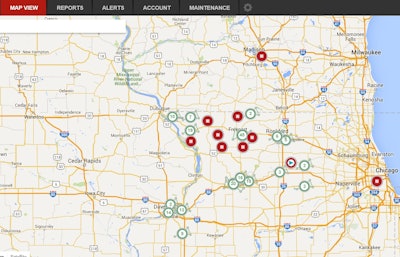
The transition that AT&T and Verizon have begun, to replace 2G cellular networks in the U.S. with mind-bogglingly faster 4G cells, looked like it was going to cost The Helm Group $35,000 to $40,000 or more. Greg Peet, president of Heavy Equipment Services Inc., the Freeport, IL,-based regional contractor’s equipment company, capitalized on what could have been a bad situation by upgrading telematics providers altogether, rather than investing in replacing the 190 2G telematics boxes (of 250 connected machines in the fleet) that will be obsolete by the end of 2017.
“One of the big issues for us with our previous provider was that they were unwilling to enable their application to accept standard data feeds [from telematics devices other than the ones they sell] using the AEMP (Association of Equipment Management Professionals’) telematics standard,” says Peet. “For our equipment that had Cat’s VisionLink system on it or Volvo’s Care Track system or Komatsu’s Komtrax, or whatever it might be — we wanted to be able to see the basics like machine location and hours in one application.”
Peet had talked with his first telematics vendor about implementing the standard from the start of their relationship. “I made the assumption that over time they would want to embrace it, but it never came to pass,” he says. “It really didn’t make all that much difference to us for quite a while. But as more and more equipment comes to us with telematics as part of their standard build, we would really like for the data to display in one application.”
The inability to integrate data streams from the OEM boxes in the same software as the rest of his fleet eventually convinced Peet not to upgrade the 2G devices supporting their existing telematics system.
Manage Data and Machines in One Place
Using original equipment telematics hardware is a lesson Peet learned early in the company’s telematics journey.
“We already had a handful of machines with OEM telematics devices when we jumped on the telematics bandwagon four years or so ago now,” he says. “And initially we installed third-party boxes on those machines as well.”
Use of the standard communications protocols for telematics data that AEMP and the Association of Equipment Manufacturers developed was pretty rare at the time. So installing a redundant device on a few machines seemed like a reasonable investment to simplify managing the company’s entire fleet.
“But over time, we got more machines that came with telematics boxes on them from the factory,” Peet says. As their number grew, the cost of installing redundant devices grew less reasonable. “You want to be able to see the data from them all in one place, and manage them all the same way.”
Peet had met representatives from telematics vendor TeMeDa and AT&T at AEMP meetings. TeMeDa and AT&T were working together to develop a heavy equipment system called Equipment and Machinery Solution (EAMS). They spent some time getting Peet’s perspective on reporting capabilities for the new system. The release of EAMS coincided with Peet’s vendor search, and he selected EAMS for The Helm Group’s new telematics platform.
“One of the attractive things for me is that they are using some of my input to help develop some of their reporting capabilities,” says Peet. “It’s still in the process of being built, but looks like it’s going to be very positive. We’re going to have a lot more analytics available in the new system.”
“The report that I’m most excited to see is actually similar to one that our old vendor built for us. I think it’s going to be called the Jobsite Utilization report,” he notes. “One of the things that was most helpful is it identified equipment that could or should be made available from one project to another.
"You can set this report's parameters over whatever job and period of time you desire, and it will tell you every machine that’s on the job and how many hours it worked during the period. You can input your rates for each piece of equipment, assuming you’re charging your equipment out at an internal rental rate, and the system will extrapolate that into an extended cost,” Peet explains.
For example, a project manager can pull up a jobsite and look at all the equipment expenses for the previous week. The report shows which machines worked, how many hours they ran, when they arrived on the site, when they left and what the costs were for the week.
One result is improved equipment utilization. “Superintendents would call and tell me they needed to rent a machine, and we’d walk through the utilization report,” says Peet. Using the report, they could see if the equipment was under-used machines on their own sites, and quickly toggle to a company-wide view to see if there were available machines on other jobsites. “It just made the transparency much greater. We improved our utilization and lowered our outside rental expense by exposing this data to everybody in the company.”
Peet hopes to eventually use this information to automate the billing process. “We’re working to integrate more of our telematics data into our ERP software. Instead of having to key in the hours off a foreman’s timesheet, we’re hoping to integrate the jobsite utilization information and have those hours drive intercompany equipment billing to the jobs,” he states.
Billing True Hours
The Helm Group’s foremen turn in daily timesheets that record crew time on the front and equipment time on the back. “We’re relying on them to tell us how many hours to bill the project for these given machines for this given day,” says Peet.
Telematics reporting of actual equipment hours uncovered discrepancies. “We were finding about a 20% to 25% shortfall in what we were being instructed to bill vs. the hours that were actually accruing on the equipment,” Peet comments.
“For several years, at the end of each month, we had to do what we call ‘truing up the hours’ or ‘truing up the rental billings.’ We’ll see that a particular excavator, for example, has been reportedly used for 100 hours last month, but the actual hours of use gauged by the telematics system is 119 hours. So we’ll go back and determine where that extra 19 hours likely occurred and generate a supplemental billing to the job,” Peet explains. “That’s a big process. It used to take one employee about 2.5 days at the end of every month.”
The Helm Group’s idling reduction policy intentionally eliminates any perceived subjectivity in equipment hours. Heavy Equipment Services bills operating divisions for every hour a machine runs, whether it’s at idle or under full load.
“Idling is a bad deal for equipment on a lot of different levels,” says Peet. “And one of the ways we try to curb it is to bill the job for it. That’s why it’s important for project managers to understand that they’re paying for all time the machine is running.”
Installation Advantages
Implementing the new EAMS system comes with several hardware advantages.
“One of the things that was attractive to me is that we aren't bound to using just one supplier’s telematics device,” says Peet. “Our provider has recommended Morey devices because they have the harness and connectors to hook up to the J1939 bus connection.” This is the standard that many vehicles’ controllers use to communicate engine and other systems’ data. “They’re able to put much of the data that comes out of the machine into our telematics data stream. It really cuts down on the installation cost, and you’re able to pick up a lot more machine operating data.”
Peet reserves judgment for a few years, but expects the hardware will also be more durable.
Peet also learned an important lesson about installations the first time through. “We did our own installations on our previous system, and we ended up finding a lot of SNAFUs that the vendor didn't tell us to watch out for. So we had to go back and redo a lot of our work,” he says. “We’re having TeMeDa take care of most of the installations on the new system. We wanted somebody else’s fingerprints to be on it, so they could control the consistency of the installations and if there was anything that needed to be corrected later they would be responsible to do so.”