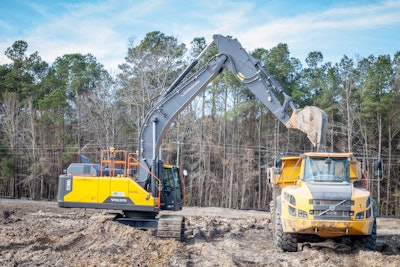
Charleston, SC-based Landmark Construction is one of the leading contractors in the Southeast U.S., with an emphasis on industrial, concrete, site work and utility contracting. It ranks in ENR’s top 10 for the region, and employs approximately 400. “We were at 45 people eight years ago,” recalls Mike Marshall, survey superintendent. “A lot of [the growth] has to do with technology.”
The success of this family-owned business, started in 1965 by Fredrick Mixson and his wife Ann, is partially due to its willingness to embrace the state of the art. Landmark Construction uses GPS and 3D modeling technology during each project; its project superintendents and foremen are experienced in their use and implementation. As a result, the company cuts costs, accelerates project schedules, improves accuracy and delivers a higher quality project for its clients.
The company has over a decade of experience with 3D modeling and GPS grade control, with all modeling done in house. “We typically run Trimble products,” says Marshall. This includes machine control systems on dozers, excavators and motor graders, as well as rovers used by field engineers, foremen and supervisors.
The investment provides measurable ROI. “Anything in the world of 3D technology pays for itself pretty fast on all of the machines,” says Marshall. “Those systems pay for themselves in the first two years. The technology is good for six to eight years before it renders itself obsolete in need of an upgrade. So, you pay for it for the first couple years, but then you get the benefit of it for the next six.”
Maximize Earthmoving Efficiency
Earthmoving efficiency is critical to the success of Landmark Construction. “Nearly half our company is involved in earthmoving operations,” says Marshall.
Currently, every dozer in its almost 30-unit fleet is equipped with 3D grade control. “The worst scenario we can get into as a company is when we are moving material from our excavation to fill and we don’t have a good grade control system in that fill,” says Marshall. “So, we always have a dozer running there with 3D.”
Currently every dozer in its almost 30 unit fleet is equipped with 3D grade control.
The increased independence has earned favorable acceptance. “The operators in an excavator love it because they don’t have that extra bulldozer there keeping grade for them,” says Marshall. “The key here is eliminating the extra cost of operation with the dozer/operator.”
Earthworks Automates Process
Last year, Landmark Construction purchased a Trimble Earthworks Grade Control Platform for Excavators system that allows the excavator to reach grade semi-automatically. When in automatic mode, the user controls the stick and Trimble Earthworks controls the boom and bucket to stay on grade.
“We have one Trimble Earthworks excavator at the moment,” says Marshall. “We’ve had it close to a year. It is a very new technology compared to the other systems that we have been running.”
Trimble Introduces the Next Generation of Grade Control for Excavators and Dozers
The biggest advantage to the system has been how user friendly it is for the operators since it draws on tablet technology. “Our company typically has iPads and some Android devices, so employees are familiar with that operating system,” says Marshall. “When they get in [the cab], it is pretty easy for them to log on and pretty much go straight to work.
“We have four operators run it. All four of them had about 30 minutes of training overview,” he comments. “The automatic part is so intuitive.”
[VIDEO] New Trimble Earthworks Brings Auto Grade Control to Excavators
A major advantage of the Trimble Earthworks with automatics is how it prevents operators from over-digging. “You cannot actually go below grade, which is really significant when it comes to dressing up the slopes,” Marshall points out.
Landmark Construction has over a decade of experience with 3D modeling and GPS grade control. This includes machine control systems on dozers, excavators and motor graders as well as rovers.
Take earthworks on a pond, for example. “When you are digging a pond, you dig from the slopes to the middle and you create this bench that your machine sits on,” Marshall describes. “When you are loading that bucket, 50% of the time the bucket is underneath the tracks. Even if you have 3D with the screen, you still have to focus on the screen and leave extra material. And you have to work your bench quite a bit farther back so you can see what you are doing.”
The semi-automatic feature no longer requires the operator to focus as much attention to the screen. “With the automatics, you can carry the grade 100% of the time underneath the machine where the operator cannot see,” says Marshall. “Now when he is pulling the bucket to him, he can see where it is being loaded and when he picks it up, he knows he is on grade that entire load because he is in automatic.
“That almost doubles his production,” he states. “That caused us to have to add trucks on the haul. The operator normally had to have two or three trucks; we had to have four because he is moving that much faster.” That was with a 4-yd. bucket on a Volvo 360. “Now the operators want a 5- or a 6-yd. bucket.”
Increase Utility Production
Earthmoving is not the only application that has benefited from an investment in 3D excavator technology.
“We have been very successful on some deep sewer work where we use 3D,” says Marshall. “The trick to deep sewer is when you pull the trench box. It is big and a lot of times it is double stacked. If that trench is not perfect, you cannot pull it. The operator tells me when he is digging with that 3D system, it is very easy for him to dig a very straight trench so he can pull that box in one shot. That is the time saver in sewer with 3D — moving that box.”
The result is increased productivity. “We were getting an extra two to three joints a day, which added up to a significant amount of money,” Marshall recalls. “It is not so much digging to grade at the bottom as it is moving that trench box one time straight. It also helps with getting to grade because we don’t have to put people in the trench.
“The safety factor is very big in utility work,” he continues. “You don’t have someone down in that hole verifying the elevation until you have completed the dig and the trench box is actually moved. Everything all happens in one big step. You basically backfill where you are at, dig and then pull that trench box and finish digging to grade before you ever put a man down there.”
Flexibility is a Key Requirement
“We do a lot of things with excavators,” says Marshall. “We just finished doing three miles of electrical conduit last month on a project and we rented a small excavator because most of our fleet is very big. We rented a 200 Series zero tailswing machine and basically installed 3D on it temporarily. We did what we call a soft install.”
The results on the project dramatically outpaced expectations. “The owners on that project couldn’t believe what we were doing,” says Marshall. “We were doing 600 to 800 ft. a day and the most they had ever seen was 300 to 400 ft. a day. They thought we were going to be there for six months and we were there for two and a half.”
To accomplish this type of success, equipment must be adaptable. “I tend to move things around a lot,” says Marshall. As newer technology is introduced, the existing GPS technology can be shifted to where it can best be utilized. “Everything is interchangeable in this world. So, if I want... I can take it out of the excavator and put it over to a motor grader; maybe it requires a couple of different sensors. My No. 1 goal is to get 100% utilization on every component.”
The technology needs to be mobile since the machines in the fleet are also turned on a regular basis. “Most of the dozers that we have been getting lately are integrated machines right at the factory, so that works out pretty good,” says Marshall. “Typically, we will do a two-year lease on a machine, sometimes four. There is nothing in our track fleet that is over four years old.”
Even though Landmark Construction tries to use the most up-to-date technology available, it also carefully tracks macro trends. One of these is the pending availability of more satellites with the European Union’s Galileo system coming online. This has caused a brief halt in the acquisition of newer grade control products.
“Most of the receivers that we have right now are not capable of picking up those satellites,” says Marshall. “Anything we purchase moving forward, we are going to want to make sure it has that capability. Every technology evolves probably in the eight- to 10-year range. I feel we are in that cycle. Moving forward, everything that we purchase will be Trimble Earthworks.”