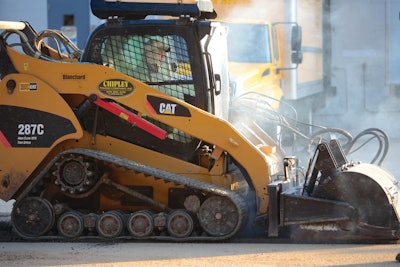
Compact track loaders (CTLs) have come of age as more and more construction firms have discovered the benefits they have to offer. Their attachment capabilities, low ground pressure, stability and maneuverability have made them an invaluable addition to many fleets. Following is a look at four companies that have spent the better part of a decade building their business around these machines, or enhancing their operations by adding them to their equipment mix.
Working All the Angles
Egnoski Excavating & Construction, Whitewater, WI, performs a wide range of residential and commercial construction projects throughout the local area. “I do jobs nobody else wants to do because they don’t have the equipment,” says Tom Egnoski, company founder and co-owner. “They’re not set up like I am.”
That setup includes two Caterpillar 247 multi terrain loaders, two IHI compact excavators and a small crawler carrier/dumper, plus an assortment of attachments. A small dump truck and flatbed trailer are used to transport the equipment, attachments and materials.
For years, Egnoski Excavating & Construction’s fleet included rubber-tired skid steers. Then, in 2003, Egnoski attended an open house at a Cat dealership in Milwaukee, where he demoed a multi terrain loader for the first time. “All it took was for me to drive it one time and I said, ‘I have to have that,’” he says. “There are some true benefits to track machines.”
Today, all of the company’s equipment is spec’d with tracks. “[Rubber tires] are too expensive — dealing with flats, and where you can and can’t go. With the track machines, I can go basically anywhere I want no matter what the soil type is,” says Egnoski. “I’ve been in some soupy, wet areas where you can hardly walk and I still go through them.”
The ability to effectively float across surfaces has helped secure work with area homeowners. “People are concerned today because they spend a lot of money landscaping their yards,” says Egnoski. Being able to travel across surfaces with minimal damage has proven a major selling point. “To the homeowner, that’s a big deal.”
In addition to low ground pressure, more contact surface on the ground provides greater stability on uneven surfaces. “I do a lot of driveways. With a rubber tire machine, it’s easy to start bobbing up and down because of the tires,” Egnoski comments. “With tracks, the machine stays more level. I have a grader that goes on the front of the loader. When you combine the two, you can do a super nice job on driveways and parking lots.”
Of course, one of the biggest advantages of both CTLs and traditional rubber-tired skid steers is their attachment capability. Egnoski Excavating & Construction has a variety of attachments in its arsenal, including hammers, buckets, plows, a roller, mower and more. Two frequently used implements are a Harley rake and a 5-ft. rototiller. The stability of the multi terrain loaders over variable surfaces has proven especially beneficial with these tools. “It all boils down to the consistency of the machine staying on an even plane,” says Egnoski.
The achieve a stable, even plane throughout operation has allowed Egnoski Excavating & Construction to complete jobs that would have been significantly more difficult, if not impossible, with wheeled equipment. For example, it just completed a job on a new home built on top of a hill. “They built it so high out of the ground that it had like an 8-ft. drop when you came out of the front door. They wanted to fill it in, so I hauled in 400 yds. of fill to get it built up so they actually had a yard around the house,” Egnoski explains.
The project required working at angles up to about 40° all the way around the house. “Basically, the whole job was working on this angle,” says Egnoski. “With a rubber tired machine, you could never stay on the hill. You would roll down the hill because of the amount of tire surface on the ground vs. the tracks. The width of the track is more stable on side hills. It worked out perfectly. You couldn’t have done it any other way.”
Fine for Grading
Lenny Seales, owner of L & K Equipment, Fort Lauderdale, FL, has a long history using skid-steer loaders, dating back to the 1970s. Like Egnoski, he first acquired a CTL around 2003 or 2004 following a machine demo. “I used it and between what I had and what [the dealer] brought out – a Bobcat T190 – it was a difference between night and day,” he states.
Seales initially utilized the T190s, but has since moved up to Bobcat’s T650 CTL, which has a 2,570-lb. rated operating capacity. “The T190 is very good for smaller jobs, but when you want to move dirt and get it done, that T650 is the only way to go,” he says.
The larger CTL has the added power needed for the applications L & K Equipment completes on behalf of Stiles Construction on large commercial and super structural building projects in and around South Florida. “Where there’s a major building coming in, that’s where you’re going to find me,” Seales states. “I take [the project] from the very beginning — from pilings, pile caps all the way up to ground slab. I do a lot of grade work.”
The T650 has enabled Seales to tackle these big jobs with ease. “That thing is a powerhouse,” he states. “It’s the most versatile machine you can put on the site.
“I can go into the ground and dig footers out with it,” he continues. “I can put sidewalks and curbs in with it... I’ve used auger attachments with it to auger holes on projects to put in 30- to 40-ft. light poles.”
The T650 is also used extensively for finish grading operations. “Tracks are the only way to grade,” Seales asserts. “With a rubber tire machine, you’re bouncing around. You have to straighten out the road you’re running on all the time.”
With 5 to 6 ft. of track on the ground, the CTL provides a smoother ride in these types of conditions. “It’s like it does the job for you, really,” says Seales. “You can cut such a fine grade with the track machines.”
More rubber on the ground also provides a stable platform for truck loading. “When you have a weight in the [bucket] of a skid steer with tires, all that weight goes in the air and the sidewall on the tires buckles. I don’t care how much air you have in the tires. They teeter; they bounce back and forth” Seales points out. “A track machine does not do that. It’s more stable, it goes more places and the biggest part about it is you’re not fixing flat tires. I’ve fixed my share of rubber tires, and that’s a big plus in itself.”
The maneuverability of the tracks is suited to working inside of structures, as well. “It’s the perfect machine to go into a building with because you have columns everywhere,” says Seales. “Ninety percent of machines can’t get around the columns or around the ground slab like that Bobcat can. It’s just so fast to get the job done.”
Tracks have also proven ideal for operation in the challenging Florida soils. “They’re great in sand and dirt,” Seales says. “They’ll go through about anything. If you take any kind of rubber tire machine into sand, you’ll bury it. The track floats right through it.”
A Versatile Addition
Chipley Company, Florence, SC, is a total site contractor self-performing all aspects of site work, including water and sewer, storm drainage, concrete work, grading, paving, landscaping and more. While its fleet includes some 65 pieces of heavy iron, compact equipment plays an important role in its operations, particularly a Caterpillar 287C multi terrain loader and 289C and 259B3 high-flow CTLs.
“We self-perform everything and that’s where the beauty of these machines comes into play,” says Roy Chipley, owner of Chipley Company. “We utilize them on every job. Many times, they’re spread over several different jobs, and that’s part of the versatility. You can put them on a trailer behind a pickup truck and move them from location to location.”
Once unloaded on site, there is little risk of the tracks damaging finished surfaces. “That is truly one of the other reasons that I like them,” says Chipley. “I can unload it in the road and it won’t hurt the road surface, and for the most part it’s not going to hurt the grass surface until you start to do major rework because you’re excavating. It can go up and over curbs without hurting the curb or the operator. It’s a much smoother ride for the operator.”
Chipley Company acquired the first of its track loaders in 2005 after Roy Chipley witnessed another contractor using a CTL on a grading job. “It just impressed me,” he says. “Then I had a job come up that was inside a mall. We had to replace their ancient storm drain system, and I needed a machine that could ride over brick pavers and in very tight areas.” Chipley rented a CTL from Blanchard Machinery, the local Cat dealer. “[They] never got it back. We ended up buying that particular machine.”
The return on this investment came quickly. “We were building subdivisions back then, and we could do all of our curb and gutter work, then put that machine behind [the paver],” says Chipley. “One operator could place fill material and put a power rake on and dress massive amounts of area with this one machine.” In the past, this might require a backhoe-loader to place and knock down material and a small grader or a tractor with a soil pulverizer to spread it around the site.
The combination of the track loader and attachment has enabled Chipley Company to replace certain equipment altogether. “When we stepped up and bought our [second machine], which was the 287C, I bought a six-way dozer blade, and that attachment replaced a small dozer,” says Chipley.
The combination has proven more maneuverable than the dozer it replaced. “We may be in a tight area and we’ve had to undercut to remove unsuitable soils. The trucks would be bringing in 15 yds. of material at a time and bulk dumping it. You can put one of the track loaders there with a bucket or this blade and level material in tight places where other equipment could not get into. It can be pushing materials or putting it in place behind curb and gutter,” Chipley explains. “In small places, it’s easier to put that machine in place than it is a D5 or D6 dozer. And it can get there behind a pickup truck instead of a lowboy.”
Attachments have proven a vital part of the track loaders’ success in Chipley’s fleet, allowing the machines to tackle a variety of applications. “Take a clearing job. Before we go in and lay trees down, we can place a cutter head on one of these units and put it in cutting the debris so there’s visibility for the big machines — they’re not getting wrapped up in the weeds and vines and small trees,” Chipley points out. “My cutters can cut anything from 6 in. in diameter on down.”
The loaders can be equipped with forks to move pallets of block, preformed catch basins or other materials. “When we’re laying pipe, we use them to shuttle the pipe to the excavators to place the pipe in the ground,” says Chipley.
Asphalt milling attachments are used to do prep work for parking lots; power rakes are used for dressing a site; pickup brooms and angle brooms are used to clean up after milling — the list goes on and on.
“Clearly, you can take one machine and three or four attachments and do several items with it,” Chipley states. “So to say that these [machines] are an important part of my fleet is almost an understatement.”
A Concrete Solution
Little convincing was required for Ruiz Construction Company, a concrete contractor based in Ottawa, IL, to switch from rubber tired skid steers to CTLs back in 2003.
“We always had wheels; it was all we ever knew,” says Jonathon Ruiz, project manager. Then, a skid steer broke down and the local rental rep suggested trying a CTL. “We didn’t think too much about it until we got in it, and then almost immediately we saw the advantages — everything from being so much more stable as a machine, to the pushing power, the lifting power, the grading advantages, the traction. I think it was within weeks after renting one that we traded our [rubber tire models] off for track machines.
“We had always had two Bobcats, and we switched both at the same time just because of the advantages,” he continues. “It cost more money, but the pros completely outweigh the cons. There really are no cons in my mind.”
Today, the company’s John Deere excavator and backhoe-loader, a finish dozer and a GOMACO curb and gutter machine are supported by a Bobcat T140 and a newly acquired Case TR270. The CTLs are used extensively in the company’s paving, pavement replacement and excavating operations, often freeing up larger equipment for other types of work.
“If our combination backhoe was on a jobsite, we’d be pushing piles of dirt. I still use it all the time, but I use it less for that type of purpose,” Ruiz explains. “The track machines are the first thing on our jobs and the last to leave.”
The newest CTL is commonly used for spreading and leveling CA6 gravel for pavement and concrete work. “The TR270 is the smaller of the Case machines. With these machines, you can save money buying a smaller model and get a lot more work done as opposed to the rubber tire machines,” Ruiz asserts. “They really blast through piles. And grading wise, with the tracks and how they float, they don’t really rut things up. When you backdrag, it comes out really smooth. If you have a good operator, you can drastically decrease your grading time.”
The tracks are beneficial on concrete demolition jobs, as well, providing a stable platform for lifting and loading chunks of concrete. “With the tracks, because they have so much more stability, you’re getting the maximum lift out of the machine,” says Ruiz. “We lift pretty heavy chunks of concrete. The tracks just hold to the ground. The hydraulic power will stop before the machine ever tips, so it’s nice for safety. When you’re loading trucks with a big chunk of concrete, you always feel stable.”
Then there’s the ability to power through challenging underfoot conditions. “They can go anywhere,” says Ruiz.
This proved especially crucial earlier this year, when the town of Ottawa experienced extensive Spring flooding. Ruiz Construction was one of the contractors volunteering to transport sandbags around the community. “The only machines that were hauling these sandbags on the pallets were the track machines. They were just plowing through the mud and flooded areas,” says Ruiz. “I was even surprised. I was floating on top of the stuff with completely loaded pallets of sand.”
Being able to access areas others can’t has enabled the contractor to take on a wider range of jobs. “I think without a doubt we do a lot more work that we could never do [with wheeled machines],” Ruiz states. “If you need an attachment somewhere, you can get it places where wheels wouldn’t let you.”
For example, on one job, a trencher attachment was needed in a remote location. “We had to go down really steep hills to get to the site and then climb back up,” Ruiz points out. “Instead of figuring out different ways to reroute and go way around a jobsite, we can get places a lot faster with tracks. It’s not that the attachments necessarily work better, but we can get the attachments where we need to faster and easier.”
Ruiz has become a firm believer in the value of CTLs, telling his contractor friends that the benefits make the investment well worth the extra expense. “They’re sometimes $10,000 to $12,000 more than a wheeled machine,” Ruiz acknowledges. “But I keep telling them, until you get one, you’re not going to realize that what you’ll get out of your jobs will far surpass the cost that you pay up front. You wind up recouping those costs faster than you think, and then making money off of it in the future.”