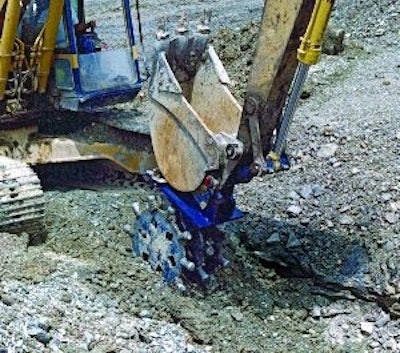
If you don't need or want to make the investment in a large, dedicated compactor, but require something with greater productivity than a walk-behind unit, a compaction attachment may be the answer. One benefit is it gives you flexibility to use the carrier (i.e., excavator, backhoe-loader or skid-steer loader) for other tasks.
"If you have a self-propelled roller, the machine (whole investment) will be parked in the lot until the specific job of compacting is needed again," says Heather Christensen, Mountain Valley Equipment, distributor of Stehr equipment. "With an attachment, you just remove it and use the prime mover in a different way. Only the small part of the investment -- the attachment -- sits unused."
Obviously, if equipment is sitting idle, it isn't generating a profit. "Any equipment purchased by the contractor is an expense. The more value you can get out of a capital investment, the better your return on that investment will be," says Bo Pratt, Rockland Mfg. "Choosing to purchase a dedicated machine for a specific purpose that isn't operating all the time ? or in other words, producing value ? doesn't give you as good of a return as purchasing a machine that can do more than one job and produce value more often."
There are also advantages when it comes to jobsite safety. For example, an attachment mounted on a carrier that provides extended reach may enable you to avoid the need to have workers in the trench. This in turn eliminates the dangers associated with having workers below ground, and may reduce or eliminate shoring requirements in some situations.
And because any power needs are supplied by the carrier, compaction attachments offer lower maintenance requirements compared to dedicated equipment. With fewer engines to maintain, you cut down on time and maintenance costs.
Static selections
There are a variety of different types of compaction attachments to choose from, including those that compact via static or dynamic means.
Static models such as compaction wheels utilize the weight of the machine and applied downward force to compact the soil. Since no hydraulics are required, they can be very cost effective. They also tend to be effective in various soil types.
"They are a good choice for cohesive and clay soils where vibration methods may not achieve good compaction, and may even be harmful, since water would be 'pumped' upwards to the surface," notes Christensen.
A compaction wheel penetrates the trench fill with specially designed "feet," and achieves compaction from the bottom up rather than from the top down. Soil mixing and displacement achieved during static compaction also limit the possibility of voids and bridging.
Compaction wheels are available in a variety of sizes and styles. You will usually want to choose the largest size your carrier will support; however, keep in mind that if it's too heavy or large, it can be difficult to maneuver.
Style options include hexpad, sheepsfoot and tamper-type "feet," as well as solid drum-type wheels. Typically, soil type determines which is most appropriate. For cohesive soils, such as clay and silt, manufacturers may direct you to a sheepsfoot/roundfoot wheel, which compacts the soil with penetrating, manipulating and mixing actions.
For granular soils, such as sand and gravel, a wheel with hexpad or tamper feet is often the better choice. "This type of wheel delivers more impact area," says Pratt, "and it compacts by pressure with some manipulation."
A solid drum wheel typically features "general-purpose" feet to accommodate a range of soil types.
In addition to foot style, you will want to select a wheel that readily self cleans, especially if you're working in wet soil conditions. This gives it the ability to work through the fill and prevents the attachment from "balling" up.
Dynamic options
Compaction via dynamic means (i.e., boom-mounted hydraulic plate compactors) is accomplished through the regulated hydraulic oil flow and pressure the carrier provides, explains Tony Neikirk, Okada America. The oil drives an offset rotator or eccentric that, in turn, creates vibration and impulse force that compacts soil and other loose granulated materials. Essentially, soil particles are rearranged and any air trapped between them is forced out.
Vibratory plate compactors are a great choice for granular material, since vibration can readily move these particles. "Because of the impulse force this attachment provides, the plate compactor can also serve as a very effective driving tool for applications such as driving pile and post, sheeting and sea walls," Neikirk adds.
Vibratory plate compactors are available in single-, double- and triple-plate styles. Double- and triple-plate models can be used on skid-steer loaders and tractors for compacting flat areas such as road bases.
A single-plate version is a suitable choice for excavators and backhoes used in trenching applications or for MSE (mechanically stabilized earth) walls, such as those often installed next to highways for soundproofing. "A compactor used in these situations must be 'handy' ? not too large ? to be able to reach any single spot in trenches," says Christensen. "For MSE walls, there is often just a small space from which to work. A single-plate compactor can get into those small spaces with a great deal of force."
According to Neikirk, a boom-mounted plate compactor provides greater amounts of impulse energy compared to static compaction methods. "And they are economically priced compared to [dedicated machines]," he notes. "[Attachments] allow the user to maximize the capabilities of the carrier, and they are generally simple to install or remove, since they replace the bucket. They are excellent tools for compaction in the trench, on inclines or any other application where impulse forces from 3,000 to over 20,000 lbs., as well as 2,000+ cycles per minute, can come in handy."
Easier Slope Compaction
Compaction on slopes can also be accomplished with attachments such as the Thompson Slope Packer offered by Rockland. The excavator-mounted attachment consists of a self-cleaning drum with dozer cleats, and it uses the down pressure of the excavator to pack slopes in any condition and grade.
Typically, contractors use a crawler loader or dozer to "walk" across the sloped area. But with the Slope Packer, the excavator can be stationed at the top of the slope, where it reaches down with the attachment to pack and roughen the soil. Because the excavator is not required to walk horizontally across the slope, it can operate in conditions not suited to other equipment. And the ability to accurately position the attachment enables the operator to pack soil right up to obstacles without damage.