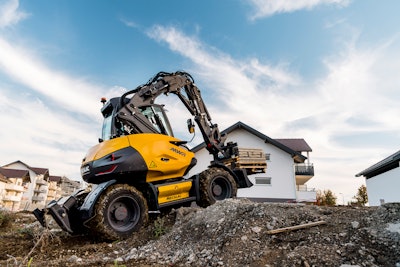
Although wheeled excavators have been popular in Europe for quite some time, they are now beginning to be used more often in North America, especially by county road departments and municipalities.
In particular, they can be utilized for common applications like ditch work, landscaping, utilities and virtually any other type of job that excavators are suited for, according to John Waldron, product manager, wheeled excavators, Volvo Construction Equipment.
As their popularity continues to increase in North America, manufacturers have been focused on changing the conventional wisdom that’s primarily associated with compact wheeled excavators: they’re often viewed as unstable.
“One lineup of compact wheeled excavators, known as MWRs, has been created with low centers of gravity though, enabling each excavator to be very stable without sacrificing operators’ ground clearance at all,” said Geoffrey Andrews, regional sales representative, Mecalac North America. “The excavators can still work on uneven ground, however—without any damage occurring to their undercarriages.”
“They’re very stable during operation, too, including when they travel uphill with loads,” Andrews added. “This is a feat of engineering that the North American market is taking notice of and embracing.”
Aside from a tight swing diameter and strength – Mecalac’s MWRs can lift as much as three tons up to 9.8 ft. high – compact wheeled excavators also feature increased safety features. The operator directly enters the cab from the side; there’s no need to climb over the attachment and turn around before the operator sits in the cab seat.
In addition, the company’s patented hydraulic quick coupler enhances safety by allowing the operator to control it from the cab, while the bracket design makes it virtually impossible for the tool or bucket to detach while in operation.
When compared to its tracked excavator models, Volvo Construction Equipment’s wheeled models, on the other hand, have the exact same engines. One distinguishing difference can be noticed between the wheeled and tracked models though. Their hydraulics are completely different. Unlike steered models, each of Volvo Construction Equipment’s wheeled excavators has a load-sensing hydraulic system, which enables operators to fully utilize all available engine power. In turn, they’re not only able to increase their responsiveness, but their controllability as well, leading to high stability.
“And just because the excavators have wheels, doesn’t mean they have to be solely operated with a steering wheel,” Waldron said. “After all, they feature Comfort Drive Control, which allows operators to control each of their excavators while using only the joystick, resulting in speeds as high as 12 mph.”
Technology Enhances Manufacturers’ Tracked Offerings
In regards to a majority of tracks in construction equipment undercarriages, Andrews believes that North American operators tend to utilize extra-wide integrators. Yet, in Holland, for instance, manufacturers create factory units on tracks, as the tracks can be bolted over a set of tires. Since the integrators that are developed overseas aren’t extra-wide, as they are in North America, they offer higher speeds, often traveling up to 1.5 mph faster than standard North American offerings.
As more and more North American operators seek out tracks that can be used in tight areas, Andrews notices they want more versatility. Therefore, they implement creative ways to utilize tracks in construction equipment undercarriages, leading manufacturers to determine various methods in which they can use one piece of track equipment in multiple ways. For example, some manufacturers provide track sets for wheeled units or enable operators to bolt a chain over their tires, resulting in the creation of a compact track loader (CTL).
“Mecalac has gone further with this idea though, as our compact excavators are designed to be multi-functional from the start, while also performing every function well,” Andrews said. “Higher speed is one aspect of this high-performing, multi-functional capability, as our crawler skid excavators are able to travel up to 6.2 mph, enabling contractors to change the ways they think about moving around their jobsites, along with how much they pay for transportation costs.”
According to Andrews, the Mecalac MCR model was born from a need for high-speed excavators.
“It performs like a skid steer,” Andrews said, noting that, “if you need something that’s versatile, it’s a high-speed excavator. Our machines already have a lot of functionalities built in (that North American customers are seeking).”
Andrews stresses that, at one point, North American jobsites had a lot of room to utilize their large equipment. That is no longer the case now though, as contractors need to maintain smaller footprints. With this in mind, Mecalac has developed the MCR Series, which is comprised of three crawler skid excavator models: 6MCR, 8MCR and 10MCR. Providing operators with a 360-degree cab rotation and a side-mounted, two-piece boom that offers high compactness, along with a high range of motion, the MCR Series is able to harness the speed and agility of CTLs, the maneuverability and digging capabilities of mini excavators, and the reach of telehandlers—in one machine.
In addition, when compared to conventional mono booms, the MCR Series’ side-mounted, two-piece booms provide operators an increased working envelope. Of equal importance, operators don’t need to reposition the excavators nearly as much as they have to move other tracked excavators, ensuring they have more time to focus on other tasks.
Featuring a hydrostatic transmission and drive motors, which are driven by a pump, each MCR Series offering can travel twice the speed of any traditional mini excavator that’s on the market. As a result of their speed, the crawler skid excavators decrease operators’ travel time across jobsites considerably, leading to faster cycle times and a decline in downtime. Since each of the excavators has a quick coupler, known as CONNECT, operators can transition from one attachment to another in a timely manner, as they never have to leave their cabs, further increasing productivity.
“Due to the MCR Series’ performance and versatility, operators will also have high ROIs, along with fewer excavators on their jobsites, enabling them to save space, too,” Andrews added. “This will be significant at urban developments as well, as operators especially need high ROIs and smaller excavators that can do more in these areas’ tight spaces.”
Aside from Mecalac, Volvo Construction Equipment has released new technology for tracks in construction equipment undercarriages. Some tracked models from Volvo, for example, have optional rubber track shoes. Consequently, operators can use crawlers on surfaces like asphalt, which they don’t want to damage. Detachable, the rubber track shoes can be used whenever operators need traction as well. Using a pad comprised of a durable rubber blend and placed on a steel plate, the track shoes reduce noise and vibration.
“The replacement of single rubber pads is also an easy, cost-effective way to maintain an excavator’s track system, which can be complicated and expensive to repair otherwise,” said Sejong Ko, product manager, large excavators, Volvo Construction Equipment.
Volvo Construction Equipment’s tracked excavators have long, wide frames as well, thus providing operators enhanced stability as they handle heavy loads. Additionally, they have narrow and short undercarriages that can be transported effortlessly.
“Differences in excavator undercarriage design do impact a machine’s durability,” Ko stressed. “As an example, the Volvo X-style chassis has robotically welded, single-piece upper and lower plates that are covered by a Lifetime Frame and Structure Warranty. Featuring heavy-duty guard plates as well, which offer protection under its superstructure and X-frame, the chassis varies from some OEMs. For instance, some OEMs have undercarriages with upper plates that are split at key stress points or straight plates that are welded on one side only—with no plate belly guard under the hydraulic swivel—instead.”
He continued, “With warranties ranging from three to 12 months, maintenance costs could add up quickly, an issue that the Volvo X-style chassis solves. Aside from providing operators these plates, the chassis has a reinforced idler frame too, allowing it to be used for rough terrain applications as well, as it also has high durability.”
Which Excavators are Best to Use—and When?
As operators consider the best times to utilize wheeled or tracked excavators, they will need to determine exactly which applications should be performed on the job, as well as the intended usage of the equipment they will be specifically using. Wheeled excavators, after all, offer benefits that tracked excavators don’t, and vice versa. For example, whenever operators use wheeled excavators, they’ll likely save money and time on maintenance and upkeep.
Furthermore, wheeled excavators are lighter than tracked excavators, enabling them to be used more easily, especially when they’re utilized in the proper conditions. At the same time, wheeled excavators are better equipped for long-distance travel, and operators arrive at their desired locations more effectively.
A common misconception is currently associated with wheeled excavators though, according to John Waldron—that by using them, operators will lose the stability they have while operating crawlers. However, that is not the case, as wheeled excavators are not only as stable as crawlers, they also ensure operators won’t sacrifice breakout/tear out forces, digging depth, power or reach whenever they use them.
“By driving excavators to various segments on their road jobs, operators can save considerable time and money. In particular, by using wheeled excavators, operators will reduce their reliance on a lowboy and eliminate the extra equipment, labor and time they previously needed to load and unload machines,” he said. “Wheeled excavators can also drive faster on roads than tracked models, cause less damage to driving surfaces and tow trailers with attachments or pipes, which decreases transport costs even further.”
The cost savings of purchasing a wheeled excavator goes beyond the initial purchase of the machine and continues throughout the excavator’s lifespan, according to Waldron. This is because wheeled excavators can equal both increased labor productivity and cost savings.
No commercial driver’s license (CDL) is required for the wheeled excavator, meaning the same person who operates the machine can drive it, Waldron explained. Compare that with a truck-mounted excavator, which may need to be supported with both an operator and a driver with a CDL.
Wheeled excavators are especially critical for usage in tight spaces, as short-swing wheeled excavators can work in one lane of traffic, when compared to conventional swing excavators that often require two lanes. If operators work on multiple jobsites that are spread apart, they can utilize wheeled excavators for such distances as well.
Waldron advises operators to use wheeled excavators that have two-piece articulating booms, as they enable them to stretch farther, dig deeper and closer to the excavators themselves, and reach higher.
“This can be especially beneficial in offering operators more flexibility to go up, around and under obstacles like bridges, guardrails and mailboxes,” he added. “Additionally, a two-piece boom can provide operators extra lift capacity in tight quarters.”
Although operators tend to utilize wheeled excavators in urban areas that have hard grounds and considerable distances for traveling, while tracked excavators are favored for shorter travel distances and ground conditions like mud and uneven terrain, Andrews believes this consensus is changing, especially as more multi-functional wheeled and tracked excavators enter the market.
“If operators plan on buying an excavator in the short-term and a skid steer later, I’d recommend the MCR Series since they’ll receive the functionality of both immediately in a single machine,” Andrews said. “However, if an operator wants to haul an excavator and skid steer to his or her jobsite, then Mecalac’s compact wheeled excavators (MWR), which are available in five models, ranging from 7 tons and up, might be the best solutions instead.”
If jobsites are near their shops, operators can actually drive their MWRs to them, thus eliminating the necessity to use a truck and a trailer to haul them. They can reduce any of the challenges that may have previously arisen whenever they tried to drive their trucks on cramped jobsites.
“Not only can operators drive the MWRs to their jobsites—they can tow a trailer, too,” Andrews said. “This capability is a new development in the North American market, so the conversation, concerning when to use wheeled excavators and tracked excavators, is starting to change.”
Waldron confirmed the versatility of wheeled excavators and suggested future innovations that could reduce overinvestment in excess machines on jobsites, saving contractors time and money.
“A wheeled excavator can be the Swiss Army knife of a fleet and prevent contractors from investing in multiple machines because it can utilize the same attachments as crawler excavators,” Waldron said. “Some OEMs also have material handling options on wheeled excavators, which are in high demand and really maximize what the machine can do.”
Preparing for the Future with Game-changing Technology
As Andrews looks ahead to the coming months, he believes that operators will continue to desire more from their equipment, and wheeled and tracked excavator manufacturers will notice their new requirements and respond accordingly.
“On our part, we’re offering a wheeled excavator that provides operators something different—multi-functionality, along with the ability to drive to jobsites while towing a trailer,” he said. “This opens up a different, more efficient way to work and a whole new way to think about wheeled excavators.”
Meanwhile, Volvo Construction Equipment offers operators Volvo Active Control, technology that enables automated boom and bucket movements to increase the accuracy and efficiency of the digging process in a more effortless manner. Operators only need to set the grade, push a button and complete their tasks, all while using one lever.
In addition, in-cab machine control apps will enhance operator performance, as they’re able to deliver high excavation accuracy quickly, while on-board weighing options will provide operators real-time insights into their buckets’ loads, leading to optimized truck loading.
“An auto engine shutdown feature will also help operators avoid costly hot turbo shutdowns,” Ko said. “As a result, if excavators are turned off without proper idle times, they will automatically run for a couple minutes before shutting down, allowing operators to simply turn the key and walk away.”
He added, “Operators should also be able to see every angle, as they strive to ensure safe rotation. With that in mind, a feature, known as Volvo Smart View, includes front, rear and side cameras, and offers operators real-time, overhead views of their excavators during operation—all on an in-cab monitor.”
Whether operators choose wheeled or tracked excavators, one change is certain. Compact wheeled and tracked excavators can provide operators with completely new ways to work in the future, in North America and beyond.
“Since they’re designed for ease of use and versatility, the excavators are reducing the amount of equipment that operators need to use on their jobsites,” Andrews said. “Whether operators are urban landscapes or ranchers that need to cover a lot of ground, these excavators are—and will continue to be—game-changing technology.”