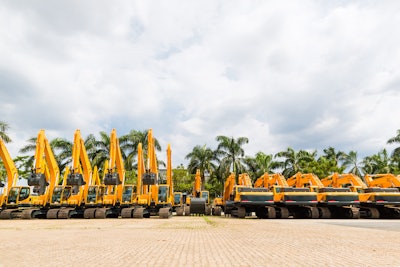
Telematics can help boost productivity on construction sites. According to Trimble, a company specializing in construction telematics, connected construction can help businesses increase productivity by 30 percent. So how exactly does a business use data to increase productivity in their operations?
The first step in leveraging data-driven insights is collecting information from connected machines and tools on the jobsite. This can range from large excavators and material handling equipment to cordless hand tools and wearables. There are many types of data available on construction sites, capable of providing the feedback and information you need to minimize risks when making operational decisions.
Collecting and Leveraging Data on Construction Sites
1. Vehicles: Engine Overspeed
Monitoring an engine’s overspeed rates through remote diagnostics can help equipment managers predict when construction vehicles are due for maintenance, as well as gain a thorough understanding of the challenges of the jobsite. Critical overspeed settings vary depending on the vehicle or motor type. Generally, engines hitting overspeed conditions are prone to reduced lifespan and engine failure, which influences maintenance, budget and rebuild strategies. Overspeed can also cause the engine to generate unwanted heat, resulting in higher operating temperatures associated with damage. Engine overspeed could serve as a warning for dangerous working conditions on the jobsite and should not be taken lightly.
“When we see engine overspeed, the first thing we take into account is the type of machine reporting out the data. Let’s use an articulated truck as an example. Is it happening on one part of the job? Is it happening all over the job? It is critical to know not just the frequency of triggering engine overspeed, but also where it is happening on the jobsite,” said Jason Threewitts, performance services manager at Carter Machinery.
With more than 90 years of experience in the construction sector, Cater Machinery sells and supports Caterpillar equipment for construction projects. The company has an expansive network consisting of more than 30 locations across the United States.
“This information will tell you a couple of things. If it is happening across the worksite, then it is probably an operator thing. If it is happening on one specific part of the job, it is probably less of an operator issue. Instead, it could be an indication that this part of the job is dangerous. Maybe I need to go out there and check the area to prevent an unsafe situation,” said Threewitts.
Equipment managers monitor overspeed on construction sites using remote diagnostics. Remote diagnostics refers to real-time monitoring of the vehicle’s status (in this case, overspeed). Upon detecting overspeed conditions, a fault code associated with the condition is triggered and a signal is transmitted to a management platform via a telematics device. These days, newer machines come with factory equipped telematics devices that can be used to capture engine overspeed data. A timestamp, vehicle identification and location data may come with the fault code during transmission.
Engine overspeed data can be combined with other types of information on construction sites for in-depth jobsite analysis.
“It is never just one thing. When analyzing the full situation, how can I continue connecting the dots all the way through? So then, I would start looking for related things. Am I getting an overheat reading at the same time while getting an engine overspeed condition? Am I getting filter plugging issues at the same time? Do I have engine or transmission oil samples coming out of the machine that is telling me something else? When you start adding all of that up together, if you have correlating data sets based on either other fault codes or sources, like an oil sample, then you have some powerful information to determine if you have a machine issue, how rebuild life is being affected or if you need to talk to the operator about how they are using the machine,” explained Threewitts.
2. Workers: Fall Detection Rates
When it comes to safety, fall detection is a critical piece of data to monitor in worksites. Falls, slips and trips are very common in the construction sector.
“The construction industry accounted for 46.1% of all fatal falls, slips and trips in 2020,” according to a report from the U.S. Bureau of Labor Statistics. Falls are tracked using gyroscope and accelerometer sensors on smart watches, tablets or safety devices. Some devices can detect both a normal fall and a hard fall. These wearable devices generate loud auditory alerts and issue emergency notifications to specified contacts or project management platforms in the event of fall without a response, increasing the possibility for workers to receive immediate medical attention.
In addition to monitoring individual falls and slips, there are several benefits to tracking the rates at which they occur. Tracking the frequency of falls over a period of time can expose gaps in safety protocols. To make tracking fall detection rates effective, a timestamp and location data should be recorded with the emergency notification for a complete assessment. This information can help ensure proper safety standards and fall protection measures were implemented prior to the fall. Falls that occur frequently around a specific machine, such as telehandler or forklift, or a specific location on a jobsite, such as fueling stations or stairways, can prompt managers to update work safety practices.
“Employers must set up the work place to prevent employees from falling off of overhead platforms, elevated work stations or into holes in the floor and walls. The Occupational Safety and Health Administration (OSHA) requires that fall protection be provided at elevations of 4 feet in general industry workplaces, 5 feet in shipyards, 6 feet in the construction industry and 8 feet in longshoring operations. In addition, OSHA requires that fall protection be provided when working over dangerous equipment and machinery, regardless of the fall distance,” according to an OSHA overview about fall protection.
3. Machines: Fuel Consumption
Fuel keeps construction vehicles and machines, such as generators and tools, operating, yet is a major cost in the budget of construction projects, usually second to labor. Monitoring fuel consumption is traditionally carried out at the fuel pump. Newer machines come with features that carefully monitor fuel consumption or fuel burn automatically without needing to manually log the information.
“When you start thinking about fuel consumption, the first thing people think about is component life. This is because there is a point in time a maximum number of gallons of fuel goes through a particular asset before you start thinking end of life. This would cause you to consider if it is time to rebuild the machine or take it down,” said Threewitts.
“I also like to think of it another way. When you start thinking about productivity, when you start thinking about how the machine is being leveraged, how much tonnage you’re moving or the load factor of that machine – that’s when fuel consumption can also be something you take a peek at and wonder how hard you are working your asset,” explained Threewitts.
Threewitts highlighted a situation wherein an operator was light-loading a wheel loader vehicle on the jobsite. The operator was not fully loading the vehicle’s bucket during each pass. As a result, the operator needed to make two to three additional passes. The operator’s thought process was that he was able to work faster without fully loading the loader bucket. Threewitts utilized fuel consumption data to show the customer that not fully loading the bucket of the wheel loader and making additional passes burned 20% more fuel, compared to maximizing the load capacity of the machine and reducing the number of passes.
“Once you start correlating fuel savings or fuel efficiency and you’re also still able to get the production and payload out of the fleet that you need; that is solid gold for a production or equipment manager. Being able to correlate those two data points together or three data points is huge,” said Threewitts.
4. Equipment: Tracking Tool Usage
Monitoring the location and utilization of hand tools and equipment on jobsites is an effective way to streamline productivity, inventory, security and asset management for businesses. This information seems straightforward, though in application there are many ways to use this data to support operations on construction sites. From a hardware perspective, this involves installing small identification tags on equipment and using wireless Bluetooth technology to transmit the data.
Cloud-based management platforms allow managers to view the status of equipment, as well as historical usage data, where they can assess how tools are used on the worksite.
"Our research shows that each jobsite loses on average one day per month of productivity due to workers searching for tools. In addition, the contractors end up spending up to 90 hours per month tracking tools: in essence, productivity loss for both workers and contractors due to lack of an effective asset/tool management platform,” said Michael McGowan, region head and CEO of Hilti North America.
The types of data associated with tracking tool usage are numerous. Monitoring the location of equipment minimizes the risk of theft and improper use of tools by individuals without adequate training for the equipment. The ability to address theft and missing equipment directly by tracking location reduces the need to replace tools, preserving the company’s budget over the long term. Preventing equipment theft also helps reduce unforeseen delays and ensures jobs are completed in a timely manner.
Next, knowing when tools are idle or in use by operators can help with allocation, as well as keep billing accurate (for rental equipment). Tracking equipment uptime is also used in predictive analytics, enabling businesses to know when equipment is needing repair or replacement. Tools that do not meet expected uptime performance can prompt individuals to bring the equipment in for inspection or maintenance. This information can also help businesses stay ahead of costs related to replacing tools by anticipating the equipment’s end of life based on accrued uptime.
“Tracking small tools — whether in repair status, on location or with employees and the associated costs — is one of the most ineffective parts of accounting and internal controls in a construction company,” said Maria Lumke, CFO of Waterline Industries, a New Hampshire-based civil general contractor.
Equipment utilization data of specific tools enables managers to track the completion of various aspects of a project. For example, a business that uses three chipping hammers for light demolition work when removing concrete for site preparation averages 10 hours of tool utilization per project. With this information, managers would know that when the three chipping hammers are at eight hours of utilization, the demolition work is nearing completion and the next phase of the project is approaching. This ability to forecast various stages of a construction project allows managers to stay one step ahead of schedule.
For businesses juggling multiple projects, the combination of location and tool utilization data for equipment is useful. Tapping into such data would enable equipment managers to allocate tools efficiently across different ongoing projects, minimizing idle time while increasing productivity.
Data Analysis in Connected Construction
A major takeaway from these examples is that in most cases, it is not the amount of data collected from machines that determines one’s ability to raise productivity. After all, there is no shortage in the amount of data you can collect from sensors and loggers found on connected machines or vehicles. Instead, it is how you analyze the data you have at hand, combine or match data sets together and assemble information that allows you to form new strategies that can enhance operations or uncover new perspectives. Ensure that the data you are collecting on the jobsite is accurate and relevant to your business goals.
Having a deep understanding of the types of data your equipment generates is a vital part of analysis on construction sites. This requires businesses to tap into readily available information generated every day by machines and equipment.