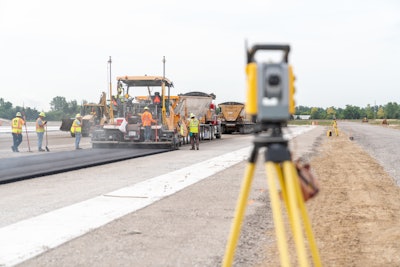
Flint, Mich.-based Ajax Paving handles both government highway and demanding private asphalt and concrete paving duties from its headquarters and asphalt jobs from a subsidiary in Fort Myers, Fla.
The company employs 500, and operates aggregates and aggregate, concrete and asphalt mixes in Michigan and aggregates and asphalt plants in Florida. Ajax Paving has been involved in marquee projects, ranging from the repair of the Sanibel Causeway following Hurricane Ian, reconstruction of North Port, Fla. roads to pass the coffee cup challenge, the I-275 near Detroit and the Florida I-75 Mega Project. Ajax Paving has been named a 2021 Best Contractor to Work For by ForConstructionPros.com. The company has taken a leadership position on environmental stewardship, partnering with Road Forward, the National Asphalt Pavement Association (NAPA) net zero carbon emission asphalt initiative.
But the company also lead as an early adopter of 3D paving technology, and has since built a program deploying it strategically over a period of what had been, at the time of our December 2022 debriefing with Ajax Paving 3D Paving Manager Jeff Robinson, more than nine years.
3D paving differs from 2D screed control in that it does not just control the elevation of the screed, but can accomplish variable depth paving, quickly changing the depth of the pavement and even the cross slope if needed, as is the case in a super-elevated curve. In this environment, an array of total stations locks onto receivers on pavers, rollers and milling machines through a prism mounted on each machine. 3D paving controls on each machine contain a digital model of the job, enabling the equipment to deliver on the model automatically including slope, crossfall and even compaction density.
This enables a paving contractor to increase quality and increase margin while shrinking the budget, timeline and employee hours.
Some of the benefits come from automating the interaction between the flow of materials to the site, the paver and the compactor. By getting all of these steps to dovetail, the paving crew can achieve a consistent rate of production which in turn results in smoother pavement with less rework and grinding.
“You want to avoid stops as much as possible and changing speeds is nearly always better than stopping,” Trimble General Manager of Civil and Specialty Solutions Kevin Garcia told ForConstructionPros, describing the process for asphalt paving. “The screed floats but a stop lets it sink, driving out the air voids with the weight of the screed. Every time you stop there is a discernable bump in the road. Oftentimes, you will have to come back and grind that bump—bring out the diamond grinder and grind a high spot, particularly if it is next to a low spot. These are incurred costs that you may not have budgeted for and may cause you to exceed your buffer.”
The asphalt compactor’s job would seem simpler than that of the paver, but also benefits from 3D technology to monitor the number of passes, degree of compaction and temperature of the asphalt. Too little compaction and the asphalt will contain air pockets, which lead to premature erosion. Too much compaction, as can happen when an operator loses track of the number of passes, they have completed and completes more than is necessary in order to be thorough, and they can crush and break down the aggregate in the asphalt. Overcompaction of asphalt also, according to Garcia, can have a knock-on effect where the paver pulls further and further ahead of the compactor, which must do its job when asphalt is at the correct temperature. This causes the paver to stop, which again results in uneven spots that must be milled out.
In concrete, 3D paving leaves very little finishing work to be done. 3D concrete technology can typically control the pan of the machine to a certain elevation and steer the machine to align with the model. This engineers out the string, which is a barrier to operating equipment on the site, and yields results that can help meet conditions required for a smoothness bonus. It is still important for contractors to maintain a uniform delivery schedule for materials with consistent properties from one batch to the next to ensure continuous flow and results. Consistent batch to batch properties is important. State department of transportation (DOT) guidance says paver vibrators should be operated between 5,000-8,000 rpm and should run without stops.
Adopting 3D Paving Technology
“Nine years ago, maybe even 10 years ago, we started out in the machine control and paving world,” Robinson said. “We weren’t sure which way we were going to go between Trimble, Topcon or Leica. We did a demo between the systems, and at the time, concrete paving was not even something we were doing yet. We weren’t even thinking about it. We were doing asphalt. But then Trimble came to us and asked what we would think about doing some concrete paving—they were doing a beta test. I talked everybody into it at our company and told them we would learn a lot.”
Trimble came on site with Ajax Paving for base testing of the concrete paving and according to Robinson, “Day One, we put stringline up with engineers. On the second day, I didn’t put the stringline up and just told them if it worked on Day One, it better work on Day Two. From that day on, we have not put stringline up for a concrete paver. The next year, we went from one machine to 14 machines.
Ajax Paving does not use 3D asphalt paving much on highway projects where they are paid by the ton. On these projects, the asphalt is trimmed to grade.
“Most of it is airports, test tracks, NASCAR and things like that,” Robinson said. “It is more specialty things we do with 3D asphalt.”
The process for these demanding projects has changed radically thanks to 3D technology.
“Back in the day, even before me, when you did an airport runway job, we would put stringline up and trim to fine grade,” Robinson said. "Asphalt would come in and paint it black. Concrete would come in and put their own stringline in and there would be conflicts because the grade was too high or too low. Now we don’t have that. Everybody just kind of comes together in harmony.”
Airport runways are mission critical projects that demand the smoothness and consistency 3D paving can deliver.Trimble/Ajax Paving
Flow of Data to Back Office
Data flow should be a two-way street in construction, and just as project requirements go from the field to the back office, data on project and equipment performance can return from the field to drive functions like work in progress reporting, application for payment, quality management, corporate performance management and more.
Ajax Paving relies on the Trimble SCS900 Site Controller software. Using this application, an engineer in the field can quantify progress and manage machine operations. Performance data and as-built data are stored on the device and can be extracted as a .TXT or .DXF file.
“We are starting, with the 3D paving equipment, to get some of the quantities and other data off of it,” Robinson said. “The concrete paving equipment lets you download the as-built data, and it tells you the elevations and smoothness so you can calculate international roughness index (IRI). We use that quite a bit. We are starting to do a lot more mapping with this data, mapping for quantities. And we are trying to figure out with Trimble how to drive value for this for paving. It is a great tool for the earthworks and the dirt guys. We are still working on it to make it better for the paving world. The mapping part of it works—you can see where you paved and get some rough quantities. I am going to be seeing if we can correlate the paving with the earthworks data to correlate our trimming with our paving together.”
Trimble technology can also operate a multiple-machine production line including pavers and compactors, for optimal results.
“We know the Trimble technology will correlate machines together,” Robinson said. “I have not thought about machines talking, there may be some value to it. We have tried tracking technologies on our trucks, but because our batch plants are on site, we don’t have very far to move the material.”
Finding ROI
The Ajax Paving 3D program has taken some capital and effort, and it has been up to Robinson to ensure the juice is worth the squeeze.
“It has been profitable,” Robinson said. “Jobs are built faster and quicker with less people. I started off with this from nothing, and now, we are one of the best in the nation with 3D concrete paving and asphalt paving. It has been challenging at moments, but we realize a profit because jobs are built faster, quicker, with fewer people. I started out from this with nothing—and it made Ajax Paving what it is—one of the best with 3D concrete and asphalt paving.”
This efficiency can help Ajax Paving win business, as can the simple fact that they are using 3D paving.
“The market is competitive, but material prices are the same for everyone,” Robinson said. “Controlling your yield and getting off the job quicker do help you win business. We are seeing 3D paving required in some RFPs from the big automotive OEMs like Ford, GM, Chrysler and Toyota. We do a lot of the test facilities for the major manufacturers—skid tests, straightaways. There are flatness specifications each manufacturer wants to achieve.”
The Ajax 3D Arsenal
Across its two locations, Ajax Paving runs an armada or 3D printers to meet owner requirements.
The company runs a fleet of 24 Gomaco concrete pavers in various sizes, and one Gunner paver.
All of Ajax Paving’s asphalt pavers are CAT AP1055s, which are integrated with Cat Accugrade GPS. Asphalt paving machines are replaced or traded every three years, according to Robinson.
Using this complement of equipment, Ajax Paving can achieve accuracy within a hundredth of an inch for airport projects and has achieved accuracy of about 1 millimeter to meet one test track project specification.
But success is not purchased from the dealer—there are still some skills and good decision making required to achieve optimal results.
Trimble/Ajax Paving
Duplicating Ajax’s Results
“You have to make sure on an asphalt job that you are using a high-density screed to make sure pavement is 92 percent compacted,” Robinson said. “If it is less compacted, you have rollers trying to achieve accuracy. With concrete we easily achieve that tolerance because it is a one lift application. But it goes both ways. With an airport project, most runways are concrete and asphalt under that. For automotive pavement, it is most often asphalt. But for concrete, we have done alternative bids internally to determine what is the best strategy to get to the desired outcome.
But success has not come overnight for Ajax Paving, and Robinson advises being in 3D paving for the long haul.
“You want to be dedicated, Robinson said. “Have an individual to champion it. Build a staff. Having great owners that believe technology has also been a success factor for us. We started this endeavor and spent millions and millions of dollars, and they never told us no.”