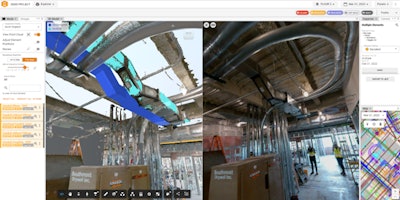
Building Information Modelling (BIM) is widely adopted across the architecture, engineering and construction (AEC) industry. It is often the catalyst for progressive workflows and has the potential to incorporate all of the important information related to the construction design lifecycle of the building.
Cloud-based platforms now enhance the experience of sharing and collaborating with this data with ease. BIM is constantly changing how the building industry collaborates and constructs.
The capacity to take model information and extend its use by giving it significance for other linked industries is the fundamental benefit of BIM that the construction sector should be aware of for processes and workflows. These procedures have an effect on fundamental operations including estimating, scheduling, logistics, and safety. These new capabilities have made it possible for systems to populate data more quickly, allowing for the earlier, safer, and higher-quality delivery of work.
BIM Coordination During Pre-Construction
During pre-construction, BIM enables users to identify issues virtually in a project where adjustments may be made at a far lower cost than they would be in the field during construction. Construction risk is reduced via a variety of BIM programs and mobile applications.
One of the biggest challenges in virtual construction is coordinating among the various subcontractors to produce quality virtual information. Contract structures that encourage the integration of team members and the various trade partners helps in producing better results.
The crucial and difficult process of design coordination ensures that building designs satisfy the functional, aesthetic, and financial demands of project stakeholders. Building system components are defined and routed during the process to prevent interference and to conform with various design and operating standards (Barton et al., 1983).
The coordination process necessitates a thorough understanding of building systems, such as ensuring that water lines are not placed above electrical equipment and that there is sufficient access for cleaning. Mechanical, electrical, and plumbing (MEP) coordination is one of the trickiest aspects of design coordination, according to experts in the construction industry. This is because of how complicated and numerous building systems are in a facility. BIM coordination does not simply involve reviewing hard clashes. There are other factors to consider including: maintaining clearances to be able to maintain and service equipment, verifying that code requirements for accessibility are maintained, and ensuring that models are constructed to an appropriate level of detail to be able to coordinate their real world physical geometry - and the list goes on.
BIM coordination allows you to recognize any MEP, interior, and internal clashes amongst the trades prior to further construction development. The digital BIM base helps in visualizing these clashes instead of waiting for the installations to begin in the field.
Once the coordination is performed, error reduction is one of the biggest advantages of BIM. BIM facilitates the identification of possible issues and the discovery of solutions before they result in errors on the job site by offering a complete view of the construction project.
Identifying and resolving disputes between building components before construction starts is also made possible by clash detection, which is crucial. Error reduction, rework reduction, and time and money savings are all made possible via clash detection. Without clash detection, conflicts between building elements would only be found during construction, necessitating expensive and time-consuming adjustments.
Using clash detection is the most proven way to identify construction discrepancy and to prevent design issues before they become an on-site challenge. It allows the subcontractors and design team to work together to identify and solve problems in the virtual world with the help of BIM, before they reach the real world (where they can be expensive) and delay the construction affecting the schedule and the resources required.
Companies see what will work and what won't work early in the design process rather than when construction begins. We can perform troubleshooting from the first day until the project is on site, making the construction process more efficient. We use this technology to find the best way for the engineering process. Spatial performance is improved by allowing manufacturers to test tight configurations before deploying equipment to site.
According to studies, construction projects usually take 20% longer to finish than anticipated. Labor, equipment rents, resources and other time-related expenses all wind up being 20% more as a result. Clash detection reduces costs by allowing project stakeholders to avoid conflicts before they arise rather than having to deal with them after they occur.
BIM Coordination During Construction
If BIM coordination in pre-construction is successful, then you are off to a good start, but what happens when unexpected conditions in the field require the teams to deviate from the plan?
Consider adopting a workflow to continuously capture the reality of your job site. This can be done via terrestrial scans, 360 photos, and a number of new and exciting technologies such as neural radiance field (NeRF). The benefit is being able to access your jobsite and continue the coordination process against the ever-changing construction site.
Twenty-three percent of firms report they are taking steps to improve jobsite performance with lean construction techniques, tools like BIM, and offsite prefabrication, as up to 70% of project changes are a result of design-induced rework recognized much later on site.
The savings that could be realized via BIM are too great to pass up. These technologies can help transform the expensive and ineffective nature of the AEC sector. BIM reduces interruption in the design and construction by identifying the construction discrepancies and getting rid of the majority of them, saving possibly millions of dollars on each project.