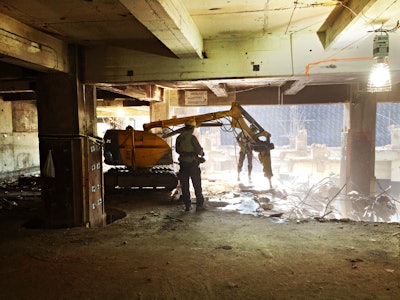
When it comes to handling high-profile projects, Baltimore-based demolition contracting firm, The Berg Corporation, wrote the book. In this case, its task centered around one of the biggest, most widely-read books of all time as it prepared to clear a path for the much-publicized Museum of the Bible in Washington, D.C.
The Museum of the Bible is an $800 million endeavor funded primarily by Steve Green, president of Hobby Lobby. Scheduled to open to the public in fall 2017, the museum will sit approximately two blocks from the National Mall. The old train loading dock on 4th Street Southwest will serve as the museum’s main entrance, flanked with tall bronze panels and a 40-ft.-high stained glass piece. Inside, visitors will enjoy a rooftop ballroom and auditorium, dine on Biblical-themed meals in an on-site restaurant, or walk through a child-focused Noah’s Ark experience filled with videos and holograms. The floors will display one of the world’s largest collections of Torah scrolls and fragments of the Dead Sea Scrolls. Bibles of the distant and recent past will also be on display, from a portion of the Gutenberg Bible, to Bibles used by Babe Ruth and Elvis Presley.
Following months of study and collaboration between Berg Corporation and Clark Construction, the project to turn a 1920s refrigeration warehouse and neighboring buildings into a 430,000-sq.-ft. display case for Green’s trove of nearly 44,000 Biblical pieces was started. Clark managed the pre-construction contingent and Terence Anderson, vice president of estimating for Berg Corporation, helped take it from there.
Making Light Work of Selective Demolition
The team’s mission included taking out every other floor of the Washington Design Center, adding 5 ft. of additional depth to the basement and removing the roof, plus demolishing the 1982, 50,000-sq.-ft. Hyphen Building, sandwiched between the Washington Design Center and the Washington Office Center. The Washington Office Center also demanded extensive structural work on the underground parking area and foundation walls.
The way Berg’s management team saw it, there were two ways to tackle the project. They could use skid-steer loaders with hammer attachments along with operators on handheld jackhammers and rivet busters, or they could bring in lightweight, remote-controlled demolition equipment to do the heavy hitting, as well as a small skid-steer loaders to quickly remove the debris.
The first option carried the risk of exposing employees to ongoing fall hazards and poor air quality, and exaggerated labor costs. The use of remote-controlled demolition equipment would greatly reduce the risks to employees, dramatically decrease labor costs and bring the schedule into line with the opening of the museum.
Consequently, Berg chose remote-controlled Brokk demolition machines for the bulk of the selective building demolition. The machines can be equipped with numerous attachments, from breakers and steel cutters to buckets and drills. Attachments are mounted on a three-part arm that provides smooth precision with optimal power and reach. The lightweight, compact machines deliver the needed hitting power, yet some models measure barely 2 ft. wide.
[VIDEO] How a 1-Ton Demolition Robot Can Outwork a 3-Ton Excavator
Brokk machines have been prominent in Berg’s equipment lineup since 1999, and the museum project presented the opportunity to add three additional units to the fleet. “The floor load would not allow mini-excavators, so this was really a problem that could only be solved by a Brokk robotic demolition machine,” says Christopher Trendell, vice president of operations at The Berg Corporation. “There is a dramatic amount of variance in the construction of both buildings, and both of them are extremely light loading capacity. The Brokks offered the heavy hitting power on a lightweight carriage.
“Using the Brokk machines in this application was the most efficient and productive means," Trendell adds, "and it certainly reduced labor costs by decreasing the number of employees needed, while also reducing the duration of our time on the job."
Step-by-step and Floor-by-floor
Kevin Durbin, a supervisor for The Berg Corporation, chose a half-dozen Brokk models from the company's fleet to complete each phase of bracing and demolition. His choices focused on getting the strongest hydraulic capabilities possible for each weight-restricted area. For example, the 3,500-lb. Brokk 160 broke holes into the building’s support columns so steel plates could add reinforcement. The 2,200-lb. 90, an older model in Berg’s fleet, handled the weakest areas, such as Hyphen Building floors that were made with smaller rebar and wire mesh.
The team first gutted the warehouse and Hyphen Office Building. Steel bracing plates, tubular steel and steel rakers were then installed at perimeter and interior columns to shore the Washington Design Center. Next, they were ready to tear the roof off to increase the height of the main, 310,000-sq.-ft. warehouse. From there, they worked their way down the eight-story building, demolishing every other floor to give the museum more open space than the existing 12-ft.-high ceilings allowed.
A crane lifted tracked Brokk 260s and 160s and skid-steer loaders to the eighth floor to begin the project. The Berg team used both Atlas Copco breakers and Darda concrete cutters on the robotic demolition machines, which they maneuvered with wireless remote control as they demolished their way through 5,000-sq.-ft. sections. The remote-control feature allowed Berg's team to operate the machines from wherever conditions were safest — either right next to the machine or several feet away. Skid-steer loaders quickly pushed the debris down a chute to minimize the weight on the disappearing floor.
The machines were shifted to the sixth floor, tackling the columns and beams first. They saw-cut slots on the opposite sides of each interior column, added steel bracing, and then repeated the process on the other sides so the columns could be freestanding. The process was repeated on each even-numbered floor, covering 65 interior columns spanning anywhere from 2.25 to 9 sq. ft. Once the columns were braced and the floor shored, it was back to demolishing the reinforced 8- to 10-in.-thick concrete floors.
“The Brokk units helped us immensely in the demolition of the structure by providing extra precision,” Durbin said of the Hyphen Building, which came down 6 in. from the larger Design Center. “The breaker attachments allowed us to maintain control of the equipment and demolish what we needed gone without damaging the warehouse.”
A couple of 6,700-lb. 260 machines also worked to remove the warehouse’s reinforced floors. The 260 offers 19 ft. of reach from its 5-ft.-high, 3.9-ft.-wide body, while the breaker exerts 450 ft.-lbs. of energy to break the slabs. The 330 electric model equipped with a breaker generating 630 ft.-lbs. broke out the basement’s concrete floor, pushing it 5 ft. lower to make room for new mechanical equipment and ease underground parking.
While floors were removed, the windows remained, a notable example of Renaissance Revival architecture. Retaining the windows helped the contractors keep some of the weather out as the project began during one of Washington, D.C.’s coldest winters on record, but it also made the electric-over-hydraulic demolition machines the only practical solution. The units are powered by 480-volt, three-phase electric motors.
“There were no fumes, which was a big deal. Since we were leaving the windows in, we needed to ensure there were no air quality issues, especially when we were working in the basement,” Trendell comments.
Easy Sorting for Recycling
In less than four months, The Berg Corporation completed the multifaceted project, all while recycling a massive amount of material. The team sorted concrete to send to a remote crushing facility and steel to ship to a scrapyard for sizing and processing. The plan resulted in over 90% of the building contents (by weight) being recycled.
The team used the same small fleet of equipment due to the ease of changing out attachments. “The Brokk unit provides an easy and fast option for sorting through concrete and rebar, especially when compared to more traditional methods, such as handheld tools,” says Andrew Laurimore, general superintendent for The Berg Corporation. “It has powerful hydraulics and the wide range of arm movement helped our efficiency with moving the materials. The remote controls also kept our operators away from any high-risk areas.”
As a whole, the remote-controlled machines proved themselves the right choice for the various aspects of the job. “My crew attacked the overall project faster, and could work longer than any person on a handheld tool, by using Brokk equipment,” Trendell states. “It was certainly the most productive choice for this project.”