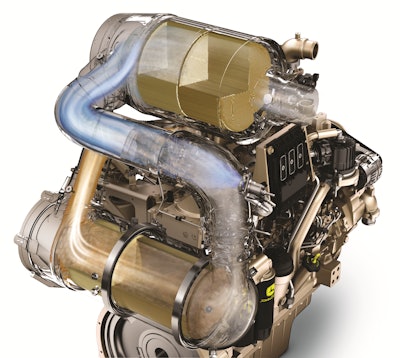
In 2019, Stage V emissions regulations will go into effect in Europe for non-road mobile machinery (NRMM) engines in the 25.5- to 751-hp power range. This next step — which will be the strictest in the world — will introduce a limit on particle number (PN) in addition to the previously required particle mass (PM) limits for engine emissions.
Though no plans are currently in place to adopt PN limits in the U.S., the design changes needed to meet Stage V are already impacting some Tier 4 Final models, and could have further impacts in future.
Back to DPFs
Many manufacturers were able to eliminate diesel particulate filters (DPFs) from smaller engines for Stage IV/Tier 4 Final, helping to save space within crowded engine compartments. With the inclusion of PN limits, it is anticipated DPFs will again be necessary to achieve Stage V compliance.
Engine Manufacturers Ready for Next Stage of Diesel Emissions Regulation
Frank Terres, executive director, Advanced Technologies – Clean Air, Tenneco Inc., says it will be necessary to have a DPF on engines above 25.5 hp, because as seen in the light-duty vehicle market, the required PN limits can only be achieved using wall-flow filters, which are considered to have the highest filtration efficiency (over 85%).
“Engines that do not utilize DPF technology have particulate levels two times higher than Stage V regulations allow,” says Dr. Xinqun Gui, manager, Engineering at John Deere Power Systems (JDPS). “Currently, DPF is the only commercially available technology that allows producers to meet Stage V engine requirements.”
Integrated Package Solutions
Packaging constraints will be one of the biggest challenges with reintroducing the DPF to existing aftertreatment systems. Space within engine compartments is already limited, especially in smaller pieces of equipment, making it difficult to include more components.
One way manufacturers look to overcome this is to use the SDPF technology being introduced for light-duty vehicles, in which the selective catalytic reduction (SCR) catalyst is coated directly onto a DPF substrate. “This [diesel oxidation catalyst] DOC + SDPF system requires only a small amount of additional space compared to the Stage IV SCR-only system,” Terres explains.
SDPF (also referred to as SCRF) systems are able to warm up faster due to their closer proximity to the vehicle’s engine than an SCR located downstream. This enables earlier NOx conversion.
According to Johnson Matthey, a manufacturer of SCRFs, these systems improve thermal management of the catalyst. They are also demanding systems and therefore may require an additional SCR/ammonia slip catalyst to maximize nitrogen oxide (NOx) conversion. Gary Simons, exhaust/emissions engineering director at Donaldson Company Inc., says these systems can impact packaging, but generally not diesel exhaust fluid (DEF) mixing performance.
JDPS will leverage a new advanced filter substrate and high-performance catalyst, says Gui, as well as emissions control calibration technologies to downsize the aftertreatment systems for its Stage V engines. The use of these solutions will reduce engine package size 39% and weight 57%. In addition, a compact mixer design will help provide greater package flexibility and easier installation.
Korneel De Rudder, exhaust/emissions development manager, Donaldson Company, says that when it comes to packaging, it often makes sense to completely redesign a machine to achieve an optimal Stage V aftertreatment layout. “However, the reality of reduced budgets forces many OEMs to update existing machines,” he says. This typically leads to the addition of extra componentry, such as a DPF.
To accommodate these redesign constraints, some manufacturers are looking to combine all of the necessary aftertreatment technologies into a single unit. Such systems are common in the on-highway truck market. Volvo Trucks and sister company Mack Trucks both introduced such systems in 2016, which include the DPF, SCR and DEF injector in a single system to reduce installation space and weight.
Donaldson will offer customers compact, fully integrated systems when possible. Reducing the size of its mixing technology enables it to package all aftertreatment components in a single unit that is still manageable for vehicle mounting. In addition, improvements to standalone mixers and mixers integrated with the DOC/DPF make it possible to package components in relatively compact modular systems.
Simons notes that in certain instances — such as for manufacturers who already use a DPF and SCR to meet Stage IV — the customer’s Stage V solution may be smaller than the one used for Stage IV. “For Stage V, it’s possible these customers will focus on optimizing the catalyst sizes and taking advantage of the improved mixing to reduce the overall package size,” he says.
OEMs completely redesigning a machine platform to meet Stage V may also benefit from the integrated, single unit option as the volume level would better justify the tooling costs. “However, if the OEM is upgrading the machine platform to the new emissions legislation (no complete redesign), one needs to be very creative to find the necessary space to integrate all the aftertreatment components,” says De Rudder. In those cases, it can be more advantageous to use multiple, smaller sized aftertreatment components that enable flexible and modular integration.
For most OEM customers, Stage V will mean extra aftertreatment components being added to their machines.
Customized to the Market
Besides the packaging challenges, including extra componentry may require global manufacturers to have different designs for different markets. “In several cases, there is a desire to use a similar aftertreatment system for Stage III, IV and V applications with the only changes between them being the catalyst content (downgrading),” says Simons.
Because the current Stage IV and U.S. Tier 4 Final regulations are relatively harmonized, it has made it easier for manufacturers to use similar designs for customers in both markets. For those that use a Donaldson system, Simons says if the system is optimized to operate at the higher dosing rate required by Stage V, it will also work for Stage III and IV without further development.
For 75.1-hp and above engines, FPT Industrial intends to meet Stage V with its next generation of SCR-only technology, HI-eSCR2 (www.oemoffhighway.com/20841622). This system adopts SCR on filter (SCRoF) technology consisting of a ceramic substrate with alternatively closed channels and SCR coating. PM filtration is integrated onto the SCR system, enabling it to comply with both the NOx and PM requirements.
The HI-eSCR2 is flexibly designed to aid installation. Up to 20 different layout solutions are possible to meet customers’ varied packaging needs. FPT says its system is also 10% smaller than others in the market, further aiding installation.
In addition, Federico Gaiazzi, FPT’s head of marketing, says there is no cooling system update or vehicle redesign required to go from the Stage IV HI-eSCR system to the new HI-eSCR2. He adds that continuing to offer an EGR-free technology will maintain the fuel efficiency, performance, reliability and durability benefits its previous aftertreatment offered for engines at lower regulation levels. The lack of exhaust gas recirculation (EGR) means there is no downtime for maintenance or active regeneration. This also eliminates the need for a heat protection device that would otherwise be required to guard against the peak temperatures of active regeneration.
SCR Advancements
De Rudder says SCR catalyst technology has improved considerably over the years, and use of state-of-the-art SCR substrates enables very high NOx conversion to be reliably achieved from small catalyst volumes. “For engine OEMs, this translates into reduced SCR catalyst volume,” he says.
Donaldson’s development of Stage V solutions has been in the works for several years, says Simons, with a primary focus on DEF mixing performance and deposit-free operation within a smaller overall package size.
By maximizing the free spray path length, and reducing or avoiding any droplet impingement on the internal walls of the exhaust system, the build-up of unwanted DEF decomposition by-products (deposits or crystals) can be avoided. For mixing, De Rudder notes that the company has been offering systems using bulk swirl motion to enhance both micro and macro scale mixing in the exhaust. “We are now at a point where we can integrate the SCR mixing in the SCR inlet, and still have a smaller space claim than what was needed for a Stage IV SCR system,” he says.
Most of the Stage V solutions represent the next level of mixing technology. “Often, the transition from Stage IV to V has been accompanied by an increase in the engine out NOx, caused by the reduction/removal of EGR,” Simons explains. “This has forced the mixing performance to increase, especially when it comes to operating deposit free.
“Two of the most critical specifications that dictate the mixing technology are the [DEF] dosing rate and backpressure,” he continues. “It is generally true that the higher the mixing needed, the higher the backpressure will be in order to operate at the best performance [level] and deposit free. With lower dosing rates, it is possible to simplify the mixing system and keep the backpressure as low as possible.”
Reducing or removing EGR can cause challenges when calibrating the DEF dosing algorithm. “No- or low-EGR engines have high raw NOx emissions which demand a high-efficiency SCR system. Often, conversion rates in the range of 96% to 99% are required,” says De Rudder. “However, at these efficiency levels, any minor local deviations in NOx conversion over the SCR catalyst can lead to a major difference in downstream NOx sensor readings.”
The NOx sensor reads absolute values in the range of 10 parts per million (ppm), and De Rudder says if that reading is off by 1 or 2 ppms, it can cause major issues with the DEF dosing algorithm. Because of this, mixers downstream of the SCR catalyst have become more common in system designs to ensure good NOx sensor readings.
Donaldson provides non-impingement swirl mixing systems that are sensitive to DEF crystallization (avoiding plugging the exhaust) and offer high mixing performance. While the majority of the industry has utilized impact-based mixers, today Donaldson sees many embracing swirl-based mixing systems. “There is a directional trend toward more compact aftertreatment systems and less volume being allocated for mixing,” De Rudder says. “More often than not, these systems use swirling flow to enhance mixing.”
“Both swirl-type mixing and next-generation impingement designs are being proposed,” notes Simons. “Time will tell if they are successful.”
Terres points out that active or passive thermal management solutions can be beneficial in overcoming the challenges associated with reducing or removing EGR, as well. Such solutions from Tenneco include low thermal inertia and air gap insulated manifolds, high-efficiency insulation technology and Micro Thermal Units, each of which provides active heat to support improved aftertreatment system efficiency. “We have also developed highly efficient compact mixers that allow for urea processing at low temperatures without the formation of undesired urea deposits,” he adds.