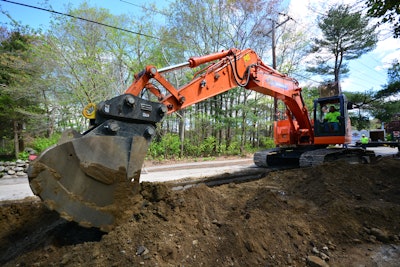
If excavating, grading and site preparation drive the demand for your construction business, then you know that your work could not be done without the right crawler or wheel excavator. You depend on these machines, and attachments, to help you bid accurately and work on multiple types of projects simultaneously.
Whether you subcontract your services to larger firms or specialize in a particular segment, having the proper equipment can help form the basis for your personnel decisions. And well-chosen equipment can give you the confidence to expand your services and even branch out to surrounding communities.
Obviously, there are several factors that will influence your success in excavating, grading and site preparation, but most of them typically point back to selecting the proper excavator. As activity continues to pick up in nearly every construction application, Shane Reardon, Doosan excavator product specialist, says there’s a growing sense of urgency to make sure that the machines you choose can tackle your projects and stay within your equipment budget.
“Since the recession ended, we’re seeing more excavators being sold into construction year over year, and each application area is growing,” Reardon says. “Regardless of the size of a construction firm, there some key factors that apply to any acquisition to make sure you can achieve profitability and keep your costs of ownership manageable.”
According to Reardon, the best approach to selecting a machine for excavating, grading and site preparation includes the following five tips.
1. Top Jobs
It seems that land clearing, excavation and grading is required on nearly every type of construction project. The single most important factor to consider in the selection of an excavator for these types of applications is what you want to accomplish with a machine. Selecting a machine to perform excavating functions only can be very different than it is for site preparation.
For example, a reduced tailswing model — ideally suited for utility installations that require digging and compacting trenches in tight spaces — is not the same solution needed for clearing and grading a 25-acre tract of land for a housing development that also requires installation of a large retaining wall. The need to perform in these applications requires a more versatile machine than just an excavator with a bucket. Rather, you’ll need a machine that can perform multiple tasks to prep a piece of land for clearing, expansion, new construction and installation.
2. Productive Configuration
Generally, the most important step in selecting the right size of a machine for excavation is determining daily digging production targets. Since the most common setup for an excavator is being outfitted with a bucket, the next logical step is to match the size and capacity of a bucket to the density of the heaviest material you expect to handle. Then, select the machine that can properly accommodate the bucket to routinely excavate that load.
An excavator configured to fit its jobsite space is another key consideration. “We’re seeing reduced tailswing configurations gaining popularity as more aging infrastructure needs replacement or updating,” Reardon says. “Work space in some cities can be very limited vs. new construction and you may not be able to close down lanes of traffic for a conventional tailswing machine.”
3. Smart Efficiencies
Like many construction machines, excavators are getting smarter. As the market expands with new models, its gaining machines with the electronic intelligence, allowing fleet managers to remotely monitor equipment using machine to machine communication, or telematics, some of which are offered with complimentary subscriptions. These systems put more information in the hands of owners and operators to help them efficiently manage maintenance scheduling and better monitor operational data and make recommendations to operators to improve machine productivity.
Innovations are also aimed at improving the communication between the engine and hydraulics for greater work group efficiencies and fuel economy. Machines designed with variable-speed control technologies reduce engine rpm during low workload requirements such as the swing portion of a dig cycle. This reduces the total energy required to perform a task and can measurably improve fuel efficiency. With pump torque control, an operator can efficiently match a machine’s hydraulic pump torque and engine response to the task, preventing engine overload and excess fuel consumption.
4. Attachment Versatility
Another key to proper selection of an excavator is the investment in a quality attachment connection system, such as a quick coupler, which is optional on most manufacturers’ machines. Some industry experts estimate that a quality automated coupler on an excavator can save owners up to 25% of their total machine operating time compared to direct-mount attachments.
Couplers make it handy to change attachments, such as swapping a regular ditching bucket for a grading style bucket for grading applications, or changing buckets to match trench width requirements. If you only think of an excavator performing heavy digging, you may be missing an opportunity to fit it with attachments such as a breaker for demolishing existing structures and material, a grapple for land clearing, a trenching bucket to dig foundation footings or a plate compactor to finish trenches. If daily projects require the consistent use of two-way auxiliary hydraulic flow attachments like hydraulic clamps and tilting buckets, it’s important to make sure a machine can be fitted with the proper hydraulics to meet your needs.
5. Transportation Logistics
Moving a machine from site to site may be the norm in some excavating, grading and site preparation applications. If you anticipate that an excavator will need frequent transport, accurate cost estimates should be included in your purchasing evaluation. Those considerations typically involve a determination of whether a trailer needs to be upsized or downsized to match the machine, or if there are more costly travel permits required for heavier excavators.
It’s also important to determine whether you have the proper hauling truck in your fleet.
“In mining applications, a machine is likely delivered to a work site and will live its whole life in one location,” Reardon says. “But if you’re moving that machine around the countryside to various construction sites, it needs to be matched to an appropriate-size trailer and be permitted to meet the area’s hauling regulations, which vary widely by state.”
Reardon also points out that mobility within a jobsite or on finished surfaces such as concrete and asphalt can be increased by operating wheel excavators that are designed to provide an alternative when a machine needs to routinely travel between tasks.
Provided by Doosan Infracore Construction Equipment America.