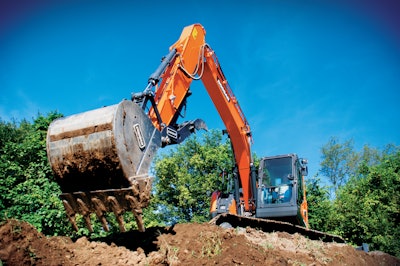
There is much more to selecting the most appropriate excavator bucket than meets the eye. Tip radius, width, heel depth, weight, ground-engaging tools (GET) and the type of coupler all have a major impact on the overall performance of the excavator in a given application. Incorrect application can yield decreased productivity and increased maintenance costs.
When selecting a bucket, bigger isn’t always better. “If you use a bucket too big for the material density, it can have a major effect on performance or cycle times, as well as stability of the machine,” says Ryan Neal, product application specialist, Caterpillar.
“The most common mistake is selecting a trenching bucket that is too large for the excavator,” says Lee Smith, excavator product specialist, Doosan Construction Equipment. “Some excavator owners think a bigger bucket will increase productivity. However, that is not always the case.”
Sizing the bucket to both the excavator and the application will help to maximize productivity.
Using a wide bucket in hard material may also create extra wear and tear on the bucket and the pins on the machines, potentially causing downtime for the customer, Neal points out.
“However, if it is too narrow, the bucket will not have enough capacity for a speedy job,” says Horton. “Also, the fewer teeth that are engaged with the material, the higher the force per tooth will be achieved, and thus provide less stress on the machine.”
Know Your Weights
It’s important to understand the density of the material being moved. “That will determine the size of the bucket,” says Neal. The amount of material to be moved also factors into the equation.
“When properly sizing a bucket to an excavator, Doosan evaluates the bucket weight and capacity,” says Smith. Find an average density of the material to be moved. Then compare that to the tip capacity of each excavator. By doing so, the goal is to maximize the production of the machine.
Make sure you include all weight on the end of the stick. “A customer needs to look at all other attachments on the machine,” says Smith. “Is there a quick coupler on the machine? Does the customer have a clamp on the arm with the bucket? The attachments need to be considered when evaluating the total amount of weight that can be moved by the bucket.”
Match Bucket to Duty Cycle
Duty cycle and the strength of the bucket directly impact maintenance cost. “It is best to choose a bucket that is described at the proper duty rating and manufactured with the best high-strength and wear materials,” says Horton. “A lot of time can be wasted in maintenance of a bucket by performing repairs or applying hardfacing and plates if the bucket is made without abrasion-resistant or harder alloy steels.”
General-purpose and heavy-duty buckets are commonly used in normal digging conditions and materials. “But when a customer is in a highly abrasive material, it can play havoc on a general-duty or heavy-duty bucket,” Neal states. “That is when they should consider using a severe-duty bucket, knowing that there is a slight trade-off in bucket capacity and extra weight in the bucket. But it will last much longer than the non-severe-duty buckets.”
Leading Edge Attachments offers rock ripping buckets with SHARC (Shanks on an ARC) technology, where the teeth rip the rock one tooth at a time.
The increased durability translates to less maintenance. “If the material is hard or compacted rock is involved, a severe-duty bucket will save the operator time and money by saving on maintenance,” says Horton. “A severe-duty bucket costs more at the time of purchase. However, it will pay for itself in a short period of time and thus save money in the long run.”
Yet, a severe-duty bucket isn’t right for every task. “With the additional guarding on the top, sides and bottom, there is some additional weight compared to the heavy-duty bucket,” says Smith. “There is no need to add weight if it is not needed. You will get more work done by optimizing the attachment at the end of the machine with the material being moved.”
The tip radius changes with duty cycle. “For each higher level of duty, the tip radius decreases and so does the capacity,” says Horton. “The harder the material, the more a short tip radius is needed. So if the material is soft clay, a high-capacity general-purpose bucket can be chosen. If the material is hardpacked dirt, a heavy-duty bucket will be required. If the material is compacted cobble and gravel, a severe-duty bucket will be needed. If the material is sandstone, limestone, shale, caliche, decomposed granite, asphalt, coral or frozen ground, a rock ripping bucket will be required.
“It is best to have several different width buckets of different duty types,” he adds. “Unless the operator is strictly digging in sand and clay where a general-purpose bucket may be sufficient, it is recommended to always use heavy-duty and severe-duty buckets, and use rock ripping buckets for real tough applications.”
Learn Geometry
Bucket geometry has a substantial impact on performance. “For example, if the tip radius is too long, it will affect breakout force drastically, meaning the machine may have a harder time breaking through tough material such as hard stone or compacted dirt,” says Neal.
“Choosing a bucket that has a shorter tip radius will provide higher tooth forces for digging or ripping through tough materials, thus better penetration.”
“Choosing a bucket that has a shorter tip radius will provide higher tooth forces for digging or ripping through tough materials, thus better penetration,” says Horton. “Also, the bucket with the least teeth in contact with the material at any one time will provide higher tooth forces. Of course, buckets that have short tip radii are often lower capacity. In order to achieve the highest productivity, the bucket characteristics of number of teeth, width, tip radius and capacity should be matched with rippability of the material to be excavated.”
A longer tip radius gives operators more capacity. “The trade-off is the operator’s cycle times will be a little slower when filling the bucket. A shorter tip radius provides more arm and bucket breakout force and faster cycle times,” notes Smith.
Heel depth can affect how the material goes into and out of the bucket. “Sometimes in wet, sticky material, the dirt or stone has a harder time discharging out of a bucket with a long heel,” says Neal.
“Some buckets have a more protruding heel and a large capacity, but can hit the material while digging, and thus cause drag on the machine and excessive wear on the bucket,” says Horton. “The best buckets are those that have the heel that does not stick outside of the tip radius.”
“A deep heel depth is usually paired with a long tip radius to offer a high-capacity bucket,” says Smith. “A shallower heel depth increases bucket and arm breakout forces. The tip radius and heel depth should be selected based on what the contractor is doing.”
Match GET to Conditions
GET also has a major impact on performance. Consider the bucket teeth.
“The teeth have to cut through the material causing the least amount of drag on the bucket,” says Horton. “The fewer the teeth engaged with the substrate, the more penetration. However, the teeth will wear faster and have to be replaced more often. A sharp single spike tooth will have high penetration but a shorter life. Twin tigers offer high penetration but also side ripping when used on the corner bucket locations.”
GET also makes buckets more suitable for tough conditions. “Adding replaceable bucket protection GET is a great idea for high-abrasion applications, depending upon the design of the bucket,” says Horton. “Sandstone and materials with highly abrasive content can wear out most buckets prematurely, and although these guards add extra weight to the bucket, the protection that they provide justifies any negative aspects.”
“It all comes down to material type as to what type of GET you use,” says Neal. “Whether it’s bucket teeth or extra guarding to protect the life of the bucket, there is a fine balance between longevity of the bucket and overall productivity. The heavier the bucket, the less payload the machine will be able to achieve.”