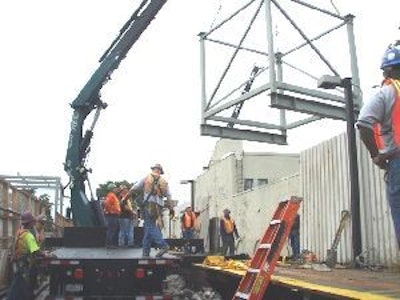
When Granite Construction won the bid to repair several of the elevated subway stations in Brooklyn, New York, it was faced with some daunting challenges. Many of these stations hadn't seen any meaningful repair since the era of Teddy Roosevelt. Next, there was little access to the work area except from the subway tracks themselves. And while some of the sites could be accessed at street crossings, it would mean employing multiple 300-ton cranes to lift the 24,000-pound sections of precast piers, causing considerable traffic headaches, neighborhood disruption and more.
What Granite Construction needed was a piece of heavy equipment that could travel on the rails, keep up with the work on the stations as needed, and yet be easily transported to other locations. This piece of equipment needed to meet some very special requirements. Besides the basic ability to lift multi-ton loads, the equipment needed to be:
- Compact enough to travel on the rails through the tight 19th-century tunnels of the New York City subway;
- Light enough to be lifted some 30 feet above the ground to sections of elevated rails;
- Able to propel itself through the subway tunnels;
- Able to tow heavy loads from the front or the rear;
- Transportable from one end of the city to the other.
And all of these things needed to be accomplished without impeding the existing flow of subway traffic.
Enter Fascan International and its team of Fassi Cranes and Crane Specialists Inc. The team took Granite Construction's requirements and set to work creating exactly the kind of equipment that the company needed.
Developing a Solution
Fascan took one of its existing crane designs, and began to incorporate the adaptations that the equipment would need. Construction of two units took place over a ten-week period at Fassi's plant in Albino, Italy.
Once completed, the cranes were shipped to Crane Specialists Inc. in Manheim, Pa, where they were each fitted to a truck chassis and enhanced with customized features.
The completed "transit cranes" exceeded expectations. The cranes were radio remote controlled. Pressure readings, operating temperatures and safety mechanisms could be monitored via the screen of the radio remote. An operator could even perform equipment diagnostics on the crane remotely.
The cranes were constructed with four remote-controlled stabilizers. But unlike many cranes, the stabilizers could be custom deployed to ensure strong support for the unit without impeding the continuous subway traffic.
For example, if the crane was on the rails, the stabilizers on the right side could be extended out and down, and the stabilizers on the left side could be extended straight down. With this modification, work could continue and subway trains could pass. In addition, the crane "knew" exactly where it was working within the 360-degree arc and could prevent an operator from crossing over the perimeter where the stabilizers had not been extended.
"Just having the flexibility to work on, above, or along the rail system makes this equipment extremely valuable," says Jeff Kline, vice president of Crane Specialists. "Granite Construction found that they could do much more with this truck and crane unit than they imagined when they sat down to design it."
The crane also used installed pintle hitches with front and rear air brakes. This gave the unit the ability push or pull specially built low profile trailers to transport materials along the rails.
The rear of the crane'’s truck was also counterweighted to give the operators full load capacity off the front of the truck without having to use another outrigger jack on the front bumper.
Rapid Results
The transit cranes were put into service in September of 2009. The Brooklyn project was still in its early stages, consisting mostly of demolition, but the new cranes started to make a contribution right away. Within hours of being put on rail, they were used to install a pre-engineered pedestrian bridge at one of the stations, allowing foot traffic to work around the construction and cross over to an alternate southbound track and platform to make connections.
Since then, the cranes have been used to shuttle excavators and equipment between stations - in short, acting as a locomotive. When demolition is completed, they will be used to install precast concrete structures to replace the 100-year-old passenger platforms at the stations. The truck will be loaded with precast sections at a street crossing, and will then roll along the track to the site of installation.
The units will also be pushing and pulling utility flat cars with 100,000- to 150,000-pound loads along the track. Since there is very little friction on steel rail wheels, the units can easily push much more weight than other means of transport.
"Having the ability to work on this project without stopping the flow of traffic in one of the busiest cities in the world is a remarkable advantage," says Kline. "People can walk right above a work site and not even know how much is going on under their feet."