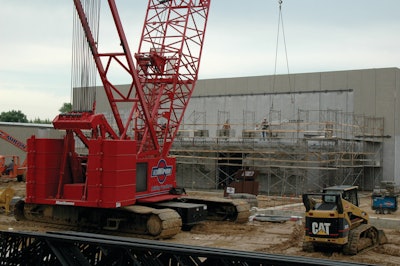
Miron Construction is one of the largest contractors in Wisconsin, with offices in Neenah, Wausau, Milwaukee and Madison, as well as Cedar Rapids, IA. It provides construction management, design/build and general construction for the health care, educational, industrial, commercial/retail, governmental, religious and environmental markets. It is also recognized for such services as Building Information Modeling (BIM), Sustainable/LEED and Experience-Based Design.
The company has been a frontrunner in school construction for many years. It fosters this business by providing no-cost, pre-referendum consulting services to local school districts. Its services include assisting with development of plans, education of the local community, publicizing the referendum, etc. This process can often take a year or more, from the time a project is announced until it goes to a public vote. And there is always the risk the referendum won't pass.
Still, John Schneider, project executive, asserts the risk of failure is minimal. "We feel we do a good enough job, it's likely to pass in the majority of cases," he states.
Taking the LEED
One of Miron's recent school projects is the $15 million addition and renovation of the Lake Mills Middle School (LMMS) in Lake Mills, WI. The project, which broke ground in February 2009, includes a 62,000-sq.-ft. addition with a 36,000-sq.-ft. remodel of the existing school.
The addition was needed to house new classrooms, a kitchen/cafeteria and office space, plus bring the gymnasium under the same roof. A new geothermal heating system - which makes up a big part of LEED certification for the school - will significantly reduce overall utility usage, with anticipated savings of over 40% from a traditional system.
A leading authority in the Midwest on the LEED process, Miron boasts 58 LEED-certified professionals on staff, with more being trained. "We see sustainable design and construction as a point of difference," says Schneider. The company works with customers on the project design, plus ensures all materials used have low VOCs (volatile organic compounds). "We make sure we follow all of the standards."
On the LMMS project, a large portion of the original building was remodeled to minimize material use and demolition and disposal of large volumes of debris. Over 75% of the construction waste was salvaged or recycled and reused during construction. In addition, local materials were incorporated whenever possible to reduce the environmental impact of transportation.
Ups and downs from the start
Work at LMMS started while school was in session, presenting some initial challenges. According to Jay Kuhlman, project superintendent, "We were actually pouring footings for the foundation of the three-story [addition] while they were still playing baseball near the building. We only had one access [to the rear of the school] and that was from the front."
Since the front of the school was positioned at the top of a small hill, a ramp was constructed to move equipment in and out. This had its limitations. "We couldn't drive the concrete trucks up and down the ramp because it was too steep," Kuhlman explains. So, a 100-ton-capacity Liebherr 853 crawler crane was positioned at the base of the hill. "We loaded the concrete trucks on the top of the hill and used the crane to swing the bucket around to pour the footings at the bottom."
With pours taking place next to the building, the school had to be underpinned to maintain stability. "We underpinned the adjacent school down 15 ft.," Kuhlman says. "We put in support piers and a shotcrete wall to hold the school in place."
Other areas were shored up by placing soil against the building to maintain a 20-ft. earth bank. Large volumes of plastic were needed to maintain erosion control during the rainy spring conditions.
Unfortunately, such wet conditions weren't confined to the spring. While an access road now allowed easy entry to the back of the school, heavy rains in June created difficult underfoot conditions all around the congested jobsite. Still, this didn't stop progress. "It doesn't help it, but it doesn't slow production down to the point that it causes any problems," says Kuhlman.
This was due in part to three four-wheel-drive SkyTrak telescopic handlers used to move material. Not only were they able to travel up and down the ramp at the start of construction, they proved more than capable of traversing the thick mud and water later that summer.
Because of their versatility, the telehandlers are a primary part of Miron's fleet. "The SkyTrak is probably our main piece of equipment," says Kuhlman. "We have a lot of them." As a result, both the operators and mechanics are very familiar with the machines. "The brand is probably the most versatile for us just because of its ability to [travel through] mud; it lifts and levels itself; and it's the one we're most familiar with as far as repairs."
Heavy lifting required
By early July, precast concrete and structural wall panels for the addition were ready to be put in place. Initially, a three-crane rigging setup was expected to be used to set the 22.5- to 55-ft. vertical panels, which weighed from 19,500 to 50,000 lbs.
"Because the precast panels are so long, you had to have a certain place to pick them and roll, turn or radius them," says Kuhlman. "You couldn't just pick them at [both ends] because they would snap in the middle."
Miron worked closely with Spancrete, the panel provider, to determine the optimal picking points. As a result, a single 220-ton-capacity Manitowoc Model 14000 crawler crane was able to set even the largest panels in place.
A double line was used for the picks - one line raised the panel up and the second line held it steady to lift it off the trailer. "Once it was in the air, the one line was more than enough, because then it free floats," says Kuhlman. "Then you could pick the one line up and increase your pull vertically at that point."
Using this method, within days, the majority of both the vertical wall panels and horizontal floor panels had been placed and interior work could begin.
The LMMS project was successfully completed in August, just in time for the 2009 school year to start.