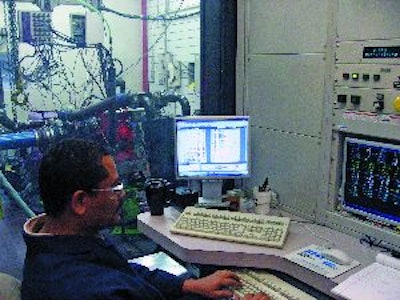
It is a dynamic environment for anyone involved in the manufacture or use of diesel-powered equipment. The Environmental Protection Agency (EPA) has been tightening the noose around diesel emissions, with an emphasis on NOx and particulate (PM) matter reduction.
The regulations are phased in over time on a Tier system based upon engine horsepower ranges. (See Table 1 for Final Tier IV implementation.) "Generally speaking, the higher the horsepower, the more stringent the emissions regulations and the more technology needed," says Doug Laudick, manager of product planning, John Deere Power Systems.
In the past, the implementation of each tougher set of standards has resulted in more efficient engines. "Power and productivity generally improved from Tier II to Tier III," says John Bartz, wheel loader and articulated hauler product portfolio planning, Volvo Construction Equipment.
Laudick agrees, noting, "When John Deere transitioned from Tier II to Tier III, most engines realized significant performance gains."
The final verdict on whether Tier IV will continue this trend has not yet been determined. One factor that could influence performance is the mandated move to ultra-low-sulfur diesel (ULSD) fuel, which typically has a lower British Thermal Unit (BTU) energy content.
"As we move to ULSD fuel, we will all see the resulting fuel consumption increase," says Bartz. "Volvo is working with the available engine technologies to reduce this impact and improve overall efficiency. Along with engine technology, various machine systems are also being looked at to improve efficiency."
Cummins has already announced the technology it's going to use to meet Interim Tier IV regulations and has been testing these products, according to Jennifer Rumsey, technical project leader, Cummins Inc. "The 174- to 751-hp product range will maintain or increase power outputs compared to Tier III," she states. "Fuel efficiency will improve by up to 5%, depending upon rating and duty cycle."
Similarly, John Deere expects to offset any performance penalties for the ULSD. "While the performance of our Interim Tier IV engines has not been finalized, we anticipate performance and fuel economy will be similar to Tier III while meeting the more stringent Interim Tier IV emissions regulations," says Kevin Resch, manager of product planning for Tier IV.
Influence of on-road technology
The current generation of on-road diesel trucks provides a pretty good glimpse of what you can expect to see in terms of technology to meet non-road Tier IV regulations.
"The same technologies used for on-highway engines will continue to trickle down into non-road products," says Resch. "However, one of the biggest challenges is the rate at which these technologies - originally developed for on-highway use - must be adapted for non-road use.
"The time between adoption of a new technology for on-highway engines and its use in off-highway applications has continued to decrease," he continues. "Off-highway equipment often works in harsher, more varied environments. Additional development time is required to make on-highway technologies suitable for off-highway applications. Ensuring the robustness of these technologies for off-highway use will continue to be a challenge through Final Tier IV."
Rumsey agrees the solutions must be customized to meet the unique needs of the off-road environment. The Cummins particulate filter serves as an example. "We considered the high shock loads, angularity and space restrictions in the off-highway environment," she asserts.
Moving to Tier IV
The step from Tier III to Interim Tier IV will require new technology in the form of aftertreatment devices - catalyzed diesel particulate filters (DPF) that will replace conventional mufflers. Some companies will continue to build on Tier III solutions, while others are coming up with unique solutions to address Tier IV.
"Volvo, in large, utilized EGR to address the Tier III challenge," says Bartz. "There are a number of technologies being considered for Tier IV, one of those being aftertreatment.
"If DPF technology is applied off-highway, there is one significant difference," he points out. "That difference is the operating signatures (duty cycle) of the different applications. The DPF needs to regenerate to get rid of built-up soot, and the specific machine operation may not generate the required temperature to achieve this. A regeneration strategy must be developed to handle scenarios where machines are lightly loaded and do not generate significant exhaust temperatures."
Cummins' Interim Tier IV off-highway solution has been leveraged from the proven technology it is using for its on-highway solution. Previously, Cummins used an in-cylinder solution for its Tier III off-highway engines. The 174- to 751-hp QSB through QSX engines are now moving to EGR with a catalyzed DPF.
"These engines will also include use of Cummins Variable Geometry Turbochargers (VGTs), advanced electronic controls and high-pressure common rail fuel systems," Rumsey explains. The VGT is a significant contributor to increased performance. "It improves the transient response."
The crankcase filter has also been designed to eliminate escaping blowby gases, oil mist and droplets. "You either need to use closed crankcase ventilation or you have to count the emissions from the crankcase in the total engine emissions," says Rumsey.
Systems integration has proven key to Cummins' Interim Tier IV solution. "Cummins makes the components in-house; it does not have to rely on outside suppliers," Rumsey states. This means it has the ability to tailor the fuel injection, turbocharging, filtration and aftertreatment systems to compliment one another.
Cummins continues to evaluate several NOx-reduction technologies to meet Tier IV Final, when permissible NOx levels will be near zero.
John Deere has used similar technologies as it has improved the performance of its emissions-compliant engines. "The most noticeable innovations utilized to move from Tier II to Tier III were the addition of cooled EGR and VGT," says Resch. "These technologies will continue to be part of the solution for Tier IV."
For Interim Tier IV, the most noticeable changes will be to engines with power ratings 175 hp and greater. "These engines will use a diesel oxidation catalyst (DOC) and diesel particulate filter," says Resch. "This technology is the same as that being used in on-highway applications today. However, improvements have been made to accommodate the more rugged conditions and varied packaging needs encountered in off-highway applications."
John Deere continues to develop and refine the technologies it will use to meet emissions regulations for engines rated between 75 and 175 hp. "For John Deere engines with power ratings less than 75 hp, a DPF will not be used to meet Interim Tier IV emissions regulations," says Resch. "In fact, John Deere has already introduced Interim Tier IV-certified engines with power ratings between 48 and 68 hp.
"John Deere continues to investigate other technology options to meet the demands of Final Tier IV emissions regulations," he adds.
Added service requirements?
"With the addition of new systems on machines, there is the potential impact of additional service," says Bartz. "Volvo is working to minimize the need for any additional service and cost to the customer."
Cummins will require you to service the coalescing filter for the crankcase every 2,000 to 3,000 hours. It is also targeting a 5,000-hour interval for cleaning ash from the DPF. However, in order to maintain the 5,000-hour service interval, it will be important to use the approved oil classification for the engines. In the on-highway market, this is currently CJ-4.
"If you use oil other than CJ-4, it could mean that you would have to remove ash from the DPF more frequently," says Rumsey.
Beyond these two areas, there should be little in the way of additional maintenance required for the Interim Tier IV engines.
More burden on end users
In the past, the burden was mainly on the manufacturers to ensure equipment met the most current emissions regulations. But recent legislation in California could signal a turning point where the end user will also become more involved. On July 26, 2007, the California Air Resources Board (CARB) approved a regulation to reduce emissions from existing non-road diesel vehicles used in California. The regulation will require fleets to modernize and add retrofits. (See www.arb.ca.gov/msprog/ordiesel/ordiesel.htm.)
While at first glance this appears to be a California-only challenge, these regulations tend to promulgate and other states are already starting to take notice.
Many OEMs are working through their distributors to provide solutions. "John Deere engine distributors are working with customers to determine the most cost-effective compliance strategy for their fleets," says Laudick. "This includes retrofitting or transitioning a piece of equipment out of their fleet. Customers have the option of installing aftertreatment and other emissions-reduction technologies into existing engines. However, retrofitting older equipment will not be easy, and might not be cost effective because some machines cannot accommodate the installation of a DPF or other aftertreatment devices."
In addition, engine re-powers are more intensive than you might imagine. "Retrofitting can require extensive resources and equipment modification," says Laudick. "A major challenge is introducing electronic controls into an older, mechanically controlled engine.
"Other challenges include higher levels of heat rejection in Tier II and Tier III engines," he adds. "In many cases, engine retrofitting will require the addition of a charge air cooler and a new, larger cooling package."
Volvo has also been hard at work addressing this issue. "Re-power from a Tier 0 to a Tier I engine can be accomplished with relatively minor complications, but it is expensive," says Bartz. "Once re-powered with a Tier I engine, the machine may have a very short time frame until it will require retrofit." (This depends on total fleet management under the CARB calculation). This does not translate into a very attractive investment.
"Given that there is currently no CARB-approved NOx aftertreatment, the only way to reduce fleet NOx is to retire machines," says Bartz. "These old machines have the largest impact on NOx and likely need to be retired out of the fleet to meet this requirement. Re-power of old Tier 0 machines to Tier II or Tier III is technically very difficult, as this now affects the computer architecture of the engine and machine, with significant cooling system considerations."
There are aftermarket particulate filters available for some applications. The Cleaire Horizon, an active diesel particulate filter, is conditionally verified for off-road applications, and is available through California distributors Cummins West and Cummins Cal Pacific.
Cummins Emissions Solutions also has passive diesel particulate filters for off-road applications that are not CARB verified. The company is working with its technology partners to get these passive devices verified in advance of the California rules implementation.
Leading the way
Sukut Construction owns one of the largest earthmoving fleets in Southern California. The company saw the CARB regulations coming and took proactive measures. "That regulation will have a huge impact on the industry over the next decade," says Michael Bobeczko, director of marketing. "A lot of people will go out of business and it will be a whole different industry."
Currently, Sukut Construction is a leader in re-powering its Caterpillar equipment. "We have one of the cleanest fleets in the industry today," says Bobeczko. Unlike many of its competitors, Sukut is not sending its equipment to the dealers to have the conversion completed. "We do this whole process in the field in less than a week."
Sukut is transitioning its whole fleet to Tier III. "We are re-powering all of our equipment with Tier III engines," says Bobeczko. "We are replacing Tier 0 and Tier I engines. We have re-powered just about everything we can re-power."
But the nature of the regulations means this is not going to be a one-time expense. "We will be in compliance in the beginning. But as time goes on, no one is in compliance, because there is no Tier IV solution [currently available in the market]," says Bobeczko. "So all of us will have to re-power, add aftertreatment devices or replace again. That is a huge concern."
Also of concern is used equipment values. Due to the amount of equipment that is currently being dumped on the market, used equipment prices have tumbled in California.
Given the CARB regulation's far-reaching implications, this is an issue everyone across the country needs to carefully study.