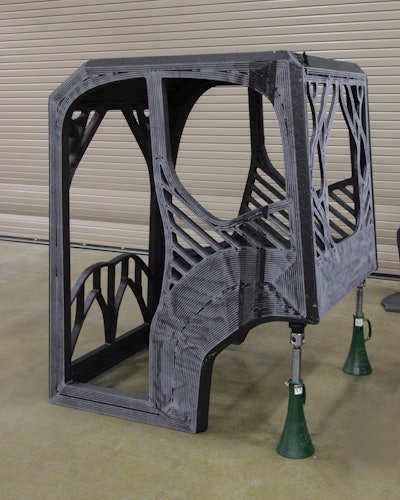
The theme of CONEXPO-CON/AGG 2017 is “Imagine what’s next”. No where will that be more prevalent at the trade show than with the world’s first fully functional, 3D printed excavator — known as Project AME (Additive Manufactured Excavator) which will be on display at the show’s Tech Experience. This prototype leverages large-scale additive manufacturing technologies and explores the feasibility of printing with metal alloys.
According to the Association of Equipment Manufacturers, “Project AME is not just about 3D printing. It’s about bringing together many intelligent people to work on a number of challenges while accomplishing a common goal.”
“It is important that future engineers and users understand the tremendous potential of additive manufacturing for their equipment and that it isn’t that far out in the future,” says Michael Gust of the Center for Compact and Efficient Fluid Power. “Imagine the design and inventory flexibility it could provide. Unique design features will be able to be added to standard designs with little cost impact from a manufacturing, tooling or inventory perspective.”
A collaborative effort
The 3D printed excavator is the brainchild of collaboration between many organizations including the Association of Equipment Manufacturers (AEM), the National Fluid Power Association (NFPA), the Center for Compact and Efficient Fluid Power (CCEFP), Oak Ridge National Laboratory (ORNL) and academic partners Georgia Institute of Technology (GT), University of Illinois at Urbana-Champaign (UIUC) and the University of Minnesota (UMN).
The idea of 3D printing an excavator was born back in 2014 after members of CCEFP toured the ORNL facility and saw what was being done with 3D printing. CCEFP was initially awarded a grant from the National Science Foundation (NSF) to 3D print the full-scale operational excavator.
“We’re not printing the whole excavator — that’s not the goal,” says John Rozum of AEM. “What we did was select a handful of critical systems that make an excavator an excavator — the cab, the boom/stick, and the heat exchanger — and reinvent them in a way only made possible through 3d manufacturing.”
[VIDEO] Behind the Scenes of First 3D Printed Excavator
CCEFP collaborated with research teams from Georgia Tech and the University of Minnesota on how to convert the current excavator design into one that was conducive to 3D manufacturing.
Graduate engineering students and professors from the University of Minnesota were responsible for designing a hydraulic heat exchanger and cooling system that would reduce the size and weight of the excavator while increasing the machine’s cooling efficiency.
In addition, graduate engineering students from Georgia Tech created the steel boom, stick and bucket, which features integrated hydraulics. Part of the design’s goal was to decrease weight, materials cost and maintenance.
The CCEFP team held a nationwide cab design contest open to undergraduate students. Student engineering teams from across the country submitted designs for a futuristic excavator cab. A panel of industry experts judged the designs and ultimately selected the design from the University of Illinois at Urbana-Champaign (UIUC) student engineering team as the winner.
The UIUC team created a fully functional 3D printed excavator cab that was also aesthetically pleasing. The cab was printed with an additive manufacturing machine that used carbon fiber-reinforced acrylonitrile butadiene styrene (ABS) plastic.
[VIDEO] Watch Excavator Cab be 3D Printed
The remaining parts of the excavator will be traditional components, Gust says.
3D printing
The excavator cab and components were printed at the Oak Ridge National Laboratory’s (ORNL) Manufacturing Demonstration Facility in Knoxville, Tenn. ORNL was responsible for developing all the processes required to 3D print the excavator components. Various machines helped create and assemble the cab, boom and heat exchanger. The printing began in August 2016 and was completed in January 2017.
“There’s no tooling. You go straight from the CAD model to the part. We want to highlight how additive is more than just one process, one type of material,” says Lonnie J. Love, corporate research fellow at Oak Ridge National Laboratory.
“On the cab we’re going from pellets to the part, and it’s plastics and composites. On the boom we’re going from the welding wire to the part, and it’s going to be steel. And then on the heat exchanger we’re going from powder — using a laser — to the part,” Love says.
Love says the most challenging part of the program was creating a whole new additive system to rapidly manufacture large metal parts. ORNL partnered with Lincoln Electric and Wolf Robotics to create the new additive system, which was used to manufacture the stick and boom.
The Wolf/Lincoln Electric Large Scale Metal AM manufactures large steel parts by using a robot to move a MIG welding head around, growing the part layer by layer.
ORNL used a laser powder bed fusion system to manufacture the aluminum heat exchanger and the Cincinnati BAAM to manufacture the composite cab.
The laser powder bed uses a laser to melt, layer by layer, aluminum powder, according to Love. A raking mechanism spreads a thin layer of aluminum powder over a plate. A laser then melts the powder correlated to the cross section of the part at that specific layer. A table moves the plate down, spreads a new layer of powder out and then melts the next layer. This process repeats over and over, building the part layer by layer.
The Cincinnati BAAM manufacturers very large carbon fiber reinforced thermoplastic parts. The system uses injection molding pellets as the feedstock. The pellets are fed into a single screw extruder mounted on a gantry. The gantry moves the extruder around, melting the pellets and growing the part layer by layer, Love says.
The printing of the cab was completed in October 2016 while the stick was completed in January 2017 with anticipation it would be integrated onto the functional excavator in February.
Fluid power
It’s not just the 3D printed excavator components that are important to Project AME. Project AME also incorporates some fluid power advances including printing the hydraulic system directly into the boom with no exposed hoses or components. Also, the hydraulic oil reservoir and heat exchanger could be integrated as a single component for storing and cooling the hydraulic fluid in one place.
Project AME in action
The completed 3D printed excavator will be on display in the Tech Experience in Silver Lot 3 (outside the Las Vegas Convention Center) at CONEXPO-CON/AGG and IFPE. The fully functional excavator will be operating in job-like conditions and moving earth. Some of the innovative designed and printed components will also be on display.
“As we develop the technology we’re really trying to demonstrate where it can be used so it’s commercially viable,” says Love. “Our goal is to develop technologies that can be used by the construction industry to increase their pace of innovation. Near term applications include tooling and manufacture of replacement parts without the need for an inventory.”
“While it may not be practical or cost effective to print an entire excavator, the processes used to create AME prove that the technology can be used in practical ways to help design and build machines that are lighter, stronger and more efficient than what we’re used to with traditional manufacturing,” Rozum adds.
In addition to seeing the completed 3D printed excavator, the Cincinnati BAAM and Wolf/Lincoln Electric Large Scale Metal AM printing processes will also be demonstrated live at CONEXPO-CON/AGG and IFPE show.
After CONEXPO-CON/AGG, the 3D printed excavator will likely go on tour to increase visibility of not only Project AME but the 3D printing processes behind the project as well.