working habits or buddy punching, a mobile management system can help identify where these problem employees may be, but it cannot correct the problems or change someone's nature.
Some employees may not use mobile devices in their daily lives, so some explanation and training on the hardware may be required. But as Flynn points out, many employers are already equipping their crews with mobile devices. Many devices are less expensive than they have been in the past, McFarlane says. The barrier to entry is lower than it may have been in previous years.
Prewett suggests construction companies allow for at least a 30-day transition period from paper management to automated mobile management. He suggests dovetailing the processes for a couple of weeks by recording on both paper sheets and the mobile devices before changing over to mobile only.
ROI
As Mathews sums it up, "mobile management solutions can create real dollar savings in the field, time savings in the office and more accurate time keeping." Software manufacturers agree that most customers can see results from mobile management solutions quickly. Employees don't have to spend as much time recording, reporting and processing hours and payroll. With these mobile solutions, companies may be able to reallocate resources and employees to other areas that need more help, McFarlane adds.
"There are so many degrees of usage potentially available," Flynn says. "Depending on how a company uses a system the ROI can be very significant."