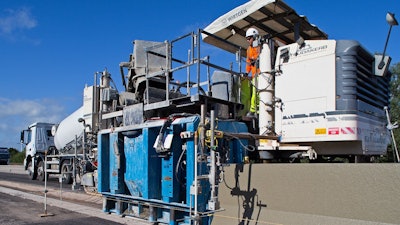
Whether drivers understand the engineering behind it or not, it is fair to say that most people would be able to recognize the steel barrier system. Often posted as ever-present guards for our on and off-ramps, they are one of the main cogs of the highway safety system.
In January 2005, in an effort to improve the country’s road network infrastructure, England’s National Highways agency committed to replacing all life expired steel barrier systems with concrete through the delivery of their Smart Motorway Schemes.
When the schemes compared key factors between the concrete barrier and its steel counterpart, they determined that the concrete option was a safer alternative, offering a longer design life, requiring less maintenance, and less likely to need repair after impact. Collectively, these factors contributed to cost reduction, improved traffic flow and limited the need for maintenance lane closures - greatly improving overall safety.
In March 2022, National Highways' Paul Unwin, who is overseeing the upgrades for National Highways, said: “Safety is our top priority. Upgrading these barriers will improve journeys and significantly reduce the risk of vehicles crossing over from one carriageway to another, improving safety and reducing the duration of incident-related congestion. We will continue to deliver safety enhancements to these motorways, which are among the busiest in the country and are relied on by hundreds of thousands of people every day.”
The Extrudakerb Concrete Barrier system can be installed as a surface mounted system, embedded to suit a schemes
requirements and adjacent works, or monolithically.Extrudakerb (Maltby Engineering) Limited
During this time, slipform concrete contractor Extrudakerb (Maltby Engineering Ltd) began the design and development of its own proprietary concrete barrier system. Originally, Extrudakerb operated as a licensed installer to Britpave Barrier Systems Ltd. In 2018, they decided to design and develop their own concrete barrier system as part of their innovations program, which was intended to be a new and improved alternative to other barrier products currently on the market. With this goal in mind, the Extrudakerb Concrete Barrier (ECB) system was created.
As with all slipform products, the system requires careful management and delivery to ensure quality concrete is provided. All processes and applications must be addressed from production to transportation and placement.
As concrete is a perishable commodity, timing is everything. Concrete’s consistency will often change during transportation, so it is critical to manage it to ensure it is delivered fit for its purpose to site.
Without a management system in place, any adjustments to the mix on-site rely on the experience and expertise of the site operatives. With a management system in place, contractors are provided actionable and recordable data on the quality of the concrete being placed, vastly reducing manual site adjustments that have the potential to cause time delays, increased costs, and waste material.
The Wirtgen SP 25i is capable of pouring large offset concrete profiles at standard heights of up to 6 ft. 7 in. or standard widths of up to 8 ft. 2 in. Offset molds can be left- or right-side mounted.Extrudakerb (Maltby Engineering) Limited
Through use of their in-house design, fabrication and technical expertise Extrudakerb are able to continually develop its system to ensure that all clients' requirements are met.
Designed with a 50-year life span as opposed to 25 years with a steel barrier, Extrudakerb’s ECB is fully CE Marked with a declared performance of H2 (high containment), W1 (working width of 0 mm, as the system did not move on impact to EN1317), VI2 (Vehicle Intrusion of <0.8 mm) and ASI B (Acceleration Severity Index 1.0 < ASI ≤ 1.4).
Like the Jersey barrier, the installation of an ECB system is dependent on client requirements: it can be surface mounted, embedded to suit scheme requirements, or cast monolithically.
Using a Wirtgen SP25i slipform concrete paver, to date Extrudakerb has placed more than 75,000 m on the U.K. roadwork infrastructure and expects to break 100,000 m by the end of the year (2022). Editor’s Note: these figures are for the U.K. only, though ECB has been licensed outside the country.
“Concrete consistency is critical in maintaining a high-quality product that allows for the maximum efficiencies and outputs achievable,” says Adrian Pickard AMICT, Materials & Concrete Technology Manager at Extrudakerb. Further ensuring they deliver the specs required, they invested in the VERIFI in-transit concrete management system by GCP. This is a system that marries sensor technology with predictive analytics in the measurement and management of the concrete during transport.
The VERIFI in-transit concrete management system automatically adds water and admixture within pre-set limits to achieve and maintain the ordered slump. The system provides automated process monitoring and control during transit from the ready-mix concrete plant to the jobsite by using sensors installed on concrete mixer trucks to monitor, measure, and manage concrete properties in transit.GCP
According to Pickard, “After including the VERIFI system onto their trucks, Extrudakerb has almost doubled efficiency per shift, having the capability to pave from 10-12 loads without the system to now achieving 16-20 loads with. Overall, the innovative partnership with Verifi has allowed Extrudakerb to push traditional boundaries, excelling against project timescales,”.
Extrudakerb’s booked projects are only ramping up with 50,000 m of barrier booked for commencement in 2023.