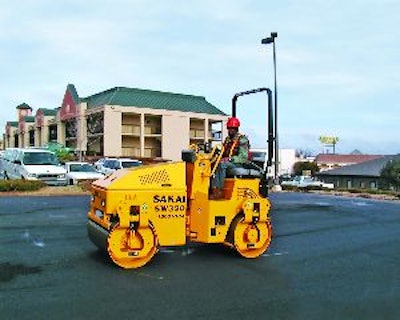
Your niche is paving small driveways, but maybe it's time to move up to bigger driveways, parking lots, and possibly secondary road paving projects.
That one-ton roller works great on smaller paving jobs, but you know you will need a bigger and faster unit to handle larger projects. Just how much bigger is one question contractors need to answer before making a jump to a midsize roller. Drum size, vibratory frequency, special features, and compatibility with present and future applications all come into play when thinking about moving up the paving ladder.
"Contractors will see a lot of changes in rollers when they move from a one-ton to a midsize roller," says Shane Sirmons, marketing manager for Sakai America. "The most obvious is the engine as they move from gas to diesel. Smaller rollers also have a lower drum frequency. Higher frequencies become very important on larger paving projects where roller operators have to move fast to get the job done."
Sakai America offers three roller models in the 3-ton category, with 39-, 47-, and 51-inch drums. Sirmons notes that the 47-inch drum is a likely candidate for contractors looking to move into the small parking lot market. As a rule of thumb, he adds, three-ton rollers are ideal for 50-car lots, but operators will need to consider larger rollers, possibly those in the seven and eight ton category, to handle larger Wal-Mart type parking lots.
Age old concept
"You have to make sure the machine that you buy will get the job done," says Hamm America Marketing Manager Bruce Monical. "The age-old concept still applies: the heavier the hammer the faster the job gets done. The name of the game is the same, too, no matter what size job contractors are paving. The goal is to keep water out of the new pavement, and compacting hot asphalt with a vibratory roller works best in most applications."
"Application will drive the buying decision," he says. "How much material, how deep, and how much time it will take to get the job done all come into play. A wrong machine for the application may be too small or too big; it may hit too hard or not hard enough. The roller also needs to match the other equipment - the truck, trailer, and paving machine - in your equipment lineup."
Hamm America's midsize roller lineup includes a 2 ½-ton, 47-inch drum roller; a 4-ton, 51-inch drum roller; a 4 ½-ton, 54-inch drum roller; and a 7 ½-ton 59-inch drum roller. At the upper end, says Monical, contractors can compact faster and deeper, but with the larger drum size they will lose the ability to pave alleyways and bike paths and lack the maneuverability necessary to work around light poles and other small objects.
"Ideally, contractors moving from small driveway rollers would like the advantage afforded the smaller size but still have the ability to do larger paving jobs," Monical adds. "They would like the bells and whistles of even larger machines, too, in a midsize roller, including high frequency, a nice comfortable platform, warning devices, and so forth."
Trending
"Trends today in the midsize roller market are mainly for better ergonomics for the operator, more comfort, lower noise and vibration, and better visibility," explains Wacker Sales Engineering Manager Mark Conrardy.
"Companies are trying to put 'big roller' features into the smaller machines. One of the keys is for operators of the bigger machines to have good visibility and see the contact point where the drum and pavement meet. You don't want the operators to have to stretch or lean out to see the work they're doing. On larger jobs especially, fatigue can become an issue."
Wacker manufactures four roller models. The smallest of the four fall into the 1-ton and 1 ½-ton categories. The largest is a 2 ½-ton unit with a 39-inch drum. "A 1 ½-ton roller is still fine for driveways, but going to a 2 ½-ton machine would be too much in most parts of the country," Conrardy points out. "The mix used for driveways generally is for lighter loads and has finer aggregate, and the larger machines have too much weight for that material."
He goes on to explain that Wacker's large roller gives the operator added versatility over its smaller counterparts. He says each vibratory drum offers a choice of high or low compaction force to fit a variety of conditions and applications. The lower centrifugal force is ideal for asphalt conditions whereas the higher centrifugal force is better suited for work in granular subbases.
Both Monical and Sirmons emphasize that drum vibratory versatility is one of the benefits that comes with larger machines. All their midsize units feature independent drum vibration to match the application and water systems that keep the drums free of asphalt buildup.
Payback time
Before upgrading to a larger roller, Conrardy says contractors should ask themselves if there will be enough work to justify going to a bigger machine.
"They should ask themselves how long will it take to payback the incremental difference in price with additional work. If the time frames and upgrades are worth the extra work that can be done, then the answer is 'go for it.'"
Adds Monical, "Some contractors use smaller commercial jobs as stepping stones to larger projects. Others do a great job with the smaller jobs and are content to stay there. Before buying a new roller, it's important to know which type of contractor you are. If you're planning on moving up to even larger projects, then a higher-end midsize roller would be in order."
"Certainly, there is a direct relationship between size and cost, with more steel and a bigger engine, hydraulic system and vibratory system in larger units," Monical says. "Maintenance costs will go up, too, as contractors upgrade, but that expense is more directly proportional to use than it is to the size of the machine."
Another important question to ask is "will my new roller be compatible with my current equipment lineup?" Going up in roller size often means getting a bigger truck and trailer, and possibly a new paver. To get optimum use out of all your paving equipment requires that their capacities reasonably match.
Other considerations
Options. In terms of special "bells and whistles," manufacturers incorporate most of them as standard equipment, including ROPS and seat belts. Hamm, for example, offers only two options on its midsize units - a couple of additional work lights and a flashing beacon.
Durability. Sakai's Sirmons notes that in their search for a new roller, contractors will likely come across "cost-down" units. "The price may be attractive," he says, "but the long-run maintenance costs will more than likely make up the difference in a hurry. Make sure to buy a machine that is well built. Durability and technology can differ from model to model and manufacturer to manufacturer. Look for solid steel construction with heavy-duty components, and make sure you're getting a machine with the latest model engine that meets current CARB and EPA standards."
In general, manufacturers advise contractors to take it one step at a time while moving up the paving ladder. Fit your roller to the application, all the time considering how it will mesh with the rest of the equipment in your paving lineup. Glance into your crystal ball. Determine what types of projects are in your future. You don't want to buy a machine that you will outgrow tomorrow. You also don't want a machine that, as Monical says, will be too big or hit too hard for current projects.
Application, payback time, and compatibility (with equipment and future growth) are all part of the mix as contractors consider their next roller purchase.
Based in Neenah, WI, Rod Dickens is a freelance writer specializing in the construction industry.