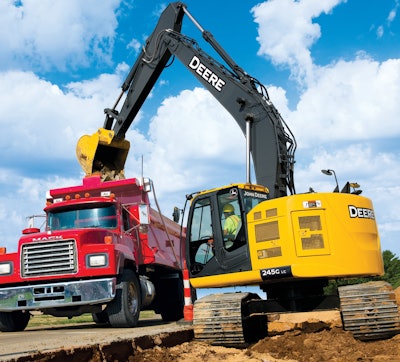
An excavator operator 20 years ago might have put little thought into how much fuel a machine was burning or if it was delivering optimum performance. There was a job to do and it usually had to get done as quickly as possible.
The landscape has changed. Fuel cost has gone up dramatically over the last couple decades, as has the cost of equipment, thanks in part to the evolution of low-emissions engine technology.
Yet, even as implementation of this technology has contributed to higher acquisition costs and potentially higher ownership costs, operating costs are actually lower in some instances due to better fuel economy and more efficient systems. Just how owners and operators are able to reap these important benefits varies from manufacturer to manufacturer.
A Design Evolution
“As with any change in regulations, the spotlight has been focused on the new systems used to meet emissions regulations,” says Ken Gray, Caterpillar global excavator product manager. “Although the operation of the technology Caterpillar is using to meet the Tier 4 Interim requirement is completely transparent to the operator, the real story is the number of valuable changes the Cat E series excavators incorporate.”
The improvements, he notes, are designed to reduce operating costs and maximize value to customers. Among them are a more powerful engine that consumes less fuel, a redesigned hydraulic system that greatly increases machine efficiency, a redesigned operator environment focused on operator safety and comfort and improved ground level serviceability.
Other OEMs relate similar improvements in excavator engines, hydraulic systems and other key components. “The majority of Komatsu’s Tier 4 Interim hydraulic excavators employ Low Speed Matching technology,” says Bruce Boebel, senior product manager, Tracked Products, Komatsu America Corp. “The technology uses higher displacement hydraulic pumps so engine speed can be reduced to save fuel with no reduction in performance.”
The company also uses Variable Speed Matching technology that regulates engine speed and power to optimize hydraulic flow. “This system is canceled when full power is required by the operator. This saves fuel for low to high duty cycle applications,” Boebel points out.
Doosan excavators feature a split cooling system that allows the oil cooler and radiator to operate independently. “The design optimizes the hydraulic system and engine temperatures, even in severe working conditions, and provides a 15% increase in cooling capacity,” says Aaaron Kleingartner, Doosan marketing manager.
A variable-speed cooling fan on the oil cooler of the DX300LC-3 to DX530LC-3 and on the radiator of the DX420LC-3 to DX530LC-3 adjusts fan speed as required by the demands of the excavator. “In tough, difficult applications, the fan runs faster, and in lighter duty applications, it runs slower to increase efficiency and reduce noise,” Kleingartner explains. “A reversible radiator fan can be set to automatically reverse to assist in keeping the cooling system clean in extremely dusty applications.” This feature is standard on the DX420LC-3 to DX530LC-3 models.
John Deere is also striving to make new emissions standards as seamless as possible, says Mark Wall, excavator product market manager. “For our customers, we want emissions to be a non-event,” he states. “The same goes for other new technologies built into the excavators.”
The company has accomplished this goal in part by employing an engine, hydraulic management system to control an excavator’s functions and operations. “The system does the thinking for the operator,” says Wall. “It keeps equipment operating at optimum performance no matter what the application is.
Different Modes of Thought
Both John Deere and Caterpillar take transparency all the way from emissions to the excavator’s overall operation. Neither OEM incorporates work modes into their machines. Instead, they use only power modes that allow operators to match fuel consumption to job requirements. Both offer three power mode levels: high power mode, a standard or normal mode and an economy mode.
According to Wall, “If operators are facing a deadline and need optimum power, then the HP mode would be appropriate. Conversely, if fuel economy is a priority, then the mode of choice would be the E mode.”
Caterpillar E Series excavators feature software that manages operation. “The E Series excavators feature isochronous speed control to maintain a constant speed, regardless of load, to improve fuel economy,” says Matthew Delzell, machine engine senior account manager. “Additionally, automatic engine speed control is built into the engine software to reduce engine rpm when not under load to help save fuel.”
While these two companies subscribe to the “keep it simple” axiom, OEMs such as Komatsu and Doosan have chosen to give operators more control over an excavator’s functions and operations.
Komatsu’s Dash 10 excavators, for example, provide six working modes. The P (Power) mode provides maximum power for high-production, focused applications and the E (Economy) mode is for light work. Boebel describes the other four: “When a hydraulic breaker is used, a one-way flow breaker mode with adjustable flow rate can be selected. Additionally, the L or Lift mode increases hydraulic pressure for applications requiring improved lifting performance such as moving trench boxes. Lastly, two additional attachment modes, which are versions of the P and E modes, match hydraulics to attachments with low-flow requirements, such as a sheepsfoot roller compactor.”
Doosan excavators come with four power and four work modes. The four work modes are for digging, lifting, breaker (one-way auxiliary flow) and shear (optional two-way auxiliary flow) applications. Economy, standard, power and power plus define the power modes.
“The power modes allow operators to manage the balance of fuel consumption and machine power based on their working conditions,” says Kleingartner. “A one-touch power boost button also provides a momentary increase in hydraulic power to break through hard ground and other tough digging conditions.” He notes that the power plus mode improves efficiency by 10% over the previous machines’ power mode setting, and the new optimized standard mode improves efficiency by 12% over the predecessors’ standard mode.
“Auto idle and auto downshift also contribute to increased productivity and fuel savings,” Kleingartner adds. “Auto idle automatically returns the engine to idle when machine functions are not used for a few seconds, reducing noise, improving jobsite communications and saving fuel. Auto downshift reduces the hydraulic flow to the drive system when turning, pushing and maneuvering to improve machine responsiveness and controllability.”
Cost Benefits
Across the board, OEMs see cost benefits for the end user in these high-tech solutions.
“The E Series excavators maximize productivity and fuel efficiency, while delivering the reliability and durability customers need and expect,” says Gray. “There’s no question that our machines are more efficient today from two perspectives. They deliver better fuel economy in gallons per hour and gallons per yard. In other words, they can move more dirt today than their predecessors with less fuel consumption.”
Kleingartner believes the new designs and technologies can help offset the cost increases from the implementation of low-emissions technology. “With proper training, operators can be the true differentiator to the bottom line,” he states. “They now have technologies at their fingertips that will allow them to adjust their excavator’s performance to fit their task-related needs.”
Boebel agrees, adding, “Educating operators to choose the most effective excavator working mode and the OEM’s ‘behind the scenes’ technologies will help improve on the job performance and reduce operating costs.”