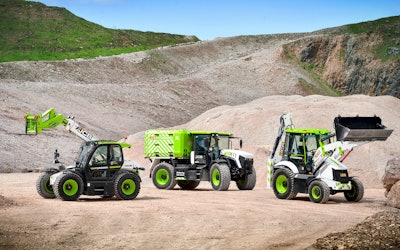
One of the hottest online topics lately regarding the construction industry is whether electric excavators are worth the time, money and commitment to change. Battery charging times may slow down a day's work, some argue. Ohers proclaim that a small electric excavator would not run for eight continuous hours on a jobsite anyway, as a construction project typically requires multiple pieces of equipment for different parts of the work. For example, as operators run dozers or wheel loaders, their small electric excavator battery packs could charge. Despite wide-ranging opinions, more manufacturers are focused on achieving two primary goals as they release new electric excavators: sustainability and fuel efficiency. And whether they're loved or hated by the industry, excavator engineering and product development, which currently prioritize electric and alternative fuels, is progressing rapidly on the road toward drastically lowered emissions.
Full Steam Ahead Toward a Hydrogen Revolution
Although JCB produces roughly 400 diesel engines every day for its agricultural and construction machinery, the company is currently considering alternative ways to power its machines.
After all, governments around the world are striving to end the usage of diesel and gas in passenger cars, along with light goods vehicles. However, JCB has encountered one significant issue: batteries aren’t usually a viable power option for the agricultural and construction industries, as heavy machinery requires massive batteries. Not to mention, the batteries wouldn’t be charged in an easy manner, as the machines are often used in remote areas.
With zero-emission technology as its ultimate goal, JCB doesn’t provide hybrid-diesel electric technology as a solution either. Nonetheless, in July 2020, JCB engineers began to design an engine for a backhoe that runs completely on hydrogen. Six months later, the first working prototype was tested, as the engineers successfully developed a high-performance, purpose-engineered, zero-carbon dioxide hydrogen fuel engine from the ground up.
“Hydrogen engines solve all of the problems that are associated with battery charging on busy, remote sites, as OEMs work on the internal combustion principle,” said Chris Giorgianni, vice president of government and defense, product and marketing, JCB. “They’ll feel familiar to anyone who is used to diesel or gas engines.”
Of equal importance, the costs of using hydrogen-powered excavators are roughly the same as utilizing excavators that are powered by traditional engines, which run on fossil fuels. Furthermore, unlike batteries, hydrogen engines aren’t inflationary. And, above all else, hydrogen engines don’t release any carbon dioxide into the atmosphere, as they’re completely carbon neutral.
“Now that hydrogen-powered excavators are here and proven, global governments need to be encouraged to adopt hydrogen engines and incentivize investment in hydrogen energy infrastructure,” Giorgianni emphasized. “While the benefits of hydrogen power are hopefully clear for everyone to see, it is still a relatively new technology. So, it is crucial that we start to take the lead in getting the message out.”
To help ensure that hydrogen power begins to be viewed as a genuinely viable alternative to electric and battery-powered machinery within the construction industry, JCB is investing $130 million to create super-efficient hydrogen engines for a wide array of machines—from backhoe loaders and telescopic handlers, to larger, heavier equipment.
In addition, the company is striving to offer its first hydrogen-powered excavators to customers as soon as possible.
“This commitment reinforces our conviction—as a company—that hydrogen power will be a key part of the solution, in response to climate change’s ongoing threat,” said Giorgianni. “As a result, JCB is looking forward to being firmly at the forefront of the hydrogen revolution.”
Maintenance-Free Electric Excavators Quieter, Cheaper
On the other hand, KATO-CES has two models of battery-electric mini-excavators: the 9VXB, which has a 5-foot, 2-inch digging depth, along with a bucket force of 2,360 pounds, and the 17VXB, which has a 7-foot digging depth, as well as a bucket force of 3,687 pounds. Since they each utilize a standard hydraulic system, users can run the same attachments with them as the diesel versions that the company has previously released.
“There is definitely a growing demand and a market for these mini-excavators,” said Bart DeHaven, director of sales, North America, KATO-CES. “The electric units are a little heavier than the diesel units, but they still have the same dig depth. The only drawback is run times, as the diesel mini-excavators can be filled at any time, yet the battery-electric mini-excavators need to be charged for eight to 12 hours to ensure they’ll run for eight hours.”
Additionally, the battery-electric mini-excavators release fewer emissions, are less noisy and have less vibrations than diesel mini-excavators, thereby improving operators’ comfort, while also reducing their fatigue. Completely maintenance-free, the mini-excavators’ lithium-ion batteries and electric motors have lifespans that are just as long as a diesel engine’s lifetime, if not longer.
“Battery-electric mini-excavators do have higher purchase prices than their diesel equivalents, but the total cost of ownership should be considered when evaluating them too though,” DeHaven added. “This total cost of ownership includes the fuel savings and extended component life of not having an engine, which decreases users’ overall maintenance costs as well.”
Zero Emissions and High Performance: Electric Excavators' Sweet Spots
Focused on minimizing its environmental impacts, while also helping its customers achieve the same goals, Bobcat Company is currently leveraging technology to become more productive and utilize resources more efficiently. As an example, the company is now using alternative-energy products that aren’t only environmentally conscious, but also ensure customers can continue their business operations as government mandates are steadily established, regarding zero emissions and clean energy.
So far, the company has advanced its commitment to environmental sustainability through the launch of the T7X, which is the world’s first-ever all-electric compact track loader. And it’s also producing a range of battery-electric excavators, as well as a variety of electric products that offer users viable alternatives to diesel-powered equipment.
“While significantly reducing their carbon footprints and producing much less noise than diesel-powered offerings, the battery-electric excavators will also expand users’ jobsite versatility,” said Joel Honeyman, vice president of global innovation, Bobcat Company. “Producing no emissions, the battery-electric excavators can tackle tough jobs—outdoors and indoors—as they also require less maintenance than their diesel counterparts.”
During bauma 2022, Bobcat Company revealed its latest electric excavator, the E19e compact excavator, which joins the E10e and the E32e as the product lineup’s third member. Each of the battery-electric excavators have compact footprints, quiet operations and zero emissions. In addition, their electrical motors deliver full torque, regardless of rpm, leading to high productivity, on-demand, multifunctioning performance (without any noticeable decline in power) and smooth hydraulic control.
Providing users a run time of roughly four hours of continuous operation on its lithium-ion battery pack, each of the battery-electric excavators can be fully recharged overnight. The E10e and the E19e have standard 120-volt outlets, whereas the E32e has a 240-volt outlet.
“Although applications vary, each of the excavators’ charges can support common, daily work operations and a full day of operation during intermittent use or a typical contractor workday,” said Mike Wetzel, director of product management, excavators, Bobcat Company.
Furthermore, the battery-electric excavators support environmentally sensitive worksites, while also enabling users to operate indoors—areas in which diesel exhaust is always restricted. And, at the same time, they provide significantly lower noise levels and vibrations than diesel-powered excavators, leading to an improvement in jobsite communication, as they can also be used in sound-sensitive areas.
“With the introduction of our all-electric compact track loader, the Bobcat T7X, as well as our battery-electric excavator lineup, which is, again, comprised of the E10e, E19e and E32e, we’re reaffirming our commitment to offering more environmentally-sustainable products,” Honeyman said. “And we’re doing so without sacrificing performance.”
He added, “We have many customers who have their own Environmental, Social and Governance (ESG) goals, and our battery-electric excavators support environmentally conscious customers, while still delivering diesel-equivalent machines’ performance and power too.”
Emissions Reduction Goals Key to Product Development and Engineering
Earlier this year, Takeuchi announced that the first 100 units of its TB20e, an electric compact excavator, will be available at various United Rentals locations across North America. Built by Takeuchi itself, the battery-powered excavator is the first product to be released in the company’s anticipated full lineup of electric products, which will be created to meet its ESG goals.
Offering the same performance that Takeuchi’s diesel-powered TB216 compact excavator does, the TB20e is 100% battery powered, enabling it to provide lower noise and vibration levels than the diesel-powered compact excavator, while also emitting no exhaust emissions. And when it’s completely charged, the TB20e provides a continuous working time, which ranges from four to eight hours, fully dependent on the application and environment in which it’s utilized in.
In addition to offering an operating weight of 4,255 pounds, the electric compact excavator has a bucket capacity of 1.34 cubic feet, along with a primary auxiliary flow of 9.0 gpm. Furthermore, it has a reach of up to 13 feet and 4 inches, as well as a digging depth of 7 feet and 10 inches, at most. To ensure its operators remain as comfortable as possible, the TB20e also has a spacious station that features a high-definition, multi-informational color display.
“United Rentals and Takeuchi have a long history together, [so] we’re pleased to be the first to offer the environmentally-friendly TB20e excavator,” said TJ Mahoney, vice president, supply chain, United Rentals. “Not only does [the excavator] provide our customers a more sustainable equipment option, it’s also more cost efficient to operate.”
“The product and market development for the TB20e took place in North America, so it made sense to debut the machine here as well,” added Clay Eubanks, director of global sales, Takeuchi. “We’re excited to see how [United Rentals’] customers react to this new environmentally friendly excavator.”
Meanwhile, Caterpillar—which has been dedicated to working on electrification for the last 30 years—is focused on increasing the power of some of its high-volume loader and excavator product lines. As an example of this dedication, in October, the company showcased a variety of fully electric prototype machines at bauma 2022. From a sustainability standpoint, one excavator especially stood out: the Cat 301.9 electric mini-excavator. Providing users a Cat 48V, 32kWh battery, the excavator has a run time of up to eight hours on one charge; this run time declines to five hours during continuous trenching though.
Additionally, the company has created the Cat 320 electric excavator, which also has a run time of up to eight hours on one charge. However, it utilizes a different battery than the Cat 301.9 electric mini-excavator does, as it features a Cat 600V, 320kWh battery instead.
“Each machine will also include an onboard AC charger, which will enable it to be charged overnight,” said Corne Timmermans, vice president, sales and marketing, Europe, Africa and the Middle East, Caterpillar. “We’re also planning on providing DC fast charging options that customers can utilize during their break times.”
Both of the excavators are anticipated to be available for customers in regions of Europe and North America within the coming years, as the Cat 301.9 electric mini-excavator is expected to be the first commercially available electric excavator offering.
At the same time, Caterpillar has also issued seven sustainability goals that it’s striving to achieve by 2030. The goals will vary considerably in their focal points over the next eight years, ranging from reducing absolute greenhouse gas emissions from its operations by 30%, to decreasing its landfill intensity by 50%.
“We have set a goal to have 100% of the new products that are released through 2030 be more sustainable than the previous generation,” stressed Jason Conklin, senior vice president, global construction and infrastructure, Caterpillar. “To achieve this goal, we will collaborate with customers, decrease waste, enhance the design for rebuilding and remanufacturing, lower emissions and improve our efficiency.”
As an example of Caterpillar’s sustainability initiatives’ results, he added that “100% of [the] new products introduced in 2021 were more sustainable than previous generations.”
OEMs Should Consider Multiple Options for Alternative Fuels
As Dr. Ray Gallant, vice president, product management and productivity, Volvo Construction Equipment, looks ahead to the evolution of zero-emission heavy construction equipment, he believes manufacturers need to realize a crucial fact. The key response to electrification or sustainable power isn’t just a single technical solution, but a variety of solutions that manufacturers will need to develop and then “bring into play”.
“Volvo Construction Equipment is working with technologies such as battery-electric, hybrid, hydrogen fuel cells and alternate fuels like hydrogen combustion, as a result,” Gallant said. “Simply stated, we’re interested in any energy source that can provide the energy we need in a sustainable process.”
For instance, small excavators are great fits for battery-electric drives. So, Volvo Construction Equipment has placed a 48-volt battery pack in each of its compact excavators. The battery pack can store enough energy for the excavators to conduct their daily work tasks on a general duty cycle basis. And, in order to recharge them, the company offers an assortment of charging solutions.
“Even heavier machines that use up to 120 kilowatts can be powered with a battery pack,” he added. “The difference is that the battery pack goes up to a much higher voltage (600 volts for our excavators, in fact), so that we not only have faster recharge times, but also acquire the power we need—all with a reasonable weight and power balance.”
Once manufacturers’ customers require 120 to 150 kilowatts of power, along with longer duty cycles, they’ll need to consider other types of technologies as well. The primary reasons? For these types of requirements, excavators’ batteries are too heavy to supply the power that such customers need, especially if they have applications in which their excavators are utilized continuously for 24 hours. And very large battery packs tend to have very long recharge times.
“Therefore, we’re looking at different technologies like hybrids and alternative fuels that can power these systems in the future,” he said. “And we’re considering cable electric excavators that can connect directly to the grid and draw power while they’re being used, which are especially excellent options if customers have stationary excavators or applications.”
If customers are using larger excavators that require 200 kilowatts of power or more, they will need to purchase equipment that utilizes exotic fuels like gaseous or liquid hydrogen. As an example, they could obtain a hydrogen-powered direct combustion engine (a modification of a standard diesel block) or they could acquire electric energy from a fuel cell, which would power each of their excavators through a battery pack. Both options can be used for very high power ranges, especially those that are required in mining or quarry sites.
“One of the considerations for all power ranges and different technologies is that we’ll need to be much more efficient as OEMs, in order to recapture as much of this energy as possible while the excavators are being used,” Gallant emphasized. “Customers can’t afford to waste or lose power through an inefficient system if they have a battery pack with limited capacity.”
He continued, “That’s why, as manufacturers, we need to be more efficient in how we use the power, recover it in the non-work cycles and ensure the excavators and battery packs last as long as possible.”
With these goals in mind, Volvo Construction Equipment, which currently offers two compact electric excavators, is preparing to develop other options, as well. In addition, the company is expanding electromobility to larger excavators, such as the mid-size EC230E Electric, a prototype that will be available in North America in 2023 for customer pilot projects.
As it prepares for the future of hydrogen fuel, the company has recently introduced a prototype fuel cell hauler too. Utilizing a hydrogen fuel cell test lab in Sweden, which tests complete fuel cell units, the company is also continuing to invest in partnerships worldwide that will help it develop more sustainable equipment and initiatives down the road.
“Volvo Construction Equipment was the first construction equipment manufacturer to commit to an electric future for its compact machine range, as we stopped the development of new diesel engines for mini-excavator models globally—from the EC15 to the EC27—as well as compact front end loaders, from the L20 to L28,” Gallant added. “That’s a bold decision, made in step with a challenge from our president, Melker Jernberg, to stir the market by providing compact, zero exhaust emission excavators.”