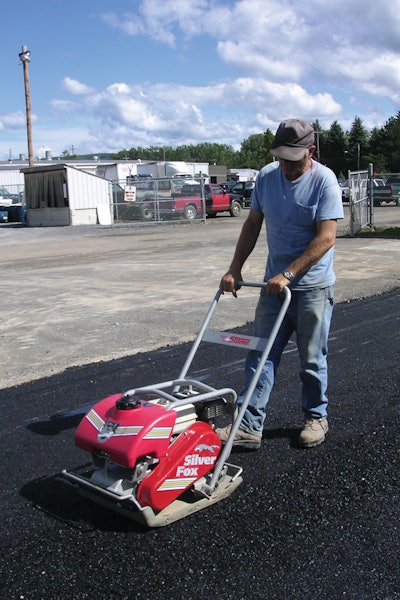
Equipment is a key element in paving and pavement maintenance. One key piece of equipment for almost all jobs is a plate compactor. Plate compactors can be used to compact sub base and asphalt on driveways, parking lots and repair jobs. They are also useful in confined areas where a larger roller may not be able reach. When it comes to selecting the right plate compactor, contractors have a few options to consider.
There are three main categories of plate compactors: a single-plate compactor, a reversible plate compactor, and a high performance/heavy-duty plate compactor. Which one a contractor chooses depends on the size and type of job he or she is doing, says Torsten Erbel, Multiquip's director of product management.
Single-plate compactors go in a forward direction only, and are probably the most popular choice for smaller asphalt jobs. Reversible plates can go in both forward and reverse, and some also operate in a hover mode, Erbel says. Reversible and high performance/heavy-duty plate compactors are often used for sub base or deeper depth compaction, he adds.
Plates on plate compactors are usually measured in width, and sizes can range from 15 to 25 in., says Wacker Neuson's National Product Specialist Jim Lewis. But width isn't the only measurement contractors should look for when purchasing a plate compactor. "Most of the small plate compactors generate around 3,000 to 4,000 lbs. of centrifugal force," Erbel says.
Read next: Know Your Compaction Facts
"Centrifugal force should not be interpreted as how hard a plate 'hits'. For many years the industry has used this term as comparative value and contractors have silently adopted it without truly understanding that the value of generated centrifugal force alone has no influence to performance," Erbel adds. "Other values such as amplitude and weight will contribute to the overall plate performance." Contractors should carefully review all the printed specifications when purchasing a plate compactor.
The eccentric frequency of the plate is another factor to consider, says Ed Varel, engineering project manager for Stone Construction Equipment. Lower eccentric frequencies (or vibrations per minute - vpm) are good for cohesive soils compaction. For asphalt and granular materials, contractors will want to look for a higher vpm, Varel says.
Contractors should also look at the plate itself. Is the plate made of cast ductile iron or steel? "A cast ductile iron base plate may be stiffer allowing for more efficient compaction of the material," Lewis says.
The shape of the base plate also affects compaction. A curved plate can make turning easier and prevent the plate from gouging the asphalt, Erbel says. How can you tell if the plate is curved? Erbel says to look underneath from the center of the plate to the edging. Although it is hard to notice, the plate will be slightly bent up, he says. The geometry of the plate is important for working in tight places, Varel adds.
Aside from the plate itself, contractors should make sure the plate compactor comes with a water tank. The water helps create a barrier between the hot asphalt and the cold compaction plate preventing the plate from sticking to the asphalt, Erbel says.
A new feature plate compactors might have is an anti-vibration handle. The anti-vibration handle cuts down on vibration transfer from the plate to the operator, creating more comfort for the operator. In addition to anti-vibration, Lewis suggests looking for a plate compactor with a central-mounted handle. "A central-mounted handle makes it easier to maneuver on the asphalt and is less apt to do any cutting or tearing of the material," Lewis says.
A swinging handle can also make maneuverability easier for an operator. "Sometimes the handle is mounted in the back; sometimes it's mounted in the center of the plate. Depending on the mount location it gives you a different swing range and also different heights as you swing the plate handle forward," Erbel says. "When the handle is mounted in the center then the operating height of the handle seems to be more level in either direction and more comfortable for the operator."
Although plate compactors are often self-explanatory pieces of equipment, contractors need to make sure they understand how to operate the compactors and how to maintain them to keep plates in good working condition. As with most equipment, Lewis says it is important to follow the operator's manual for maintenance. "The majority of maintenance is for the engine, and contractors should follow the engine manufacturer's recommended intervals, quantities, and types for oil, fuel, and air filters," Varel says.
And make sure to clean off the base plate and in between the plates daily to remove any asphalt that may be stuck on. Lewis also says to make sure the water tank is free of debris. Daily checks of hardware, especially bolt tightness, will help prevent any unnecessary downtime on the job. Varel adds that contractors should check belt tension and condition and engine rpms weekly.
Erbel also suggests inquiring into the type of service a manufacture offers with the plate compactor. Is there a warranty? How long is the plate compactor covered? Are there any exclusions in the warranty? What type of service support do they offer and who handles that service? What is the parts availability like? "The key for the contractor when selecting a dealer is it's critical to understand what kind of support the dealer can give him or her," Erbel says.
When selecting and purchasing a plate compactor, it is important to look at more than just price. Make sure you find a plate the suits the types of jobs it will be used on, and make sure it has the features and elements to allow you to get the best compaction and smoothest job possible.