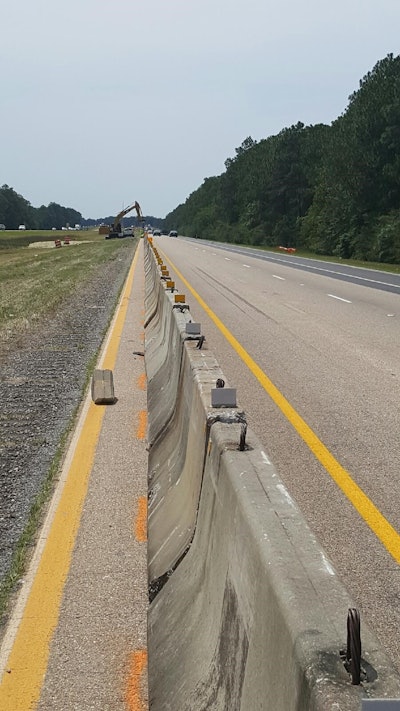
The work of building and maintaining America’s roads and bridges relies heavily on the effective management of traffic, which includes limiting proximities among motorists, workers and equipment in construction zones.
A Federal Highway Administration (FHA) analysis of Bureau of Labor Statistics data shows that collisions among vehicles and mobile equipment is the second most common cause of worker fatalities, contributing to an average 14% of worker fatalities in construction zones between 2005 and 2010.
Concrete road barriers are commonly used to direct the flow of traffic which curtailing worker exposure to passing cars, trucks and commercial passenger vehicles. Traditional barrier handling methods employed by contractors include rigging with slings or chains. Loads, however, are at risk of shifting or coming loose, and they are often free-swinging and difficult to control. On the ground, it often requires several tag line operators to guide materials into position. All of these factors introduce potential hazards on the job and increase the risk of injury.
Mallette Bros. Construction discovered a better way to handle concrete road barriers by utilizing a hydraulic lifting system. After researching different options, the Gautier, Mississippi-based asphalt contractor began implementing hydraulic lifters at the start of a 630-day road-widening project.
Previously, Mallette Bros. had been using a manual scissor-type lifting apparatus that required a total of six workers to handle tasks associated with moving and positioning concrete road barriers, including the traffic and maintenance personnel necessary to perform time-consuming lane closures.
Mallette Bros. had originally assumed that in order to stay on track by relocating two miles, or approximately 10,000 linear feet, of barrier wall once every two to three weeks, it would require a total of 8.5 days to handle just this portion of the job. Within the first seven months of the project getting underway, the time required was revised down to 3.5 days.
According to project manager Carlos Morales, “We went from the ability of six people to move 75 barriers a day all the way down to two or three people handling 250 barriers a day... there is no comparison from either a safety or productivity standpoint. We have more than exceeded the time frame allotted ourselves, all in a safe manner.
“We are working within three to four feet of the traveling public, driving 80 miles an hour,” he said. “We don’t even do lane closures when using this system. That’s how confident we are in the product.”