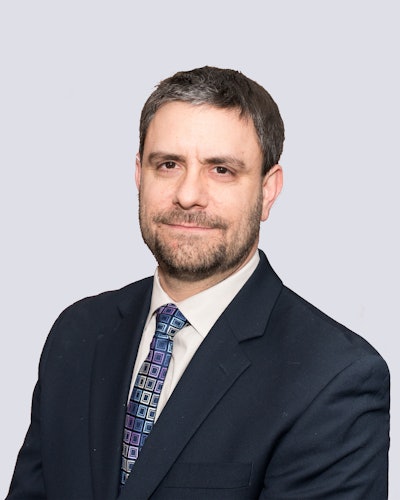
By Michael Bloom
Most contractors think of telematics exclusively as a tool to strengthen control over the movable assets in their fleet. Today’s advanced systems do that in dozens of ways, from pinpointing the real-time location of every vehicle and machine on a single dynamic map to electronically collecting engine hours, generating equipment utilization reports, issuing real-time alerts on equipment problems like blocked air filters, and much more. But the technology also can be used to improve the management of human assets – notably driver behavior.
Community Asphalt, a contractor with four asphalt plants and more than 450 on-highway and off-road assets servicing south Florida from Miami to Fort Myers, has been capitalizing on those capabilities since mid-2013. With relatively little effort, the company has successfully used its telematics system to curb speeding, idling and out-of-the-way driving.
“We reduced speeding alerts from 255 in the first month that we monitored to as few as 20 a month today, and we cut average idle time across our entire wheeled fleet as much as two-thirds simply by calling drivers when we see they are idling too long,” says Emmanuel Le Hardy, loss prevention manager for Community Asphalt’s parent company OHL USA. “The fuel savings from controlling idling alone paid for our telematics deployment.”
The firm has gone the extra telematics mile in other ways as well, including working with its telematics provider to customize reports for easier problem identification on jobsites. The upshot of all these efforts: increased safety and smoother operations as well as reduced fuel consumption.
Spotting fuel thieves
Community Asphalt turned to telematics in 2013 in the wake of a fuel theft investigation involving two of its dump truck drivers. Utilizing temporary GPS units as well as manual surveillance, Le Hardy determined that both drivers were regularly stopping at the same house and transferring fuel from their gas tanks to a temporary tank on site. Both were convicted, placed on probation, and ordered to pay restitution.
To enable rapid detection of similar abuses in the future, Le Hardy decided to install Navman Wireless’ OnlineAVL2 brand-agnostic telematics platform on the company’s 138 dump trucks, 15 lowboys, nine service trucks and three fuel trucks,. System functions such as real-time GPS tracking and replay-a-day capabilities would allow him to root out fuel thieves by monitoring and retracing each vehicle’s daily activity, complete with time stamps.
With permanent GPS tracking units in the vehicles and back-end telematics software in the office, Le Hardy decided to use the system to track other aspects of driver behavior as well. An informational meeting was held at each plant to inform workers that managers would be utilizing telematics alerts and reports to measure driving speeds, spot unnecessary idling, and uncover issues such as long-way-around driving and lengthy stops at area shopping malls that would impact productivity and fuel usage.
Drivers were put on notice that supervisors would be calling them when these behaviors were observed. Then they were asked for their cooperation and given one month to adjust to the change without punishment for violations.
Identifying speeders
Le Hardy’s first target was speeding. He configured the telematics system with different geofences and speed thresholds for different scenarios, including 15 mph in company plants, 25 mph inside quarries, 57 mph on an access road between the company’s storage yard and its Miami plant, and 72 mph on highways.
He also set up an alert system to notify supervisors when drivers exceed those thresholds and created a disciplinary policy establishing an escalating series of penalties for violations, from verbal to written warnings and finally to two- or three-day suspensions.
In June 2013, the grace-period month, Community Asphalt managers received 255 speeding alerts. That fell to 201 in July and plummeted to 36 in August. Since then the numbers have fluctuated from 20 to 90, almost always coming in on the lower end of the range. Map printouts from the telematics system show the location, time and speed of the violation, providing validation if further disciplinary action is required.
Reducing idling
Idling violations are handled differently. Le Hardy set up the telematics system to alert supervisors by email if a truck inside a company plant or storage yard doesn’t move more than 33 feet in 30 minutes. (“The only time we allow idling is if a truck is loaded with asphalt because we can’t risk turning it off and not having it start up again,” he notes.) Instead of disciplining drivers when they get back to base, however, company policy is to stop the problem immediately without disciplinary consequences.
“We instructed our supervisors to pick up the phone and call the guy who’s idling and tell him to turn off the truck. They’re not supposed to wait for a second or third email or the end of the shift. It’s better to stop the idling on the spot,” LeHardy says. “If a driver is waiting to get a load of milling or for any other reason, he has to turn his truck off.”
This simple strategy has slashed idling time across Community Asphalt’s wheeled fleet from a pre-telematics 30-35% average to just 8-12% today, adding up to considerable fuel savings across the 165 vehicles involved.
Enforcing driving routes
Other belt-tightening in the fuel budget is coming from both formal and informal monitoring of driving routes used in traveling between Community Asphalt plants and jobsites, again using telematics maps and geofencing functionality.
At one point, for example, supervisors noticed that workers were taking a dangerous route between Miami and a project in the Florida Keys that also took more drive time than other options. Le Hardy geofenced the offending highway and configured the telematics system to generate an alert to the company’s truck superintendent if a vehicle turns up on the road. Problem solved.
Customizing reports
As a power user of telematics technology, Le Hardy has also identified ways to tailor system reports to better meet Community Asphalt’s needs. At his request, Navman Wireless’ professional services team created a special report that is delivered to project managers every morning and customized to display information only for the jobsites for which they are responsible.
The report – a modified version of OnlineAVL2’s standard Site Report by Vehicle – allows project managers to quickly determine whether too few or too many trucks were assigned to a site, whether they all showed up to be sure that the site is not charged for missing vehicles, truck idle time as well as arrival and departure time, and other information that helpful in optimizing asset utilization.
Case in point: an airport paving project that was generating unusually high idling rates. Further investigation revealed that drivers had to wait to be escorted in and out of the airport. Superintendents then were able to address the problem directly.
From driver behavior modification to better jobsite controls, Community Asphalt’s experience illustrates a few of the ways that asphalt contractors can go beyond telematics basics like GPS mapping to improve safety, operations and the bottom line. The technology has more bells and whistles than your favorite electronic gadget if you’re willing to take advantage of them.
Michael Bloom is a director, marketing and product management at Navman Wireless (navmanwireless.com), a provider of GPS-based fleet optimization systems and services that enable companies to monitor, measure and improve fleet-related costs and efficiencies.