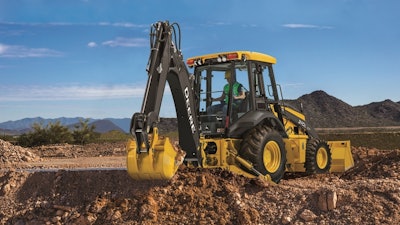
Since the onset of emissions regulations set forth by the U.S. Environmental Protection Agency (EPA), the complexity, cost and fuel usage of many machines have gone up. Several equipment manufacturers have made concerted efforts to lower the power ratings of their new models from 75 and 85 hp to 74 hp or lower, in a process referred to as de-rating.
Reducing the maximum power of a machine offers several benefits, including minimizing its aftertreatment needs to meet EPA Tier 4 Final emissions regulations. By doing so, the OEM lowers its production costs, and thus owning and operating costs, on top of improved fuel efficiency and reduced maintenance requirements.
“There are numerous reasons for reducing maximum power in a newer machine when compared to the one it is replacing,” says Craig Timmerman, product marketing manager - Engines and Powertrains, John Deere Construction & Forestry. “It could be... a result of a new technology that enables the same level of productivity, while still allowing the engine power to decrease. At John Deere, the reason for reducing horsepower has been to support our value proposition of productivity, uptime and low daily operating cost.”
Bobcat Company expanded its compact loader line to include the 74-hp S740 skid-steer loader and T740 compact track loader in its 700 frame-size class. This machine size is popular for the general contracting, landscaping and recycling market segments, which need the extended reach and lifting capabilities of the larger frame size but not the extra horsepower necessary for certain power-demanding applications like pushing or digging.
“The 74-hp machines can help minimize the initial investment and operational costs to the customer,” says Mike Fitzgerald, loader product specialist at Bobcat. “Customers needing a skid steer or compact track loader in [the 700 frame-size] category for heavy digging or pushing applications should consider the 75-hp and above loaders. These machines provide the performance needed for those tasks and will have extra aftertreatment systems to meet emissions requirements for that horsepower level.”
At Case Construction Equipment, the 580N EP backhoe-loader model was initially a result of focusing on the rental market. “Contractors that rent equipment are often looking for the most basic setups they can find for simplicity and cost,” explains Katie Pullen, brand marketing manager. “They need a machine to get on the jobsite and work efficiently without having to worry about explaining all of the bells and whistles to operators.”
Because the 580N EP is only 74 hp — as many models were years ago before everything shifted to larger, higher horsepower machines — it features a maintenance-free Tier 4 Final solution. The particulate matter (PM) catalyst built into its engine does not require a diesel particulate filter (DPF), or any aftertreatment, so there are no new maintenance practices or activities associated with the machine that renters have to learn.
“Similarly, first-time backhoe buyers and newer contractors will appreciate the lower cost of entry into the backhoe market,” says Pullen. “Many of the larger horsepower backhoes are designed with more features because they are targeted at the owner-operator who spends their whole day in that machine.”
Since not every contractor needs that level of functionality, the entry-level model features options a contractor can add to get the machine to where they want it to be.
Favorable Performance Choices
The best candidates for power reduction are equipment types that don’t spend much time operating at peak power. For example, if a loader’s maximum power needs are during bucket filling, and a new linkage design results in more efficient filling, then the maximum power can be reduced without any negative impact.
John Deere’s goal is to avoid any negative impacts when reducing maximum power on its equipment by favoring performance attributes. “For example, if gradeability is more important than operating weight, then the weight will be reduced to maintain gradeability performance. The most obvious difference, which isn’t necessarily a negative, is on the specification sheet showing a lower engine power,” says Timmerman.
“There is a bit of a stigma to the term ‘de-rating,’” says Pullen. “When a piece of equipment de-rates, it represents the machine performing at a rate lower than what it is capable of.” The core structural elements of the 580N EP are the same as Case’s full-featured models. “We’ve relied on the same hydraulic design on these machines as the higher horsepower backhoes and have not compromised structural strength in any way for the lower horsepower.
“Speed is the main sacrifice when looking at lower horsepower units,” says Pullen. “Contractors accustomed to larger horsepower models with more features will notice that these machines don’t have the full features they are familiar with. But that is to be expected anytime you compare a 90-hp machine to a 74-hp machine, or a 15-ft. backhoe to a 14-ft. backhoe.
“Having said that, our standard 580N backhoe at 90 hp and the 74-hp 580N EP have the same backhoe breakout forces and lifting capacities — two of the most important operating factors,” Pullen says.
How is This Accomplished?
John Deere has several models in it loader, backhoe and crawler product lines that are able to reduce maximum engine power. “In most cases, [de-rating] has been accomplished due to system efficiency gains,” explains Timmerman. “The efficiency of our hybrid loader drivetrain system, for example, has enabled the maximum power to be reduced.”
While actual de-rating calls for an existing piece of equipment to be modified to lower its maximum power output, in reality, many manufacturers are designing simpler pieces of equipment specifically to leverage a 74-hp workload and adding them to their existing product lineup.
Bobcat designed its 74-hp skid-steer and compact track loaders to retain their lifting abilities. “The 74-hp compact loaders have a good balance of engine horsepower and auxiliary hydraulics. For instance, the 74-hp S740 and T740 loaders have a 30.5-gpm high-flow option, while other larger horsepower machines in the 700 and 800 frame-size have 37.5-gpm high-flow systems. The lower gpm high-flow option allows for a more balanced machine with the 74-hp engine,” says Fitzgerald.
“Customers in landscaping, general contracting and recycling applications who need a machine for dimension and weight capabilities, but do not need the extra horsepower, are more likely to use the 74-hp machines. Tasks may include landscapers who are lifting pallets of paving stone or sod; general contractors who are unloading commodities and providing site cleanup; or recycling centers that are using loaders to load sorting machines and lift bales of materials,” Fitzgerald says.
Case has also added lower horsepower models to its existing compact equipment product offerings. It’s able to reduce the equipment’s horsepower without sacrificing performance and productivity through the unit’s hydraulics and structure. The footprint and structure of the machine are still the same, although a few hundred pounds lighter, so the physical design elements that effect its performance are the same. The hydraulic system features the same pumps and controls as the comparable higher horsepower models.
“In addition to our 580N EP backhoe, we’ve kept certain skid steer, compact track loader and compact wheel loader models below 74 hp in order to implement the same maintenance-free Tier 4 Final solution — the particulate matter catalyst,” says Pullen.
The End Goal
At the moment, the efforts of reducing maximum power below 75 hp seem to be long term in nature. Finding system efficiencies to allow a machine to be specifically created for a tailored application will allow OEMs to offer their customers the most cost-effective solution without overcompensating for power needs that the customer’s application does not warrant.
“We feel our customers will continue to ask for machines that offer lower daily operating cost. As long as this demand remains, we will continue to look for opportunities to provide more efficient machines to support this need,” says Timmerman.
Case, too, sees its lower horsepower equipment development as a more permanent, long-term solution to provide its customers with a broad spectrum of options to best fit their needs — especially for the rental customer or the first-time backhoe buyer who doesn’t need a full-featured, high-horsepower model. “It provides them with a solution that is more cost effective, both in initial purchase price and total cost of ownership,” says Pullen.
With even further emission reduction rumors on the horizon, further system improvement to gain productivity without increasing horsepower will continue to be evaluated by all OEMs. Through a focus on efficiency gains in existing onboard systems such as a machine’s hydraulics, as well as continued research and development on simple and intuitive technologies, OEMs will be able to provide contractors with cost-effective equipment solutions that make the most sense to them for the specific application at hand.