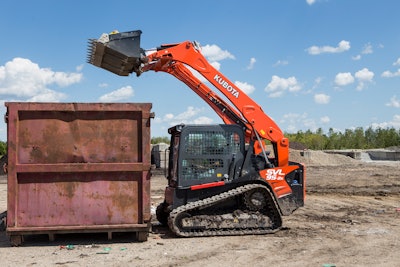
Manufacturers have concentrated R&D resources to perfecting the performance characteristics of vertical lift skid-steer and compact track loaders (CTLs). In many cases, this has resulted in increased durability and digging performance to compliment the greater lifting capacity and height these machines afford compared to their radial lift counterparts.
“In the past, the saying was that the radial lift is generally a better option for excavating and grading. And if jobs typically require working above eye level, a vertical lift would be the better option,” says Lars Arnold, global product manager, skid-steer loaders, Volvo Construction Equipment. “However, that is no longer true. Vertical lift is the way to go to be able to work in various different applications with a skid steer all year long. They are great for grading with a dozer blade, bucket and fork applications, as well as for high-performance hydraulic-driven attachments.
“Radial lift offers more reach at mid-range height compared to a vertical lift, which can reach higher with more stability,” he continues. “Digging is an application done mostly at mid-range height or lower, which is why the radial lift is traditionally considered the best option. Also, because radial lift loaders have fewer maintenance and wear points and a reputation for durability, they’re more commonly used for tougher applications, like digging. These traditional views are being challenged as the trend is clearly toward vertical lift machines since they are the better choice for being a multi-tool carrier.”
Vertical lift loader linkage designs have progressed significantly. “The design of the lift arms today are significantly different than what has been available from Bobcat from years past,” says Mike Fitzgerald, product representative, Bobcat. “In the early days of compact equipment — skid-steer loaders in particular — the radius lift path machine was designed to do certain work and the vertical lift path did a little bit different job.”
The simplicity of the radial lift path machines translated into increased durability, which made them well suited for digging applications, while the vertical lift path machines were targeted more toward lift and carry applications.
Today, the durability and longevity of radial path and vertical path machines is comparable. Tools such as CAD and finite element analysis have made it possible to isolate stress and improve the designs. “The structural integrity and reliability, durability of the lift arm/frame configuration have made it so the customer doesn’t have to take that into consideration in the purchasing decision anymore,” says Fitzgerald.
The Performance Gap Narrows
In many cases, the performance gap has also narrowed. “If you optimize the tilt cylinder locations, the pivot points, then the breakout forces are similar from one machine to another,” says Fitzgerald.
A key advantage to the vertical lift machines is that the load travels straight up and down with the loaders arms instead of swinging out in an arc, which keeps the center of gravity close to the machine. “Whatever you can lift at the very bottom on the stroke of a vertical lift you can typically take all the way to the top,” says Gregg Zupancic, product marketing manager, John Deere. With a radial lift machine, you might be able to pick the load off the ground, but as the load swings out slightly in the arc of the lift arms, you can lose the center of gravity and are more likely to tip forward. “So a heavy load at truck bed height may make you unstable.”
Many of the new vertical loader designs strive to achieve the durability and breakout forces of the radial lift models.
“Kubota is careful to place the loader hinge pivot points in precise locations to distribute the load on the main loader chassis much like a radial lift loader,” says Jeff Jacobsmeyer, CE product manager, Kubota Construction. “This placement gives the performance characteristics of a radial lift with the benefits of a vertical linkage. Large bucket pivot pins in the front bucket coupler and loader arms evenly distribute the load, which ensures long life when used in severe-duty applications.
“Machine lift performance and overall balance is critical in today’s competitive market,” he comments. “Kubota only manufactures a vertical lift design, so it is imperative that each model delivers the advantages of a vertical lift loader, yet performs to the lasting durability demands and performance of a typical radial design. Kubota’s unique vertical linkage design tucks in the rear and sides of the unit when retracted, allowing these models to push and dig more like radial machines.”
Case Construction Equipment counters that it is difficult to beat the simplicity of a radial lift machine. “The durability of the vertical lift design has definitely improved with the newer designs,” says Debbie Townsley, product marketing manager, skid-steer loaders and CTLs. “However, the simplicity of the radial design offers inherent durability advantages over the vertical style. From a customer’s perspective, the higher number of parts on many vertical lift loaders can potentially lead to more component failures.”
“Vertical lift machines do tend to have more wear points and therefore more maintenance needs. But speaking for Volvo skid-steer loaders, durability is always a top consideration in our development process, no matter the lift design,” says Arnold.
Loader Size Matters
The percentage of machines with vertical lift correlates closely with machine size.
“Smaller machines tend to be more entry level. By nature, customers want them a little lighter,” says Zupancic. “If you look at the smallest size machines, maybe 60% are radial lift and 40% are vertical lift. Then you get into the medium size and it is more opposite — you have 60% to 70% vertical and the remainder radial. On the largest machines, they are all vertical lift.” In this case, the machines are already heavy, so adding the extra structure to achieve higher lifting or better breakout forces makes sense.
Vertical lift is popular with large- and medium-frame loaders. “The entire industry has moved more toward the vertical lift path machine because customers see value in spending additional money to get the extra rated operating capacity (ROC), with no trade-off in durability,” says Fitzgerald.
“There are various reasons for the shift to more vertical loader models,” says Townsley. “One of the main reasons for the shift to vertical is the growth of the loader market to larger machines. The largest size loaders almost exclusively use vertical lift designs. Customers running larger loaders generally want the lift and carry performance of a vertical design. The vertical lift design particularly helps in the loading of dump trucks and placing materials at elevated heights.”
Arnold agrees, adding, “The lifting capacity is the reason larger skid-steer loaders tend to be vertical lift. Contractors want to be able to lift more with the larger machines. A vertical lift can also make it easier to work in confined spaces because of its straighter up-and-down path.”
Boom Geometry Separates the Players
Boom geometry is a major point of differentiation between all of the loader manufacturers who offer a vertical lift machine. A lot of effort goes into the boom design, especially where the cylinders connect to the boom and how the boom connects to the machine. “Typically, every competitor has a patent on that design. There is a lot of work that goes into that and you cannot exactly replicate someone else in the marketplace,” says Zupancic.
Manufacturers have to make deliberate trade-off choices when designing the boom geometries. “Every manufacturer has a different priority,” acknowledges Zupancic. Engineers study the kinematics of the boom design. “That is where all of the cylinders might connect, what portion of the boom it might connect to, the angle of the cylinder.” This allows the OEM to tune specs such as breakout force.
“On the large frame, we did push the envelope on the boom breakout,” says Zupancic. “That is the lifting force of the boom. The angle of the way the boom sits on the frame, the pivot points that the cylinders connect to and the linkage connects to were modified slightly so we could pick up another 1,000 lbs. of boom breakout force/lifting power.”
John Deere recently changed the vertical lift design on its large-frame G Series loaders. “One of the key drivers for the change of the vertical lift was related to getting more height to hinge pin, or lift height,” says Zupancic. “We were previously around 10 ft. and we changed the design of the large machines to get up to 11 ft. today.”
This change required a different lift pattern arc for the loader arms. “In the past, the lift pattern basically went straight up and then at full height it would move slightly away so you could better reach into a dump truck,” Zupancic explains. With a higher reach, this approach would have required additional counterweight. “We didn’t want to add a bunch of extra weight to the frame of the machine to be able to counter that. Typically, our strategy was to have really good breakout force with our bucket at the lower heights.”
All manufacturers have their own lift arm designs and geometry. “Volvo differentiates itself with the unique single arm on both vertical and radial lift machines, providing side door entry and eliminating the need to climb over attachments to enter the cab,” says Arnold.
Some vertical lift designs can restrict visibility to the rear of the machine. “There are manufacturers that have a large portion of the linkage exposed very high, which can hinder rear operator visibility,” says Jacobsmeyer. “Kubota uses a lower profile integrated linkage system that provides a desirable front to rear weight ratio, resulting in excellent loader performance as well as visibility. The lower placement of the vertical linkage provides outstanding rear and side operator visibility throughout the loader lift and lower cycle.”
Vertical Lift Is More Complex
The additional linkage providing the vertical geometry does come with incremental cost, but that varies with designs among the manufacturers.
“Initial costs are higher when manufacturing a vertical lift machine simply because more materials and labor are involved in production,” notes Jacobsmeyer. “The additional pivot pins, fabricated loader linkage and assembly labor add to the cost of the loader during manufacturing.”
Depending upon the manufacturer, the increased cost for vertical lift can be negligible. “When you move up to a vertical path loader, there are performance benefits that justify the additional investment,” says Fitzgerald.
Radial Lift Not Going Away
Smaller machines and certain applications will continue to favor radial lift. “Radial lift styles are generally offered on the more price sensitive smaller loader models,” says Townsley. “However, in applications that require a lot of digging, there are larger radial lift loaders on the market to meet those specific customers’ needs. For example, Case offers the SR270 model that provides an ROC of 2,700 lbs. for customers that want both extra power and lift capacity in a radial lift machine.”
The demand for radial lift models isn’t going away. “There may be a bit more movement toward vertical lift loaders in the market, but there are still applications where it is more advantageous to use a radial lift loader,” says Townsley. “For certain applications, the design characteristics of a radial lift-style loader still have a clear advantage over a vertical model.”
The radial lift machine is better suited for loading and unloading off small vehicles or platforms, such as low-sided trucks or the back of trailers. “As the travel path is more similar to an arc, this configuration provides greater reach at mid ranges, which makes it ideal for loading and unloading off smaller vehicle platforms, such as lower-sided trucks or flatbed trailers,” says Townsley.
Many manufacturers still offer a radial loader option for digging in tight spaces. “Radial lifts are really good digging machines,” says Zupancic. “The bucket at the bottom is really close to the machine so you get good leverage to pry. There is less linkage in general, so there are fewer bushings to maintain or replace. There are half the grease zerks of a vertical lift machine. You are also going to get better visibility with the radial lift. A customer may choose a radial lift simply for the visibility. They tend to be compact. The way the radial lift works is if you bring it up, the bucket is the highest point. So in indoor applications, being that it is more compact, you have better visibility and the highest point is the bucket, which is out if front of you so you can see it better. It may be a better solution for those applications vs. a vertical lift.”
The radial lift geometry has its advantages. “People who stay with the radius path loaders are operations where they may be ground engaging or backfilling foundations, as a radius path will reach out farther at a lower height,” says Fitzgerald. “There are certain applications that a radius path machine still does the job a little different and meets the needs of a specific set of customers a little better.”
Tandem axle landscape trailers often require lift heights between 30 and 50 in. “With a typical landscaping trailer, you are going to reach a little farther onto the bed with a radius path loader than with a vertical path loader,” says Fitzgerald. “Conversely, when you load a truck or hopper with high sides, the vertical path loader is going to reach in farther at those upper heights. What you are doing and how you have your jobsite set up will determine which machine suits your application best.”