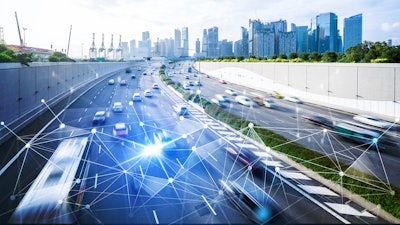
Wireless Sensor Network (WSN) technology is widely used across a myriad of industries to monitor large structures or complex environments. This monitoring solution has made its way to the asphalt sector, enabling organizations and roadway operators to remotely monitor asphalt structures from a safe distance, stay ahead of demanding maintenance schedules and avoid pavement failure through predictive analysis using data collected by sensors along the network.
A WSN is designed to monitor different types of conditions, occurrences and properties in specific areas of the asphalt structure. For instance, wireless sensors can be embedded into the asphalt pavement to monitor the temperature of the asphalt as it cools down after being laid. This information can be used to ensure that the asphalt is being laid at the optimal temperature, which can help in preventing premature failure of the pavement due to thermal cracking.
Wireless sensors can also be used to monitor strain on the asphalt pavement caused by road traffic. This information can be used to identify areas where the pavement is experiencing excessive stress, which can help in identifying potential areas of failure and informing maintenance and repair decisions in a timely manner.
The main objective of WSNs is to stay ahead of time-consuming and costly repairs through effective forecasting and analysis by implementing passive, non-destructive monitoring methods. In most cases, small changes in the asphalt’s structure occurs before major damage or notable decline in performance. Such micro changes in the structure typically go unnoticed through manual observation practices and requires sensitive instruments to detect, measure and monitor.
Know Your Nodes
WSNs have numerous working components, ranging from individual sensors and power supplies to modems for data transmission and software platforms for analysis. Because of this, deploying a WSN for asphalt monitoring tends to be very tedious. The presence of several working components increases points of failure within the system and is a considerable challenge in managing WSNs for asphalt monitoring.
A point of failure refers to a single point in a system that can cause the system to break down or become inoperable. In the case of a WSN, you could be using the latest and most reliable software for data analysis, but if the sensors gathering data in the asphalt are faulty and returns inaccurate data then the entire monitoring system is compromised.
Monitoring along the roadway is facilitated by small sensor nodes. The sensors are buried in the pavement, either by drilling into the surface or incorporated in the structure during construction. The latter method is less invasive and requires careful planning before construction.
Sensor nodes can take on a wide range of packaging styles, determined by the power supply, operating principle and application of the sensor. For example, a sensor used for monitoring structural health with an acoustic attenuation operating principle may feature cylindrical packaging. Sensors used for monitoring traffic and environmental conditions with a magnetic or vibration operating principle may have a box case packaging style. The area of installation along the asphalt structure is also a major factor in packaging style. Sensors can be installed at the top, middle or bottom asphalt layer. The area of installation is determined by the conditions the sensor is designed to measure or monitor.
For large WSNs, relay nodes must be installed to extend the network's coverage area and increase its connectivity. Relay nodes typically act as intermediaries between sensor nodes and the base station or other nodes in the network. These nodes can help to overcome obstacles such as physical barriers, radio signal interference and transmission range limitations by relaying data packets between sensor nodes and the base station or other nodes that are out of direct communication range.
Coordinator nodes are used to serve as the central point of control for the network. The coordinator node is usually a powerful node that has additional functionalities and responsibilities compared to the other nodes in the WSN.
Remote monitoring is facilitated by sink nodes, also known as a base station or gateway node. These components contain antennas for data transmission to an external network. The sink node is usually a fixed, stationary node that is located at a central location in the network. It may have more processing power, larger storage capacity and better connectivity than the other nodes in the network.
A WSN installation is considered successful if it can support 24/7 uptime with minimal onsite maintenance. This requires the hardware and system components to be extremely durable, capable of withstanding extended periods of vibration imposed by vehicles and fluctuating temperatures due to seasonal changes in weather. The data generated by the sensors should also be accurate so that it can be used to generate actionable reports, serving as the foundation of predictive analysis.
“WSNs must be packaged with a material that is compatible with that of the pavement and can protect the internal circuits from thermal and mechanical damage without compromising on their performance capabilities. For example, the strain gauges of WSNs are often packaged with epoxy resin, as it is associated with a high-energy harvesting efficiency and can simultaneously protect the internal circuits of the WSN from high pressure and potential harm from aggregates within the pavement,” highlighted Benedette Cuffari, researcher and scientific writer at AZoNetwork.
Optimizing Node Layout and Configuration
A challenging aspect of planning a WSN installation is deciding on a node layout along the asphalt structure. A WSN layout should use the least amount of sensor nodes possible, while maintaining quality data collection and transmission. By minimizing the number of sensors nodes in the network, the WSN would be less costly to install and maintain.
Wireless sensor nodes have limited detection and connectivity ranges; therefore, it is important to incorporate a layout that addresses such limitations. Another factor in choosing a node layout is data transmission. Sensor nodes pass around and forward data to the sink node. Not all sensor nodes transmit data to the sink node. From a practical perspective, it wouldn’t make sense for a sensor node located very far away to directly send data to a sink node on the other end of the network.
Sensor nodes are usually installed in clusters, serving a specific part of the roadway or structure. Additionally, their coverage area can overlap. Multiple sink nodes can be present in a WSN, serving individual clusters of sensor nodes. There are several options for the configuration of node installations on roads. Nodes can be installed on the outer lanes of wide roads with alternating spacing, forming a triangular cluster (when installed on both sides of the outer lanes). On the other hand, narrow roads can easily be covered with a single line of sensor nodes.
“The challenge in designing the WSN lies in finding the minimum number of sensors that allows to maintain good data quality. An optimization problem therefore arises in which a limited number of elements must be associated with an infinite number of possible positions. Optimization can take place on the basis of certain parameters such as data quality, the maximum sensing coverage, the fault tolerance, the network connectivity and so on,” explained Alessandro Di Graziano, researcher from Department of Civil Engineering and Architecture, University of Catania.
Choosing a Reliable Power Supply
The “heart” of a WSN is the power supply; without reliable power the WSN would not function. A compromised power supply could cause the critical components to go down or in some cases the entire WSN. Nodes are low-power components that require small amounts of energy during application. The challenge in powering nodes is utilizing a power source that is maintenance-free and reliable for extended periods.
A leading solution for powering sensor nodes within a WSN is energy harvesting. This process involves converting vibrations from vehicles to electrical energy. A key component in energy harvesting is lead zirconate titanate (PZT). The material can generate electricity in response to mechanical stress, such as vibration or deformation.
In an asphalt pavement, PZT-based sensors can be embedded to convert the mechanical energy generated by the passing vehicles into electrical energy, which can then be used to power the WSN deployed in the structure. PZT-based sensors are installed in the middle or top layer of the asphalt pavement, where they can detect the vibrations caused by the vehicles passing over the pavement. The vibrations cause the PZT material to deform and generate an electric charge, which can be captured and stored in a capacitor or a rechargeable battery.
Sensor nodes used for asphalt cannot rely solely on batteries for power. This is because the sensors are buried in asphalt, making access difficult and costly for battery maintenance or changes. Batteries inside commercial sensors (that rely solely on batteries) must be replaced every four months or 1-2 years, depending on the type of battery. Using PZT technology enables the batteries to remain in a charged state for consistent power, resulting in a “self-powered” solution. The problem with using solar panels or wind energy to charge batteries powering nodes within the asphalt is underground deployment, which requires long and buried wiring connections. PZT does not have this requirement.
Not all components within a WSN are fit for energy harvesting via PZT. Solar energy can be used to power modems and other network components near nodes for remote data transmission. A battery stores solar energy for use at night or during low-light conditions. These components are located on the sides of roads and are protected by heavy-duty cabinets, such as stainless steel enclosures to withstand rugged elements.
Using different types of power supplies makes WSNs increasingly complex and adds to its long list of potential points of failures. This is because power supplies have different lifespans and are prone to degrading performance over a long period of time. Managing power supplies for WSN components requires monitoring healthy charge states and energy harvesting performance.
Challenge Accepted
With so many hurdles and challenges associated with deploying a WSN, why would roadway builders and operators consider implementing such daunting projects? WSNs can help increase the uptime of roadways and reduce maintenance costs through preventive measures. According to research, it is 6-10 times more costly to perform corrective or emergency maintenance on asphalt pavement, compared to implementing preventive maintenance.
Reducing corrective or emergency maintenance also has positive effects on cities and residents. Local businesses are usually caught off-guard and when road construction hits their area. In most cases, their only option to wait for the project to finish. Road repair projects can take months to years, depending on the size of the project.
“Public works projects can seriously disrupt business activity and construction mitigation is designed to help businesses through what is often a very difficult period,” said Bo McCready of the University of Wisconsin's Robert M. La Follette School of Public Affairs. By supporting preventive maintenance efforts, WSNs can help keep roadways open ensuring access to business establishments and public locations.