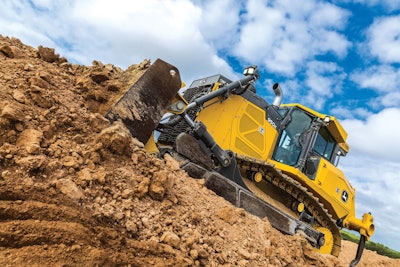
Not only is proper grading on construction jobsites crucial to a project's long-term success, but improper grading can have significant ramifications on a job’s timelines and costs. Such is the observation of Matt Goedert, John Deere solutions marketing manager, as well as other industry experts in addressing the importance of proper grading.
“There are many reasons for this, as it can have a great effect on the jobsite’s timeline, efficiency, machine operating costs, jobsite conditions and ultimately the satisfaction of the end customer,” Goedert said.
As a construction site task that disturbs the ground, the value that proper grading brings to a project cannot be underestimated. It is the function of a construction site project that establishes the permitted height and depth of swales, cuts and fills, as well as enabling proper drainage.
Proper Grading Techniques Create Property Aesthetics
Proper grading is a driving factor in mitigating environmental issues as they relate to erosion control and stormwater runoff, and helps contractors fulfill the requirements of a National Pollutant Discharge Elimination System (NPDES) plan and a Stormwater Pollution Prevention Plan (SWPPP). In addition to adhering to nationally-established standards, grading also must be completed in compliance with local zoning and other regulatory restrictions and requirements. During the construction phase, sediment control is a consideration when engaged in grading, with care given to pollutant runoff of trash, debris and solids. The impact of various weather conditions is one of the factors in achieving proper grading, Goedert pointed out.
“Proper grading to ensure water sheds off the jobsite and away from working areas will help the jobsite keep moving after inclement weather is experienced,” he added. “Without keeping drainage in mind throughout the jobsite’s construction, days and even weeks can be lost in the schedule.”
Scott Hagemann, Caterpillar senior market professional, agreed that controlling water without losing material is a significant driving factor in proper grading.
“For example, on a gravel road, you need to have the water flow off the road, but if the slope is too much, the gravel will also flow into the ditch,” he said. “On a concrete or asphalt surface, you need to grade so that the water flows to the designed areas.”
Operating costs of equipment can also be affected by weather and other factors, said Goedert.
“When grading with a dozer for example, a significant portion of the operating cost is tied to the undercarriage,” said Goedert.
He added that when grading, a good equipment operator will have as a primary consideration a purpose for every move made with the dozer as to keep the number of passes needed to a minimum. Being conscious of how operating characteristics, such as travel speeds, working on slopes and load management affect undercarriage wear also is important, Goedert said.
“At the end of the day, the grade of the finished product has to be correct, both in elevation and slopes,” he added. “For most jobsites, the tolerance of these specs is defined by the engineering firm who created the design. The grade is often inspected as the jobsite progresses to ensure it is within design specifications. Ensuring the grade meets target specification can save large amounts of time in costly rework.”
Using the Correct Equipment for the Task
Safety is paramount during the grading procedure, said Hagemann.
He pointed out that interstate speed limits are based on the road slopes in curves and for on- and off-ramps, so if the job is not done properly, it compromises safety.
“Also, if you have a haul road to maintain, you don’t want excess cross slope due to material that would fall off the haul truck,” he added.
In grading, there are standard do's and don’ts that contractors should consider in ensuring its success.
A major consideration when grading is to use the correct equipment for the job and how it was designed, points out Hagemann.
Goedert concurred.
“A critical part of ensuring proper grading is selecting the right tool for the job,” noted Goedert. “When looking to purchase or rent a piece of equipment, it’s important to consider the machine’s versatility to ensure high utilization and return on investment.”
He cited the John Deere 950K PAT dozer with SmartGrade as a piece of equipment designed for versatility.
Given that it is equipped with a six-way power/angle/tilt (PAT) blade, the dozer is designed to enable the operator to execute significant levels of dozing and finish grading, doing so without the use of several other machines.
“This machine fits into so many different segments, providing the production capability of a large dozer with the versatility of a small finish dozer,” Goedert points out. “The large PAT blade provides the ability to control and windrow material allowing the operator to balance out cuts and fills efficiently.”
The versatility enables its use in jobs from fine grading and site development to large road-building tasks.
Operator and Technology Considerations
The equipment operator and the technology used also plays a large part in meeting the grade tolerances outlined for the job, Goedert pointed out. Technology used on the equipment offers the equipment operator the ability to leverage the benefits of precision, safety, and efficiencies in time and costs.
SmartGrade aims to improve grade accuracies and reduce the number of passes it takes to achieve target grade, said Goedert. SmartGrade provides 3D grade control without external masts or cables. Auto SmartGrade automatically adjusts the blade when encountering heavy loads.
“There are many other tools in the operator’s toolbox to help them achieve proper grade,” Goedert said. “Features such as slope control allow operators to grade consistent slopes to meet specification and ensure proper drainage on the jobsite.”
Many John Deere products also offer 2D laser solutions which allows the system to also control the blade/bucket tooth to a desired elevation. Often working in the background is technology that may be less complex but adds a lot of benefit, such as John Deere EZ Grade technology, said Goedert.
“EZ Grade is designed to sense changes in the machine’s pitch and automatically adjusts the blade’s position to maintain smooth grades, helping operators achieve phenomenal grades with lower effort and reduced fatigue,” Goedert points out.
Operating characteristics can have a significant impact on undercarriage life, which in turn affects operating costs, he added.
Some operating habits to be conscious of that may cause premature undercarriage wear include always turning one direction, continually working slopes in the same direction, spinning the tracks, and continuous abrupt turns or counter-rotating, which increases stresses in undercarriage components, Goedert noted.
“In general, high speed shortens undercarriage life, especially in reverse,” he said. “Since the amount of wear correlates with distance traveled, reducing the number of passes needed to complete a job has multiple benefits. All these characteristics are items to look at when training operators.”
In addressing the do's and don’ts associated with proper grading, Rafal Bukowski, product specialist for HST dozers for Komatsu, noted that “a big thing is to think ahead of the jobsite that you're about to get onto."
“Understand the terrain, understand where you have to move dirt, and where you have to take dirt from to constantly have material in front of your blade,” he added. “This will essentially save you time, money and increase your productivity and efficiency.”
Komatsu has developed and is reinforcing the iMC 2.0 proactive dozing ‘smart’ technology.
“This essentially allows the machine to think ahead as it tracks across the terrain,” Bukowski said. “It maps it and creates a temporary surface. This allows the machine to plan for its next pass, allowing it to grab as much dirt and position it into most spots – essentially taking dirt from high spots and putting in the low spots.”
A significant factor in grading is for the equipment operator to always obtain a surface that is not only smooth, but also drains properly, said Bukowski.
“Understanding the terrain and how you essentially want the terrain to look when you're finished will allow you to make fewer passes, create less wear on the machine and save time and money,” he added.
Keeping Safety a Top Priority
Another key factor is to always maintain awareness on a swivel, Bukowski noted.
Safety is the No. 1 priority for a jobsite. Bukowski pointed out that there are multiple people working on jobsites and a many potential risks involved.
“If we can minimize the amount of people that are on the ground, essentially you're practicing safe workspace conditions,” he said of the use of ‘intelligent’ equipment.
As such, automatics allows the operator to “keep their head on the swivel to understand who's around the machine and create eye contact whenever there's somebody at the jobsite,” Bukowski noted, adding that by doing so, “we are essentially eliminating workers being on the ground checking grade to place some stakes, since the machine does that for you with high accuracy.”
Proper Inspection and Maintenance
In terms of what should be avoided on a grading project, Bukowski advised against overloading the blade.
“Many inexperienced operators will start the machine up and load up the blade with as much material as they possibly can,” he said. “But that tends to bog the machine down, creating divots and ruffles.
“Essentially you want to have a smooth transition when starting out and creating a consistency, loading up as needed. That minimizes the amount of time that you need to go over the material multiple times – smooth transitions from high spots to low spots.”
Few factors can hold a project up like down time as a byproduct of improper maintenance.
“Ensuring that machine inspection and daily maintenance occurs greatly effects the machine’s performance, longevity, operating cost and even operator efficiency,” noted Goedert.
Proper inspection and maintenance includes performing daily walkarounds, which are essential to ensure the machine meets its productivity potential and to minimize potential down time.
“When examining your machine, it’s crucial to get into not only a regular routine but complete the checks in the same order,” said Goedert. “Every time you do an inspection, start in the same spot, and complete your inspections around the machine ending where you started. This routine makes it easier to spot what is normal vs. abnormal and makes sure no checks get missed.
“When performing your walkaround, visually inspect the machine’s appearance and look for damage, check fluid levels, look for leaks, and take a close look at wear items that could prevent the machine from efficiently doing its job. Spotting potential problems early is beneficial on multiple fronts.”
On every piece of equipment, routine greasing offers a lot of benefits, noted Goedert.
“Not only does proper grease improve component life, but it will have a large impact to the performance and accuracy of the machine,” he said. “The tighter we can keep the machine’s joints, the more precise the operator will be able to control the machine.”
This improves accuracy both with and without a grade control system installed, he added.
“Checking for leaks at the end of the day can be a good way to prevent a mess from occurring overnight and reduces the environmental impact and can be beneficial while all the joints are free to ensure proper lubrication,” said Goedert.
Undercarriage is an area where owners can accrue significant costs. It is important to perform proper maintenance such as checking track tension to optimize the life of the system, Goedert said.
“A dealer can help with maintenance or – when purchasing a new machine – with selecting the right undercarriage solution for the intended application,” he said, adding John Deere’s Maximum Life undercarriage is designed to offer twice the life of conventional systems.
Increasing undercarriage life lowers operating costs.
Goedert noted that the three ways in which owners and operators can ensure they get the most out of their undercarriage include:
- Track tension: Maintaining proper track tension is an important controllable factor in undercarriage life. A tight track greatly increases component stresses and increases wear rates. Tracks should be adjusted to the proper amount of sag as working conditions change, possibly daily. Increased soil moisture, for example, can cause packing in the sprockets and a tighter track. A track tension decal is located inside the service door of all John Deere dozers displaying the track sag specifications and the process to check it.
- Keeping the undercarriage clean. If working in a material that hardens as it dries out or freezes, cleaning the undercarriage daily will prevent the increased wear that occurs with the additional contact points.
- Daily visual inspections of the entire undercarriage are helpful to identify any unusual component issues or unusual wear indicators. Undercarriage wear inspections on a regular interval allow planning for repair or replacement and are proactive actions that lead to better control of the overall costs of maintenance.
To increase the likelihood of proper maintenance, John Deere has designed its equipment to make maintenance as easy as possible, noted Goedert.
“On every piece of John Deere equipment, a periodic maintenance decal is located inside the service compartment which includes key maintenance information such as recommended oil types, refill capacities, and color-coded maintenance intervals,” he said. “When designing equipment, time is spent grouping filters and fill locations together and making them accessible from ground level as much as possible. The easier it is to perform maintenance the more likely it is to get completed properly.”
“A key factor in maintaining equipment is essentially the less you use it, the better condition it will be in,” said Bukowski. “It seems common sense. But with automatics, you are you're essentially being 60 percent more productive than previous generations of automatics – using machines 60 percent less of the time and doing the same amount of work. With that, you get higher productivity, higher efficiency, and with less fuel less wear and tear on the machine.”
Bukowski also advises the operator to minimize third gear reverse travel as much as possible to keep the undercarriage lasting longer.
Make sure the machine is calibrated as correctly as possible, he added.
“With that calibration, you want to make sure that your blade tips are measured and inputted correctly into the machine,” Bukowski said.
Proper tuning also enables the operator to adjust the blade response from normal pass to fine, depending on the type of material with which the operator is working, he added.
“You want to create a smooth surface with the contour of the final grade in mind,” Bukowski points out. “But also, at the end of the day, machine operators will seal the job site, meaning they'll back drag materials to prevent water pools from building up. This creates less time for when it rains for material to dry up and they can get back onto the job site.”
“Machine wear is a natural outcome of machines and needs to be adjusted as it happens,” he added. “Some adjustments need to take place to tighten the slop in the machine. Some parts are not designed to be adjusted; they need to be replaced. Regular maintenance of changing oil, filters and greasing is required to get the most out of your equipment.”